Последние несколько лет в нашей стране на различных уровнях активно обсуждаются вопросы, связанные с практическим внедрением цифровых технологий, объединенных общей концепцией «Индустрия 4.0». В настоящее время правительством Российской Федерации утверждена программа «Цифровая экономика», выделяются бюджетные средства на создание различных видов цифровых платформ, а собственники и топ-менеджеры крупных компаний на страницах изданий отчитываются об успехах «перехода на цифру».
Подавляющее большинство экспертов уверены в неизбежности цифровой трансформации и ключевых преимуществах тех компаний, которым удалось быстро и эффективно перейти к новым парадигмам управления.
Однако наиболее авторитетные аналитики призывают не впадать в эйфорию и взвешенно подходить к внедрению цифровых технологий, трезво сопоставляя затраты и ожидаемый эффект.
В условиях массового увлечения цифровыми технологиями управленцы большинства крупных и средних промышленных производств также предпринимают попытки внедрения передовых решений «Индустрии 4.0», основанных на больших данных, искусственном интеллекте, дополненной реальности, виртуальных двойниках, 3D-печати (рис. 1). Вероятно, по мере развития и совершенствования каждая из этих технологий найдет свою практическую область применения и позволит получать значительный экономический эффект от внедрения. Однако в настоящее время большинство отечественных и зарубежных специалистов в области управления производством отдают предпочтение предиктивной аналитике как наиболее востребованному и экономически эффективному инструменту цифровизации в промышленности. По их оценкам, грамотное внедрение предиктивного технического обслуживания и ремонта (ТОиР) производственных активов обеспечивает исключение аварийности, повышение производительности, а также существенное сокращение затрат на поддержание активов в работоспособном состоянии.
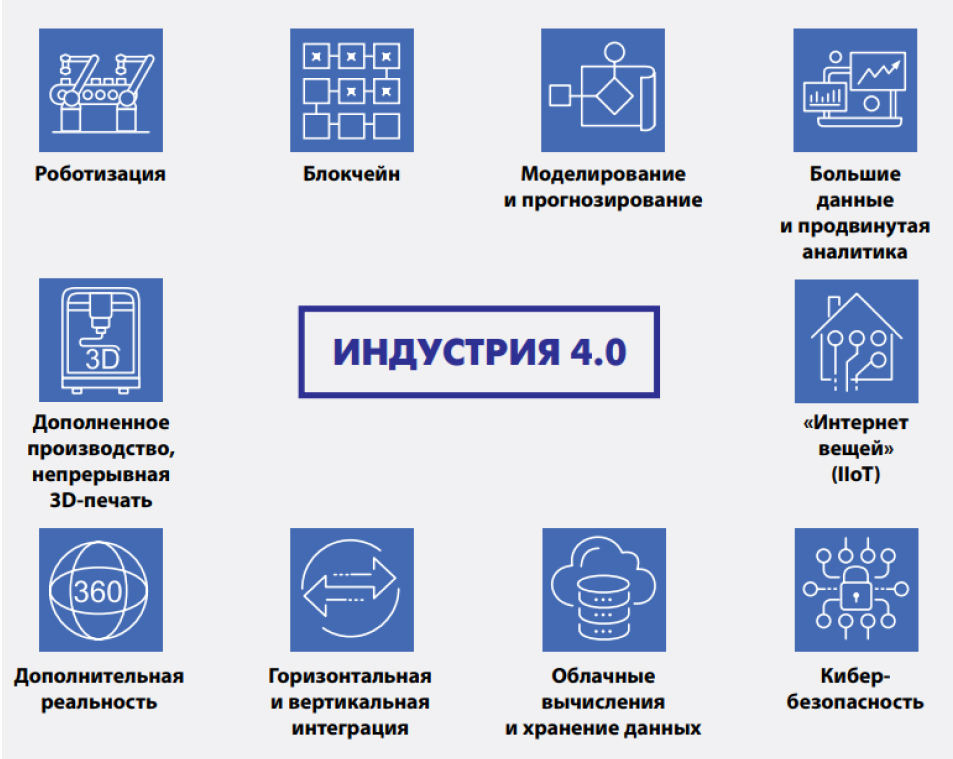
