Любая история о ремонтниках должна начинаться с упоминания о самом первом механике – Архимеде из Сиракуз, который выполнил классификацию простых механизмов: рычаг, клин, блок, ворот и винт. Эти простые механизмы служили и до сих пор служат для решения самых различных инженерных задач, в том числе и в современных машинах, являясь основой механического оборудования.
Однако в Древней Греции ремонт механизмов еще не был приоритетной задачей, чаще всего было проще изготовить новый. Так продолжалось достаточно долго – и в средневековой Европе, и в эпоху ренессанса и барокко.
Безусловно, механизмы на действующих предприятиях ремонтировали, следили за их состоянием. Невозможно предположить, что первая в мире заводская паровая машина – творение великого русского механика Ивана Ивановича Ползунова – могла работать без элементов технического обслуживания. То же самое можно сказать о первых русских паровозах и одной из первых в мире железных дорог с паровой тягой, которые были созданы уральскими механиками Ефимом Алексеевичем и Мироном Ефимовичем Черепановыми.
Наиболее известным в России примером проведения ремонта, как комплекса мероприятий по приведению изделия в работоспособное состояние, является восстановление функций часового автомата «Павлин» (рис. 1) работы мастерской английского механика Джеймса Кокса. В 1777 году знаменитый часовой автомат из позолоченной меди был приобретен князем Григорием Александровичем Потемкиным для Эрмитажа государыни Екатерины II. Для перевозки механизм был разобран. В России собрал эти часы Иван Петрович Кулибин, которому их доставили в нескольких корзинах в виде груды деталей, причем некоторые из них оказались повреждены, других – недоставало. Высоко ценились его труды, как замечательного новатора в деле разработки научных приборов, часовых механизмов, транспорта, связи, осветительной техники, но способность разобраться в иностранном механизме, понять его устройство, технологию изготовления деталей, найти или создать аналоги – это, пожалуй, один из первых примеров успешного импортозамещения в нашей стране.
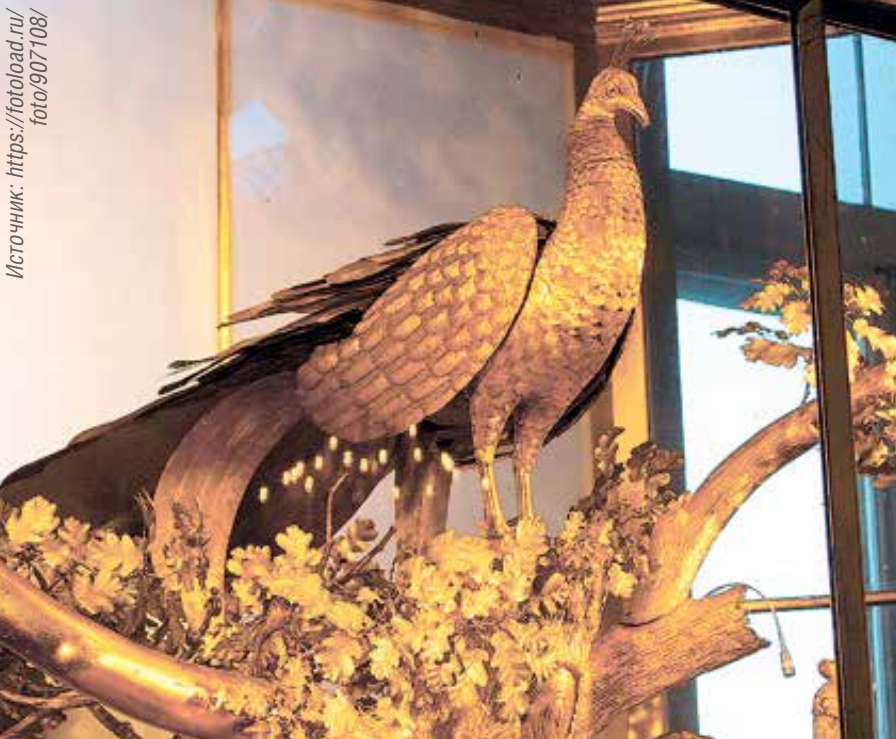
Основой нынешней цивилизации являются сплавы железа и углерода – сталь и чугун. Развитие человечества на протяжении тысячелетий происходило благодаря совершенствованию технологии получения и использования этих сплавов. Таким образом, современная промышленность во многом является результатом преобразования и использования железа. Поэтому наш рассказ об истории, вопросах и решениях в сфере инженерной механики будет во многом о специфике работы на металлургических предприятиях. Металлургические машины, ввиду многообразия конструкций, условий эксплуатации, уникальности изготовления, представляют пример наиболее сложной задачи для организации процессов технического обслуживания и ремонта (ТОиР) для обеспечения непрерывности технологического процесса.
