Если вы едете на поезде по России — скорее всего, вы смотрите в окно, сделанное на нашем предприятии. Ломоносовский опытный завод в Ленинградской области — основной в стране производитель и поставщик комплектующих для железнодорожного транспорта и поездов метро. Наша продукция также экспортируется в страны Европы и Прибалтики. Предприятию более 25 лет. С 2004 года завод входит в состав «Трансмашхолдинга» — крупнейшего поставщика подвижного состава для российского транспорта, сейчас принадлежит дочерней структуре «Трансмашхолдинга».
На заводе работает почти 1000 человек, мы используем около 400 единиц оборудования. В том числе — более 40 станков с программным управлением. Наша служба эксплуатации и ремонта следит за тем, чтобы техника как можно реже выходила из строя. Что для этого требуется? Тщательная диагностика, всесторонний анализ работы оборудования и отлаженный процесс техобслуживания.
С 2011 года на всех предприятиях применяется Производственная система ТМХ, основанная на концепции «бережливого производства» (Lean). Ее основные цели:
- сокращение затрат,
- оптимизация сроков создания продукции,
- сокращение производственных и складских площадей,
- гарантия поставки продукции заказчику,
- высокое качество при согласованной с заказчиком
- стоимости.
Дважды в год на заводах холдинга проходят производственные аудиты с участием экспертов из головной компании и ведущих специалистов всех компаний холдинга. Во время аудита каждого предприятия в ключевом документе развития производственной системы «бережливого производства» — дорожной карте — анализируется достижение заявленных целевых показателей. Дорожная карта содержит требования по 5 направлениям развития:
- менеджмент,
- подготовка производства,
- качество,
- производство,
- цепочка поставок.
В разделе дорожной карты «Управление производственными активами» необходимо достижение следующих целей:
- Показатели надежности оборудования. Уровень поломок / коэффициент технической готовности, MTBF (Mean Time Between Failures — средняя продолжительность работы между отказами, характеризует надежность восстанавливаемого прибора, устройства или технической системы), MTTR (Mean Time To Restoration — среднее время до восстановления работоспособности).
- Анализ и оптимизация затрат на обслуживание и ремонт оборудования.
Для достижения этих целей нам требовались:
- инструмент систематизированного (документированного и структурированного) сбора-регистрации и анализа показателей коэффициента технической готовности / аварийности, MTBF, MTTR;
- анализ по определению 20 единиц оборудования с наиболее высоким уровнем поломок;
- анализ поломок и потерь, связанных с организацией внеплановых ремонтов;
- четкое разделение материальных и трудовых затрат на ремонты и обслуживание по каждой единице основного оборудования через ордерную организацию работ с выдачей нарядов, в которых отображаются все затраты на ремонты (заказ-наряд);
- анализ целевых показателей, на основании которых разрабатываются планы мероприятий и стандарты по достижению целевых уровней.
Мы искали информационную систему, которая позволит нам выполнить цели «бережливого производства». Выбрали «1С:ТОИР» как гибкое решение, в котором можно построить аналитику по требованиям Lean, данные из системы позволяют ее получить. Поэтому мы обратились к разработчику системы «1С:ТОИР» — компании «Деснол Софт»
С чего для нас начался проект автоматизации управления ремонтами? Сначала построили базу оборудования. В ней содержатся паспорта всей нашей техники, схемы и технические карты. Оборудование в базе (около 400 единиц) поделили на объекты ремонта, их сейчас более 1500 — в каких-то случаях это целые единицы техники, в каких-то — отдельные детали, узлы, механизмы. К производственному оборудованию в базе в качестве объектов ремонта мы добавили здания и помещения. На втором этапе проекта «1С:ТОИР» адаптировали к нашим потребностям, настроили интеграции, вписали систему в существующий на заводе IT-ландшафт. Одновременно с этим «Деснол Софт» провел обучение сотрудников предприятия работе в системе. На третьем этапе систему ввели в опытно-промышленную эксплуатацию, началось ее практическое использование. В «1С:ТОИР» работают 50 сотрудников предприятия. Системой активно пользуются как специалисты ремонтной службы, так и сотрудники производства. Для них в системе сформированы специальные автоматизированные рабочие места — АРМы.АРМ «Технический специалист» нужен для определения вида работ по заявке от производства. Заявка о неисправности поступает в ремонтную службу, специалист определяет, что понадобится: ремонт или какое-то мероприятие в рамках техобслуживания.