По наиболее распространенному определению, предиктивная (предсказательная или прогнозная) аналитика — класс методов анализа данных, используемый для прогнозирования будущего поведения объектов и субъектов с целью принятия оптимальных решений. Предиктивная аналитика использует статистические методы, методы интеллектуального анализа данных, теории игр и оценивает текущие и исторические факты для составления предсказаний о будущих событиях. Первые документальные попытки использования предиктивного анализа (в то время это называлось предсказаниями), основанного на субъективных факторах, были зафиксированы еще в Древней Греции и Риме (рис. 2а). Позднее математики и астрономы разных эпох, используя имеющуюся статистику, предсказывали периоды разлива рек и засухи, солнечные затмения, наводнения (рис. 2б). В наши дни предиктивный анализ уже на базе современного математического аппарата традиционно используется в банковском секторе, страховании, розничной торговле, здравоохранении и других областях (рис. 2в). Сегодня наибольшей популярностью среди населения пользуются сервисы (рис. 2г), основанные на краткосрочном прогнозе явлений или событий (погоды, загруженности дорог и пр.) на базе нейросетевых моделей.
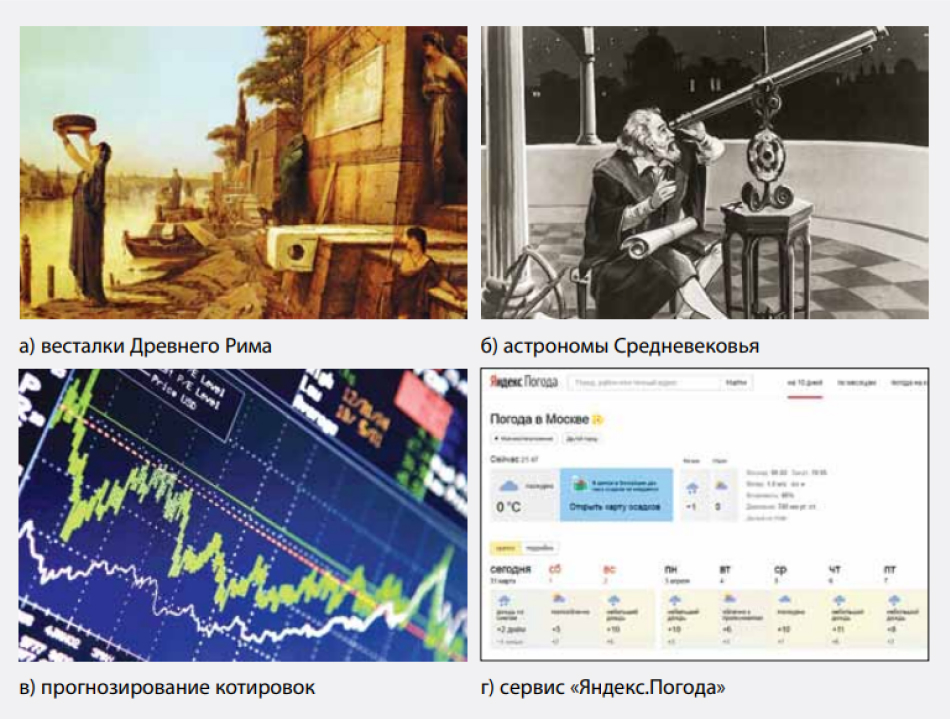
Наиболее востребованная сфера практического применения предиктивного анализа в промышленности — использование сведений о прогнозируемом состоянии активов для планирования объемов производства, сроков проведения необходимых ремонтных и восстановительных мероприятий и оценки финансовых показателей. Выгоды применения предиктивного анализа очевидны: своевременно получая информацию о текущем состоянии оборудования, существующих дефектах, скорости их развития, остаточном ресурсе, можно управлять надежностью производства и принимать компетентные решения, основанные на объективных и достоверных данных, существенно повышая экономический эффект (рис. 3). Поэтому в настоящее время многие промышленные предприятия в нашей стране, в русле стратегии глобальной цифровизации и развития промышленного интернета вещей (IIoT), задумываются о внедрении предиктивного анализа или уже реализуют первые пилотные проекты. Однако в условиях ажиотажного спроса на подобные решения (по нашим оценкам, рост количества компаний, декларирующих свои предиктивные компетенции в промышленности, происходит со значительным опережением закона Мура) важно трезво оценивать существующее положение дел на предприятии и понимать базовые принципы, на которых основывается любая предиктивная аналитика.