Появление инженеров-механиков
Исторически появление профессии относят к 30 октября 1854 года, когда в Российском императорском флоте был образован Корпус инженеров-механиков. Это – время Крымской войны 1853-1856 годов, время героической обороны Севастополя. Именно тогда выяснилось, что парусные корабли потеряли практическую ценность как боевые единицы. Противники имели значительный перевес по всем типам кораблей, а паровых линкоров в российском флоте не было вообще. Использование кораблей с паровым двигателем (рис. 2) показало их преимущества и определило перспективы развития.
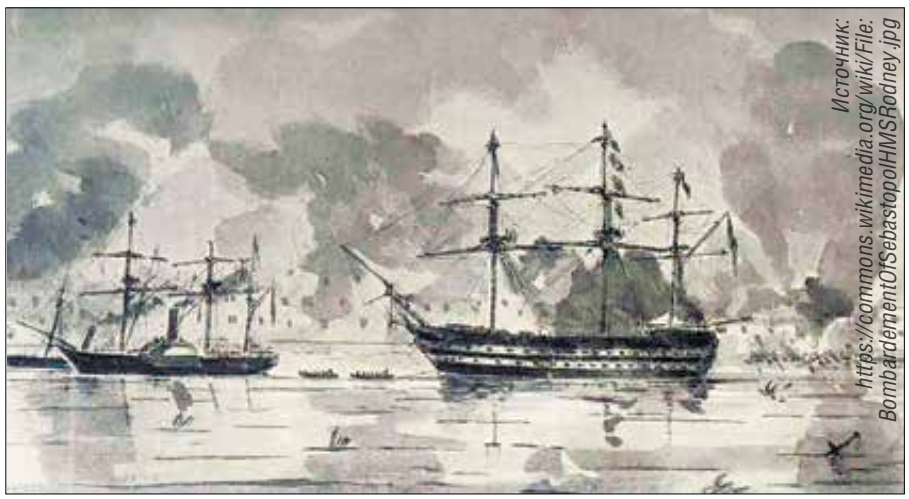
Очевидной стала необходимость создания парового броненосного флота и сети железных дорог для решения логистических задач, что предопределило развитие промышленности России на окончание XIX и начало XX веков. Именно тогда начали закладываться основные принципы ТОиР механического оборудования, в дальнейшем получившие свое продолжение при обеспечении безотказности металлургических машин.
Обслуживание боевых кораблей и паровозов имело как различия, так и схожие черты.
ТОиР на флоте
Техническое состояние паровой машины, рулевого управления, механизмов наведения, поворота башен для боевых кораблей является основой живучести и эффективности. Поэтому роль машинной команды на крейсере в конце XIX века стала более ответственной. На это указывает количественный состав машинных команд легендарных крейсеров российского флота – «Варяга» и «Авроры» (рис. 3).
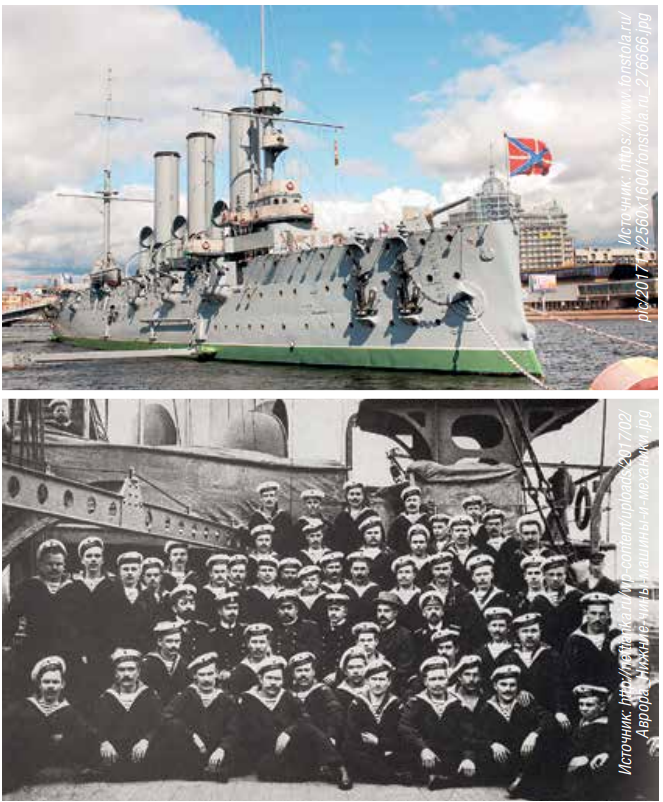
Отсутствие длительного опыта эксплуатации паровых машин на кораблях начала XX века, уникальность оборудования, высокие требования к надежности обуславливали необходимость применения при конструировании больших запасов прочности. Условия работы оборудования характеризовались переменными, иногда максимальными нагрузками. Эксплуатационная надежность (безотказность) уникального корабельного оборудования (рис. 4) обеспечивалась за счет четко организованной системы осмотров и операций по техническому обслуживанию. Для этого необходим был обученный персонал, умеющий работать в стесненных условиях, технически грамотный и ответственный.