Рабочее место «Мастер» разработано для регистрации заявок на ремонт. В него добавили цветовую индикацию и пиктограммы — статусы выполнения ремонтных работ стали нагляднее. Также добавили реквизиты, отчеты и формы документов, которые помогают лучше контролировать работы по заявкам.
АРМ для ведения графиков работы оборудования позволяет учитывать различные графики. В дальнейшем на основании этих графиков рассчитываются все основные показатели работы оборудования, строится ключевая аналитика. В зависимости от загрузки производства устанавливаются различные графики: 2 смены по 12 часов, то есть круглосуточно, или 8 часов 5 дней в неделю. «1С:ТОИР» дает возможность учитывать фактическое время простоя и работы каждой единицы техники. Так мы видим реалистичную статистику. А это в дальнейшем позволяет сформировать достоверную отчетность.
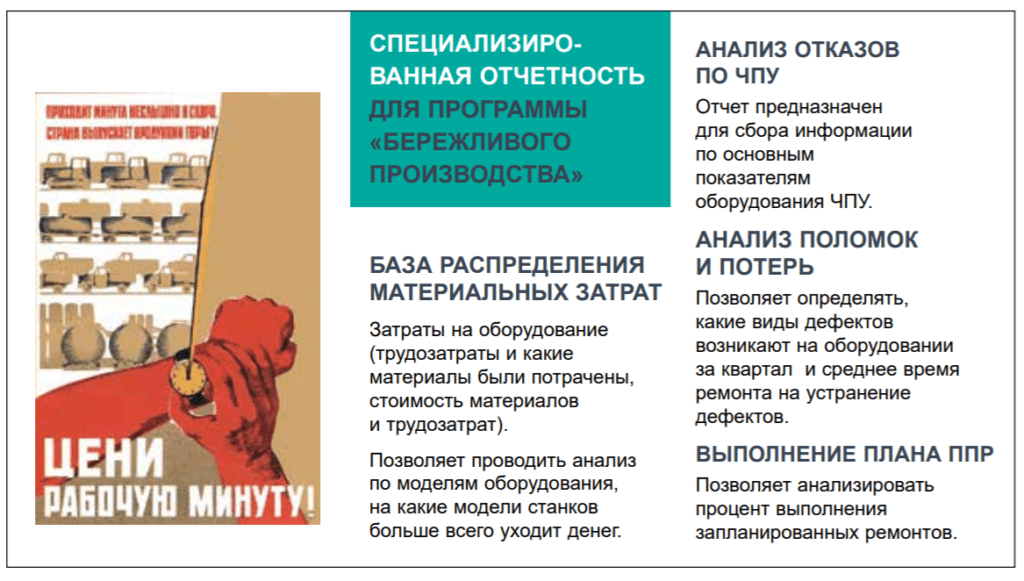
Для выполнения целей «бережливого производства» «1С:ТОИР» формирует 11 специальных отчетов. Система помогает нам получить такие показатели, как среднее время ремонта по каждой единице оборудования, причины и частота ремонтов по каждой единице оборудования, доля затрат на ремонты в бюджете предприятия и т.д. Мы можем строить реальную аналитику для конкретного производства и отображать её в виде удобных для восприятия графиков. Анализ отчетов позволяет совершенствовать наши методы управления оборудованием и достичь главной цели – свести внеплановые простои оборудования к нулю.