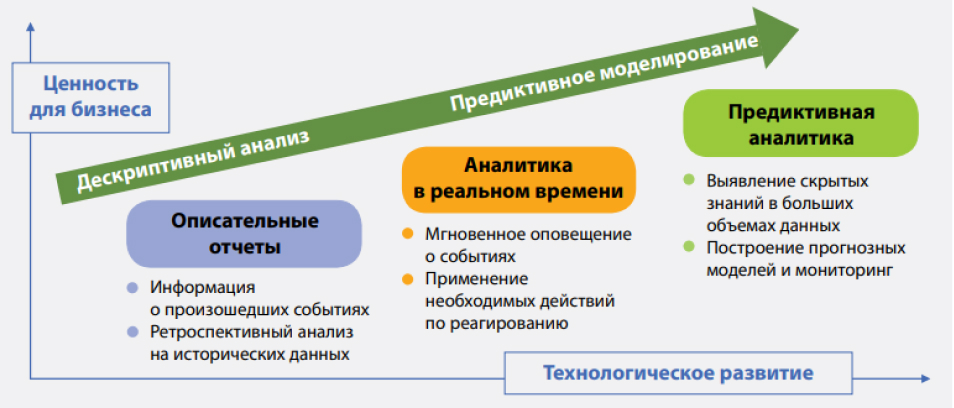
Большинство экспертов выделяют четыре основных этапа внедрения методов предиктивного анализа: сбор данных, обработка данных, анализ данных и собственно прогноз (рис. 4). Каждый этап имеет свои особенности и подходы к реализации, выходящие за рамки данной публикации, однако, как ни парадоксально, в подавляющем большинстве случаев основные трудности возникают уже в начале пути. Использование «неверных данных» или «несостоятельной выборки» может привести к полной остановке проекта либо низкому качеству получаемых прогнозных моделей. И тот и другой варианты развития событий чреваты не только потерями значительных инвестиций, но и формированием негативного отношения к самой идее цифровизации, что в среднесрочной перспективе грозит существенным технологическим отставанием. Поэтому первостепенной задачей, предшествующей внедрению любых видов предиктивного анализа, является выбор данных, необходимых для построения состоятельных предиктивных моделей. Рассмотрим более подробно вопрос полноты данных для построения предиктивных моделей применительно к наиболее важной группе производственных активов современных промышленных предприятий — динамическому оборудованию (это и насосно-компрессорные агрегаты, и прокатные станы металлургии, и бумагоделательные машины, и грузоподъемные механизмы, и огромное количество других видов роторных механизмов).
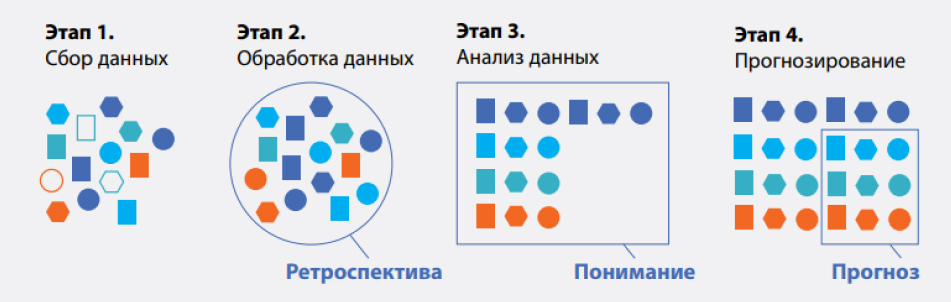
Практика применения различных методов диагностики показывает, что до 80% сведений о текущем состоянии динамического оборудования содержат в себе различные параметры вибрации, а оставшиеся 20% приходятся на силу тока, температуру и ультразвук (УЗК). Очевидно, что контролируя данные параметры с необходимой периодичностью и передавая их в цифровом виде в единую базу данных, можно получать информацию, достаточную для построения состоятельных предиктивных моделей. На первый взгляд, данные задачи успешно могут решать и существующие системы АСУ ТП, и многочисленные MES-системы, и системы управления предприятием на базе EAM/ERP решений. За кажущейся простотой скрывается множество подводных камней, способных потопить не один проект.