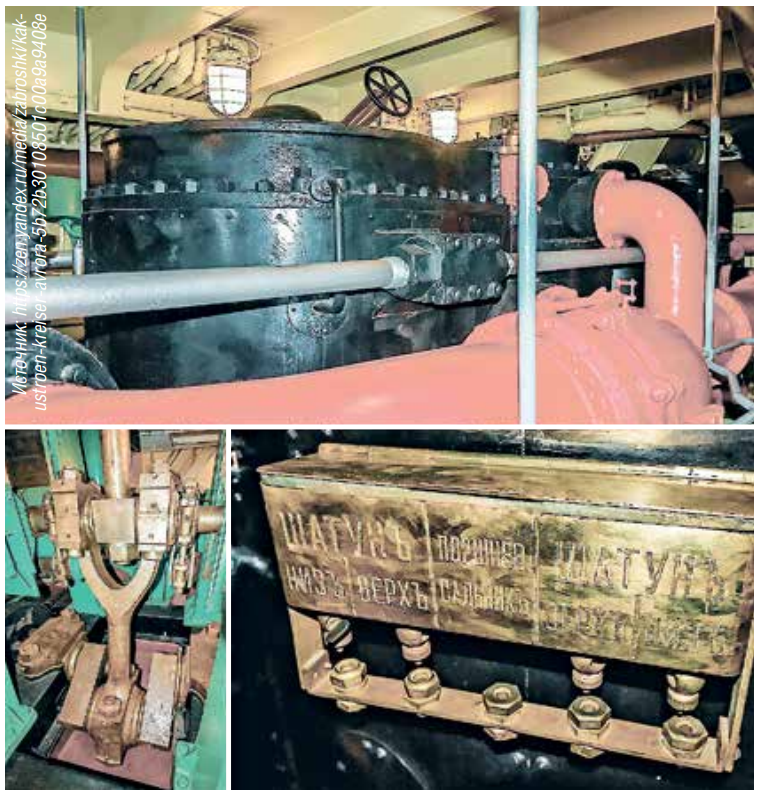
Сформированная многоуровневая система осмотров используется и сейчас. Основные виды осмотров и примерная периодичность: ежесменный осмотр проводится вахтенным; ежесуточный осмотр проводится машинистом; еженедельный осмотр проводится механиком; ежемесячный осмотр проводится старшим помощником.
К этому добавляется система сдачи-приемки вахты с последующим устранением замеченных неисправностей, строгое соблюдение режима смазки и др.
Периодичность ремонтов определяется условиями морской жизни:
- авральный ремонт проводится немедленно, силами машинной команды;
- текущий ремонт проводится в порту с привлечением необходимых специалистов;
- капитальный ремонт проводится в доке специалистами морского завода.
ТОиР на железной дороге
Безопасность передвижения на железной дороге обеспечивалась комплексом мероприятий по ТОиР пути, паровозов, вагонов и др. Однотипность паровозного оборудования (рис. 5, 6), условий эксплуатации позволяли использовать преимущества планово-предупредительных ремонтов (ППР): регламентированные сроки и объемы подготовленный инструмент и обученный персонал.