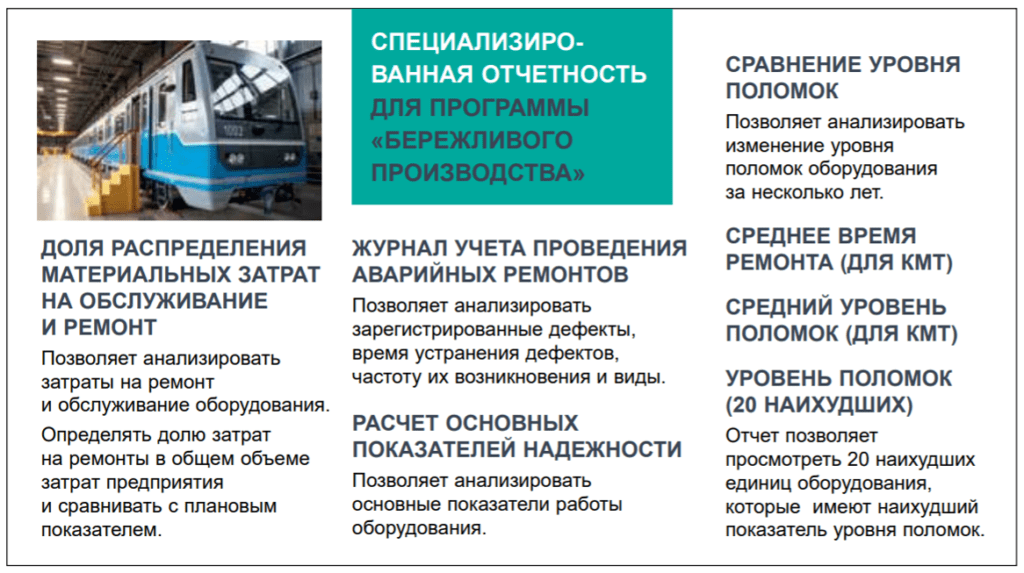
Управление техобслуживанием мы ведем в «1С:ТОИР», а для управления ресурсами предприятия в целом наш завод использует систему «1С:ERP». Между ними настроен обмен справочниками и документами, которые отражают потребление и получение материалов. Таким образом, у нас есть все данные для того, чтобы дать ремонтной службе необходимое и при этом расходовать ровно столько средств, сколько нужно. Мы изжили проблемы ручного построения отчетов, непрозрачных процессов и бумажного документооборота. Следующий фокус внимания — управление на основе точных данных. В перспективе мы рассматриваем возможность обмена между «1С:ТОИР» и системой мониторинга промышленного оборудования АИС «Диспетчер», модуль для этого также разработан «Деснол Софт».
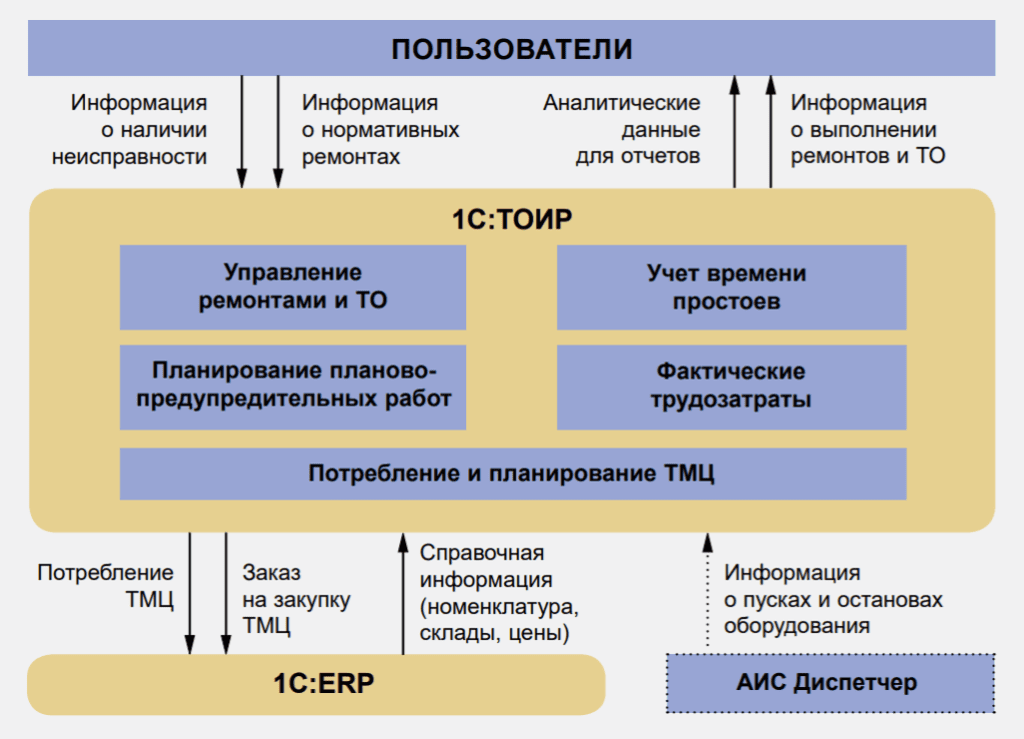