Сложность заключается в том, что все указанные системы оперируют сводными показателями или усредненными значениями — это общий уровень вибрации, усредненная сила тока, значение температуры в единичной точке и пр. Наиболее важная информация о состоянии оборудования и дефектах его узлов содержится именно в гигабайтах и терабайтах динамических данных (формах сигналов, спектрах вибрации и тока, термограммах и пр.), которые хранятся в памяти специализированных переносных или стационарных диагностических приборов и программных комплексов, а в данных системах отсутствуют (рис. 5). Попытки построить предиктивный анализ только на основе данных АСУ ТП, MES или EAM систем в подавляющем большинстве случаев обречены на неудачу. Такие попытки достаточно точно характеризует известный показатель «средняя температура по больнице». Очевидно, что по данной температуре нет возможности ни оценить здоровье отдельных пациентов, ни охарактеризовать в целом работу самого заведения. Проводя аналогию из финансового сектора: нет никакой возможности оценить динамику изменения стоимости акций отдельных компаний, основываясь только на знании текущего курса национальной валюты, и ни один брокер даже не будет пытаться этого делать.
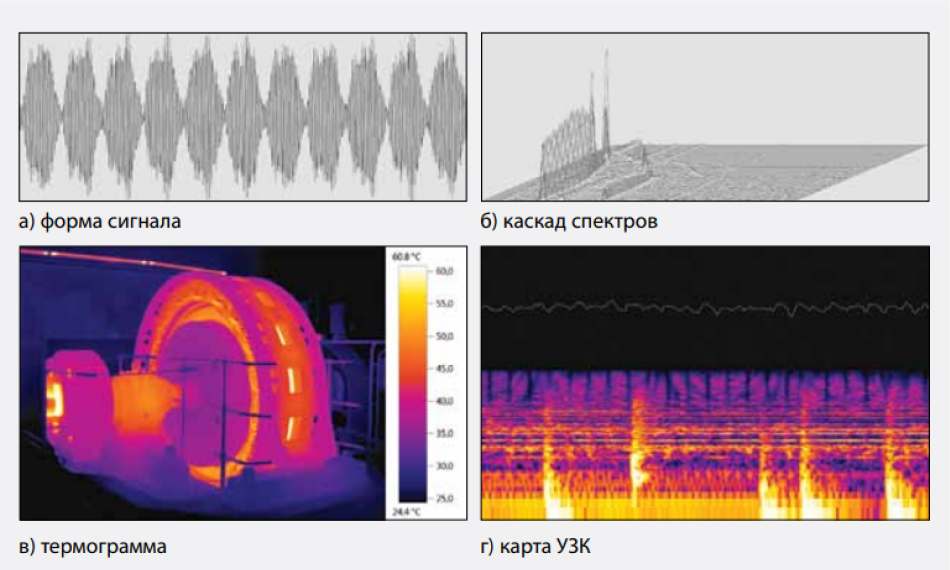
Уместен вопрос: не могут ли отдельные специализированные диагностические приборы и системы заниматься предиктивной аналитикой в рамках всего предприятия? К сожалению, ответ также отрицательный. Существующие диагностические программно-аппаратные комплексы имеют локальную область применения, их возможности ограничиваются, как правило, только каким-то одним методом диагностики. Кроме того, данные комплексы не имеют важнейшей информации о технологических режимах и проводимых мероприятиях ТОиР, которые оказывают существенное влияние на изменение вибрации и температуры, что не позволяет им с высокой вероятностью строить прогноз остаточного ресурса. Максимум, на что способны подобные решения, — хранить большие массивы данных для ручного анализа и поддерживать алгоритмы автоматизированной (или автоматической) поузловой диагностики на базе экспертных систем по результатам последних измерений. Возвращаясь к аналогии из финансового сектора, данная ситуация напоминает попытку спрогнозировать поведение всего рынка ценных бумаг нам основе информации о стоимости акций только одной компании, причем без учета внешних макроэкономических факторов.