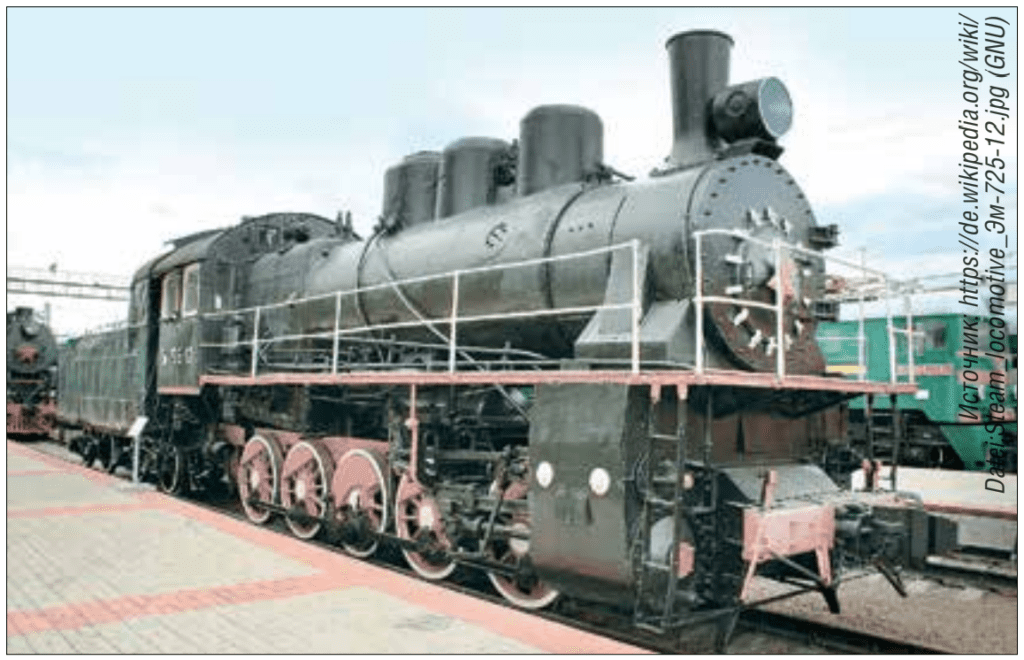
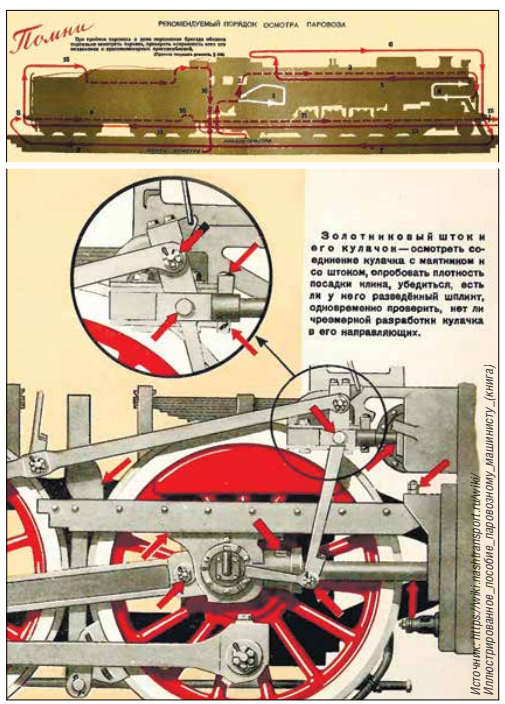
Для обеспечения технически исправного состояния паровозов правилами предусматривались профилактический осмотр, промывочный (текущий), подъемочный, заводской и случайный ремонты, которые проводили после выполнения установленных норм пробега между видами ремонта и осмотра с учетом технического состояния железнодорожного транспорта.
Основным видом технического обслуживания являлся профилактический осмотр, проводимый машинистами паровозной бригады, специалистами в депо. При осмотре проверяли характер износа, техническое состояние узлов и деталей, соответствие их установленным размерам, исправность действия тормозных устройств, контрольных и измерительных приборов. Осмотр паровозов осуществлялся в стойле основного депо силами специализированных бригад с привлечением, в необходимых случаях, слесарей комплексных бригад промывочного ремонта.
При нахождении паровоза в профилактическом осмотре свыше установленной нормы простоя его переводили в промывочный ремонт – для очистки стенок котла от накипи, удаления шлама и устранения отдельных неисправностей узлов и деталей. На каждой дороге нормы пробега между промывочными ремонтами устанавливал начальник дороги по сериям паровозов для каждого локомотивного депо. Время работы паровоза между промывочными ремонтами не должно было превышать 40 суток. Действия в данном виде ремонта по большей части сводились к ручной работе на верстаках и лишь в малой степени нуждались в услугах станков. Промывочный ремонт паровоза выполняли слесари комплексной и специализированных бригад в установленные нормы простоя по графику.
Подъемочный ремонт проводили при достижении предельного износа бандажей движущих колесных пар. Этот ремонт имел целью устранить ослабления в соединениях частей паровоза и, восстановив утраченный запас на износ его частей, привести паровоз в состояние, обеспечивающее осуществление пробега номинальной длительности. Качество ремонта определяли пробной поездкой с устранением после этого всех обнаруженных недостатков.
Заводской ремонт паровоза выполняли на профильном предприятии. Туда направляли паровозы после выполнения установленного межремонтного пробега с учетом его технического состояния. Капитальный ремонт – это разборка паровоза или тендера по частям в главных мастерских. Отдельные части паровоза распределяли по цехам и ремонтировали при необходимости, восстанавливали способами, обеспечивающими их исправность и начало нового цикла ресурса. Для повышения качества производимых работ при ремонте паровозов применяли методы сетевого планирования и управления, поточные линии ремонта узлов и деталей и др.