Спустя несколько месяцев постоянной работы в системе мы видим серьезный прогресс в подготовке управленческой отчетности. Раньше требовалось до трех дней, чтобы собрать и сопоставить информацию из бумажных журналов. Сейчас информация накапливается планомерно, день за днем, а отчеты строятся автоматически. Данные теперь вносит не руководитель подразделения, а несколько операторов оборудования. Это одновременно повышает скорость обработки информации, снижает количество возможных ошибок и высвобождает дорогостоящее время руководителей для основной работы.
Мы получили возможность реально экономить, повысить качество информации о состоянии основных фондов и быстрее двигаться к цели. Сегодня можно сказать, что «1С:ТОИР» стал неотъемлемой частью Lean для нашего завода.
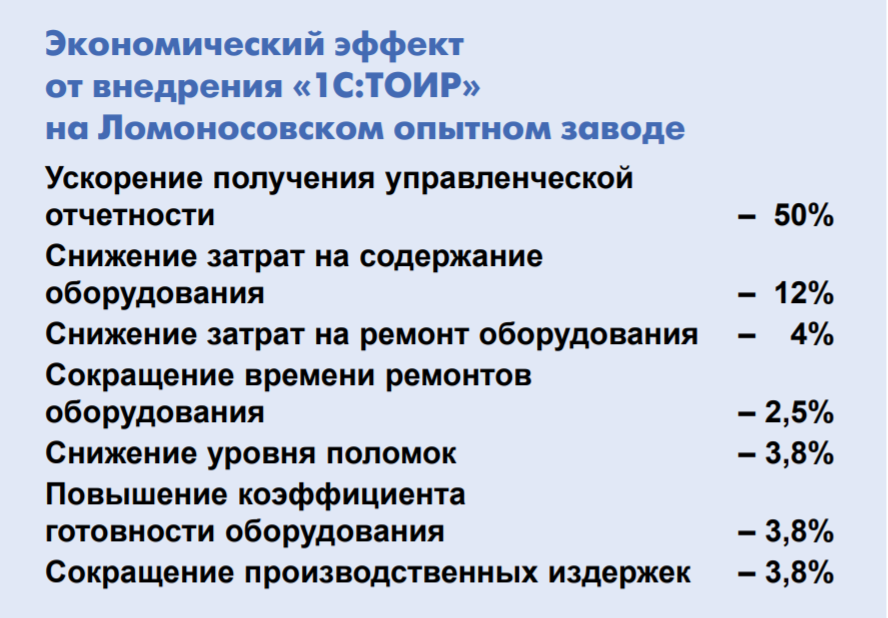
Журнал Prostoev.NET № 1(22) 2020
Евгений САВЕЛЬЕВ, руководитель департамента информационных технологий «Обособленное подразделение КСК Санкт-Петербург» ООО «Ключевые системы и компоненты»