Общемировая практика показывает, что для построения состоятельных предиктивных моделей, описывающих поведение большинства видов динамического оборудования, требуется совместный анализ следующей информации, сгруппированной по источникам:
- АСУ ТП: сведения о технологическом процессе и текущих режимах работы – мгновенные дискретные значения вибрации, частоты вращения, температуры, тока, давления и пр.
- Мобильный ТОиР: результаты визуального контроля, дискретные значения вибрации и температуры, получаемые в ходе ежесменных инспекций технологическим или оперативным персоналом.
- Переносные диагностические приборы: результаты периодических измерений различных динамических данных (сигналов и спектров вибрации, термограмм, карт УЗК и пр.) силами диагностических служб или цехового персонала.
- Стационарные диагностические системы: результаты постоянных измерений различных динамических данных (сигналов и спектров вибрации и пр.) наиболее ответственного и критичного оборудования в режиме реального времени.
- Модули ТОиР (общезаводские и цеховые): сведения о проводимых технических обслуживаниях и ремонтах, входном контроле, балансировках, центровках.
На многих промышленных предприятиях уже установлены современные системы АСУ ТП, используется различное диагностическое оборудование и внедрены программные решения классов MES, EAM/ERP, поэтому менеджмент часто пребывает в иллюзиях полноты централизованной информации и готовности к цифровой трансформации с использованием предиктивной аналитики. По факту, все данные, необходимые для построения предиктивных моделей, действительно существуют, но находятся в различных локальных базах закрытых форматов (далеко не всегда эти данные оцифрованы) и не могут быть использованы для настройки предиктивных моделей (рис. 6). Усугубляет данную ситуацию многообразие несовместимых аппаратнопрограммных средств, получившее название «зоопарк решений». Некоторые крупные промышленные предприятия имеют диагностические приборы и системы сразу нескольких различных производителей, которые несовместимы друг с другом ни на программном, ни на аппаратном уровнях, а также десятки несинхронизируемых систем АСУ ТП и MES.
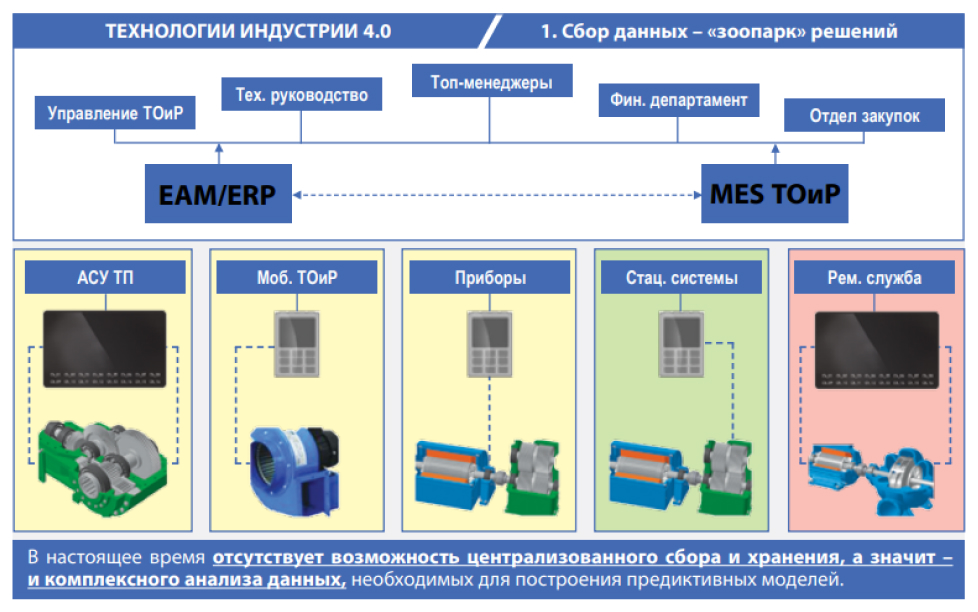
Таким образом, основной задачей, предшествующей внедрению предиктивной аналитики и других технологий «Индустрии 4.0», является внедрение общезаводских программных платформ, которые способны объединить существующую информацию о текущем состоянии оборудования из локальных хранилищ в единую сетевую многопользовательскую базу, обработать собранные массивы данных с применением современного математического аппарата и передать результаты диагностики для принятия компетентных решений по организации эффективной стратегии ТОиР. Данные программные цифровые платформы являются важным связующим звеном между устройствами «полевого» уровня и системами управления предприятием на основе предиктивных моделей, поэтому требования к подобным решениям достаточно высоки: помимо надежности, функциональности, удобства использования, гибкости настройки и адаптации, большое значение имеют такие критерии, как совместимость и интегрируемость.