Случайный ремонт приравнивался по своему содержанию к аварийному.
В России с момента появления железных дорог существование паровозов было неотрывно связано с их машинистами. За каждым паровозом закреплялись постоянные бригады, которые работали на нем многие годы, досконально знали все его особенности и сами проводили текущий ремонт. Машинисты воспринимали себя хозяевами машины, что обеспечивало сохранность техники. Попытка перейти на обезличенную эксплуатацию привела к увеличению количества неисправных паровозов. Паровоз без человека – ничто. Каждый паровоз обязательно чем-то отличался от других. Любой работник безошибочно узнавал свой паровоз по звуку его гудка.
Поразительное долголетие отечественных паровозов было обеспечено не только надежностью конструкции, но и этим особым отношением к паровозу, которое невозможно регламентировать никакими инструкциями. Каждый машинист тщательно изучал особенности движения на своем участке пути. Это позволило, например, Петру Федоровичу Кривоносу водить тяжеловесные поезда с вдвое повышенной против существовавших норм скоростью.
Таким образом, сформировались два подхода к ТОиР оборудования:
- послеосмотровые ремонты или ремонты по состоянию, применимые для уникального механического оборудования с большими коэффициентами запаса прочности и переменными режимами работы;
- принудительные ремонты с предупредительной заменой деталей и узлов через определенные интервалы времени или после наработки определенного ресурса, применяемые для типовых механизмов, работающих в одинаковых условиях.
ТОиР на металлургических заводах