Совместимость. Программный комплекс должен поддерживать взаимодействие с разными видами измерительных систем различных производителей: переносными, стендовыми, стационарными, а также приборами обходчиков, балансировочными станками, центровщиками и пр. Результаты измерений, получаемые с использованием всех измерительных систем, должны записываться в единую диагностическую базу для последующего просмотра и совместного анализа. Данное требование является наиболее критичным, так как многие производители оборудования поддерживают уникальные неунифицированные протоколы приема/передачи данных. Кроме того, программный комплекс должен обеспечивать совместное хранение и анализ всех необходимых динамических и статических данных различных методов контроля (форм сигналов и спектров вибрации, спектров токов, термограмм, карт УЗК и пр.).
Интегрируемость. Для достоверного анализа и интерпретации полученных результатов измерений необходима информация о технологических процессах, режимах работы, проводимых мероприятиях ТОиР и пр. Эти сведения оказывают существенное влияние на оценку текущего состояния оборудования и должны учитываться как в ручном, так и в автоматическом режимах при построении достоверных диагностических моделей. Поэтому в программном комплексе должны быть организованы гибкие механизмы взаимодействия с внешними аппаратными и программными системами. В единую базу данных должна импортироваться необходимая информация из АСУ и SCADA систем, а результаты диагностики оборудования с поузловым перечнем неисправностей — экспортироваться в ремонтные модули EAM/ERP систем.
До недавнего времени ни один программный продукт не удовлетворял в полной мере данным требованиям и не обеспечивал одновременно централизованный сбор, хранение, обработку и передачу данных, что являлось серьезным препятствием для внедрения предиктивного анализа. Ситуация изменилась несколько лет назад, когда на российском рынке появился первый отечественный программный продукт — цифровая диагностическая платформа нового поколения SAFE PLANT. Благодаря поддержке закрытых протоколов обмена данными различных производителей платформа SAFE PLANT обеспечивает совместимость с большинством типов существующих «полевых» устройств. В платформе реализован механизм хранения, просмотра и анализа больших данных, экспертная система смешанного типа с предустановленными и пользовательскими правилами для раннего распознавания свыше ста видов неисправностей большинства типов оборудования, а также настраиваемые нейросетевые модели. Благодаря гибкой сетевой архитектуре и поддержке современных протоколов обмена с возможностью привязки объектов базы к объектам активов осуществляется эффективное взаимодействие с внешними базами данных. Информация из АСУ ТП о режимах работы оборудования, сведения о ремонтах из журналов ТОиР в автоматическом режиме передаются в SAFE PLANT. После комплексного анализа данных результаты диагностики с перечнем выявленных неисправностей экспортируются из SAFE PLANT в любые используемые EAM/ERP системы ведущих мировых и российских производителей либо внешние системы предиктивного анализа (рис. 7).
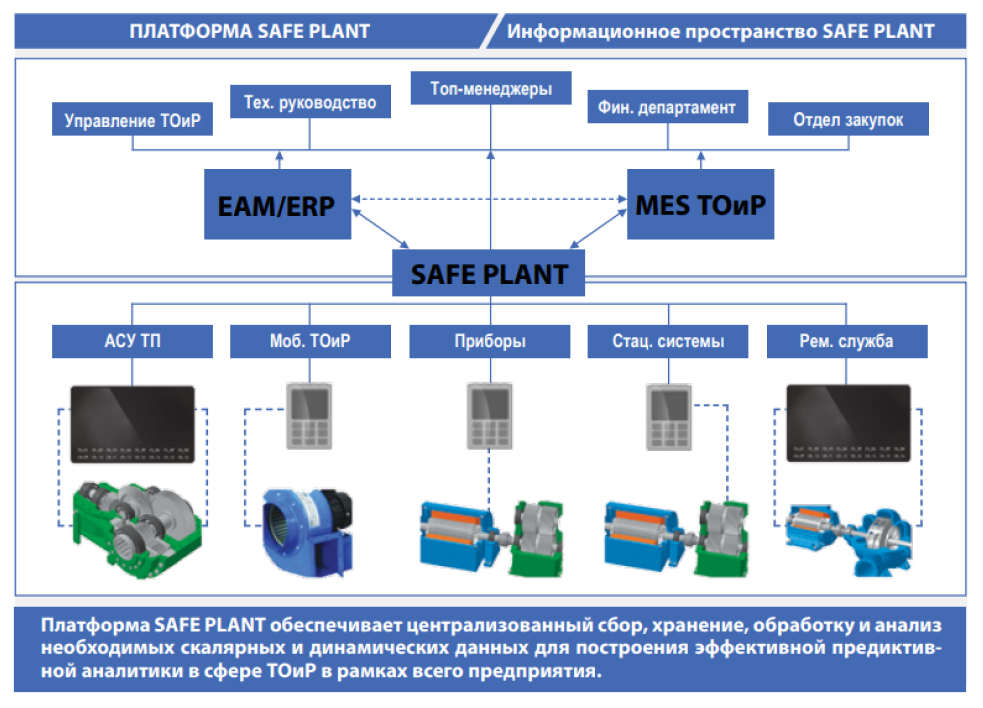
Внедрение программной цифровой платформы SAFE PLANT обеспечивает единую диагностическую базу данных с актуальной информацией для построения эффективных моделей предиктивного анализа всего парка технологического оборудования, высокую скорость передачи информации и принятия решений, а также автоматическое выявление неисправностей на ранних стадиях развития. В результате топ-менеджеры и собственники предприятий получают объективную и независимую оценку состояния оборудования для планирования инвестиций в модернизацию и обновление парка оборудования на основе данных об остаточном ресурсе. Высокая эффективность практического внедрения единой диагностической платформы SAFE PLANT на заводах ведущих отечественных предприятий (ПАО «Газпром», ПАО «НК Роснефть», ПАО «Лукойл», ПАО «Транснефть», МХК «Еврохим», ПАО «Фосагро», ПАО «Уралкалий» и др.) подтверждается не только существенным ростом экономических показателей за счет снижения расходов на закупку запасных частей, исключения простоев, сокращения численности персонала и перехода к ремонтам по состоянию на основе прогнозирования, но и возможностью внедрения новых достижений Четвертой промышленной революции в сфере ТОиР, объединенных концепцией «Индустрия 4.0».
Если у вас еще не внедрена подобная интеграционная платформа, позволяющая объединить и проанализировать результаты диагностических измерений приборов и систем различных методов контроля, данные АСУ ТП и сведения о ТОиР в рамках единой сетевой базы данных, задумайтесь еще раз: а действительно ли ваше предприятие готово к предиктивной аналитике?
Журнал Prostoev.NET № 1(18) 2019
А.Е. Сушко, к.т.н., генеральный директор ООО НПО «ДИАТЕХ», Москва