До середины XIX века производство чугуна и стали носило более ремесленный, чем производственный характер. Все изменилось после изобретения Генри Бессемером в 1855 году (рис. 7, 8) и усовершенствования в 1879 году Сид ни Гилкристом Томасом конверторного способа получения стали. Отметим, что томасовский конвертер работал в литейном цехе Донецкого металлургического завода до 2012 года.
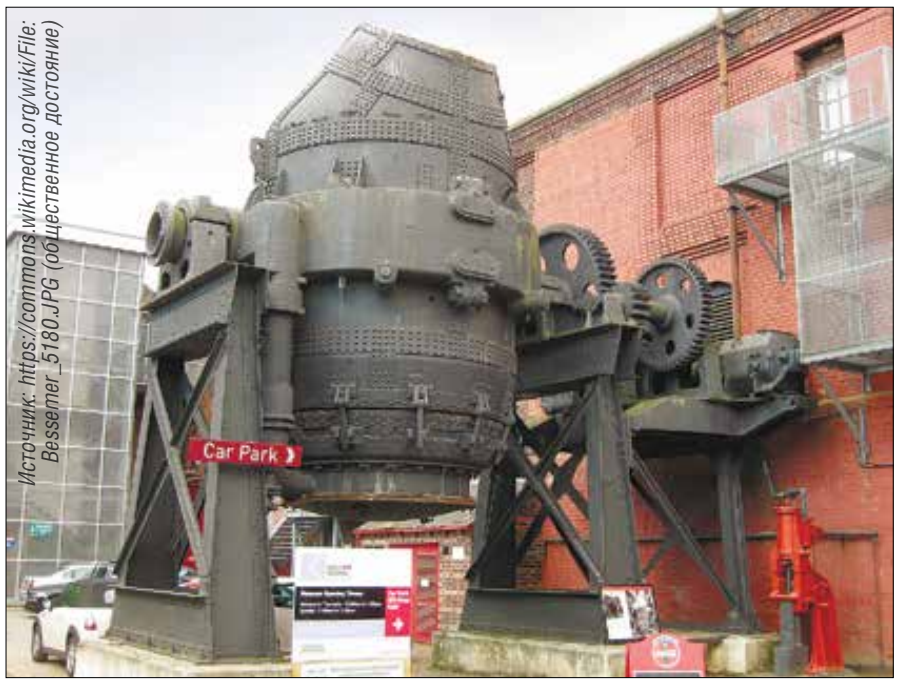
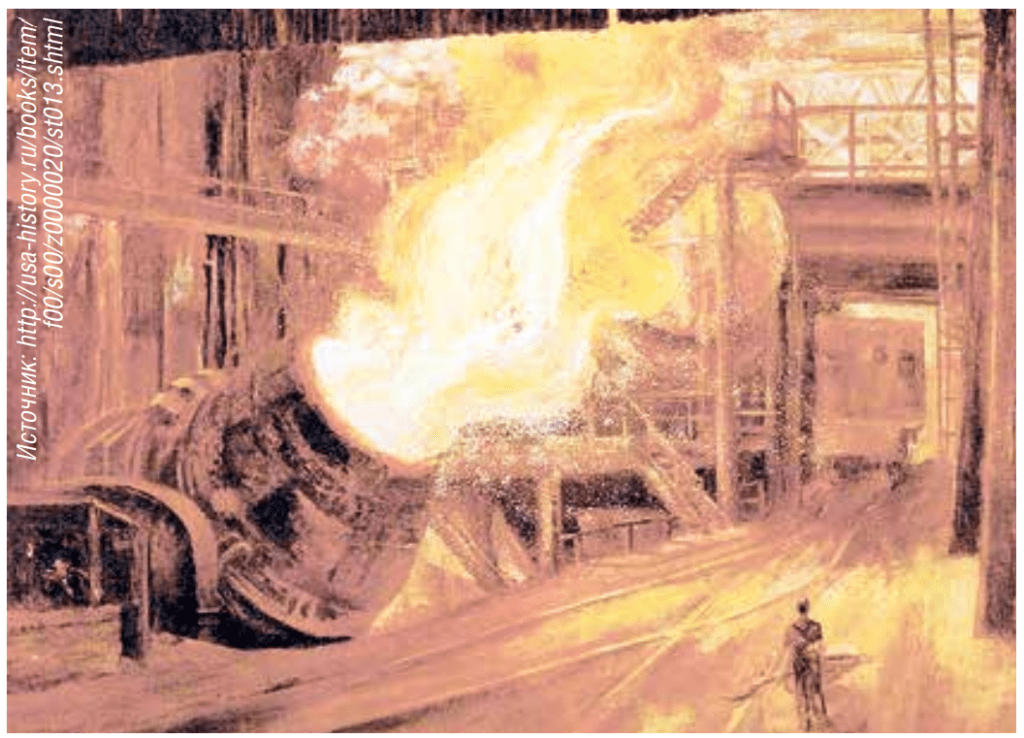
В 1865 году Пьер-Эмиль Мартен успешно осуществил выплавку стали из чугуна и железного лома в регенеративных пламенных печах. Принцип использования тепла отходящих газов для подогрева топлива и воздуха в регенераторах был разработан Карлом Вильгельмом Сименсом, поэтому в ряде стран этот процесс выплавки стали называть сименс-мартеновским.
Благодаря промышленной революции и появлению электрического привода в начале XX века произошло перевооружение металлургических заводов России. Появились механизированные системы загрузки доменных печей, прокатные станы с мощными двигателями. Для оборудования этого периода характерны большие коэффициенты запаса прочности, поэтому прокатные станы 1908 года работали до 2008 года, а однодвигательная скиповая лебедка фирмы «Отис» работала и в 2002 году.
Оборудование было, в основном, импортное, методы ремонта – неизвестными, запасные детали практически отсутствовали, что чем-то напоминает нынешнюю ситуацию, сложившуюся на отечественных предприятиях в связи с санкционными ограничениями.
К металлургическому оборудованию были применены принципы обслуживания уникального оборудования, с преобладанием осмотров и технического обслуживания. На фотографии (рис. 9б) начала ХХ века – обслуживающий персонал на фоне блока барабанов скиповой лебедки доменной печи. Минимум три человека были задействованы в обслуживании скиповой лебедки. Так продолжалось до окончания гражданской войны.
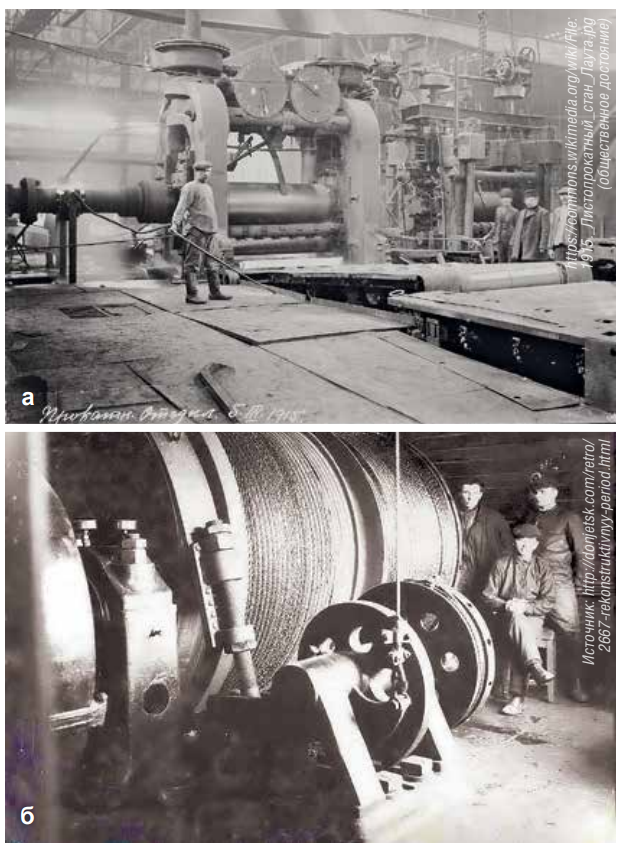
Зарождение системы ППР
В первые годы советской власти началась работа по организации ППР и рационализации ТОиР оборудования на металлургических заводах. Так, в 1923 году Окружное бюро научной организации труда Приокского горного округа под руководством инженера А.Г. Попова выполнило сравнение ремонта машин после отказа и в плановом порядке. Эта работа проводилась на Выксунском и Кулебакском металлургических заводах. Ее результаты были опубликованы в 1927 году в виде инструкции по планированию текущего ремонта. На основе материалов этой работы в 1931 году была выпущена брошюра «Рационализация ремонтного дела на заводе». Здесь давался достаточно подробный анализ недостатков ТОиР оборудования, устанавливались принципы их рациональной организации и намечались мероприятия, которые требовалось провести в области ремонтного дела.
В качестве основных принципов указывались следующие:
- ремонт должен непрерывно поддерживать оборудование в обновленном состоянии;
- ремонт оборудования на предприятиях есть самостоятельное производство, продающее свою продукцию цехам, потребляющим ремонт;
- всю постановку ремонтного дела необходимо привести к методам предупредительного и принудительного ведения ремонта;
- ввести в ремонтное производство систему планирования.
Новые вызовы и угрозы
ЦК ВКП(б) 1 июня 1927 года выпустил обращение «Ко всем организациям ВКП(б). Ко всем рабочим и крестьянам», в котором сообщил об угрозе империалистического вторжения. Причиной стал англо-советский конфликт 1927 года, угрожавший полномасштабной войной. Однако преимущественно аграрная на тот момент страна не могла воевать даже с Польшей. Необходимым стало укрепление обороноспособности государства за счет индустриализации. Началось строительство предприятий, выпускающих тяжелые машины, новых металлургических заводов и подготовка специалистов для обслуживания этих уникальных агрегатов.
Одним из ярких подвигов стало изготовление Ижорским заводом в 1931 году первого советского блюминга (рис. 10), в 1933 году введенного в эксплуатацию на Макеевском металлургическом заводе. Следует отметить, что тогда во всем мире было только 12 блюмингов, которые выпускали только заводы Германии и США. Согласно легенде, после монтажа первого советского блюминга для его обслуживания на Макеевский металлургический завод была направлена команда моряков, демобилизованных с кораблей Балтийского флота. Опыт эксплуатации корабельного оборудования был применен для обслуживания уникальных, тяжелых энергоемких металлургических машин.
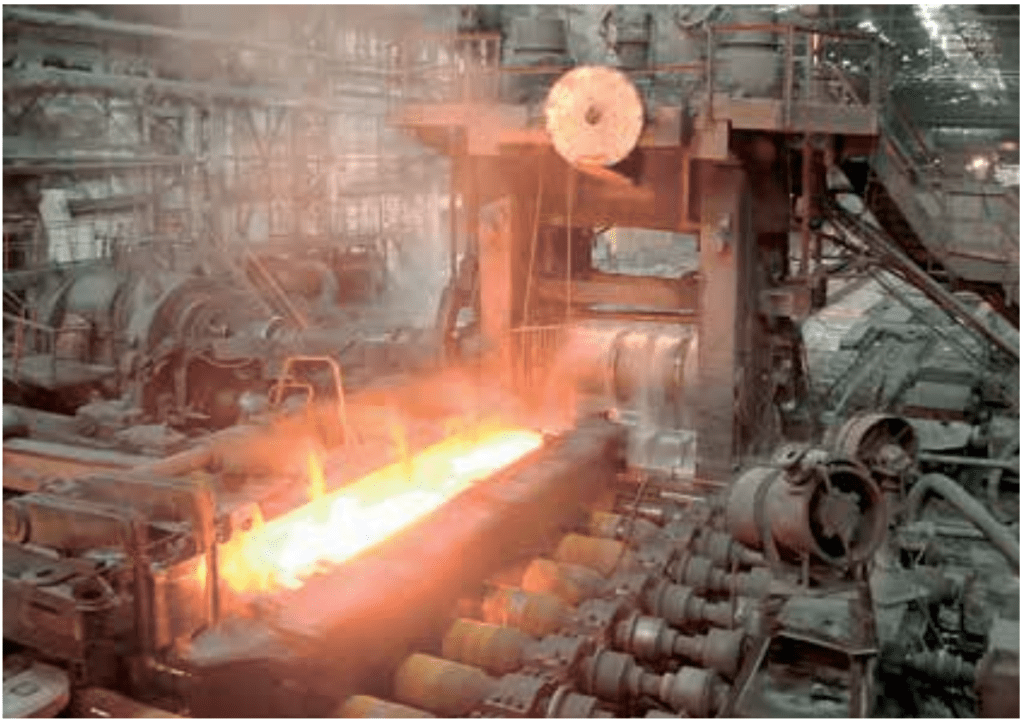
Малое количество металлургических машин, отсутствие ремонтной базы, подготовленного персонала и опыта эксплуатации потребовали использовать осмотровую систему. Главная задача – остановить эксплуатируемую машину при первых признаках неисправности и не допустить вторичных повреждений из-за разрушения смежных элементов оборудования.
Техническое состояние механизмов оценивалось при помощи органолептических методов: анализа шумов механизмов, тактильного восприятия вибрации и определения степени нагрева, методов визуализации механических колебаний. Реализация методов осуществлялась при визуальном осмотре работающего или остановленного механизма. Частичная разборка оборудования для проведения ревизии проводилась редко, а полная разборка – только во время капитального ремонта. В дальнейшем ревизии металлургических машин стали совмещать с проведением текущих и капитальных ремонтов.
Рационализация
В 1931 году вышла брошюра В.В. Спиридонова «Рационализация ремонта заводского оборудования», опиравшаяся на результаты, полученные А.Г. Поповым, и развивавшая его подход. В 1932 году была опубликована еще одна брошюра В.В. Спиридонова, в заглавии которого впервые фигурирует понятие ППР (рис. 11). В работах А.Г. Попова и В.В. Спиридонова упорядочивание текущего ремонта предполагалось достичь «приведением его к системе планирования при посредстве запасных частей». Основной упор делался на определении срока службы изнашивающихся деталей оборудования и на своевременном изготовлении запасных частей.
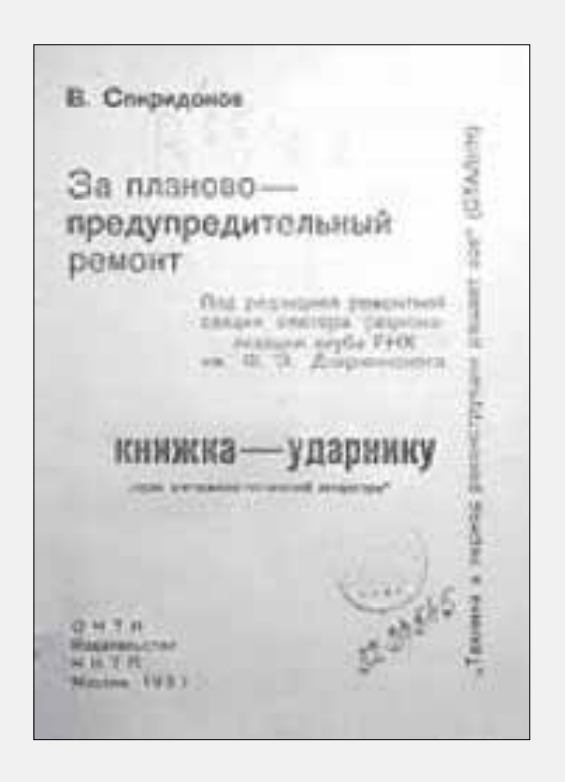
В работе В.В. Спиридонова указывалось: «Планирование и четкий выпуск продукции может иметь место лишь при оборудовании, которое работает так же точно, уверенно и без перебоев, как хорошие часы. Между тем на наших заводах большой процент механизмов имеет весьма почтенный возраст, а систематизированного, организованного ухода за ними нет. Новое импортное оборудование без надлежащего ухода также быстро начинает работать с перебоями.
Происходит это потому, что текущий ремонт не налажен, и из-за неимения под руками запасной части происходят простои, а отсюда и срыв программы. В капитальный ремонт механизм поступает лишь тогда, когда все его части окончательно разболтаны…
На большинстве наших заводов установилось мнение, что «оборудование нашего завода давно пора под копер; тут не только профилактика, а и омоложение не поможет, а отсюда вывод – нужно новое оборудование».
Это, конечно, простое решение вопроса, но оно далеко от наших возможностей, ибо целиком рассчитывать на получение импортного оборудования мы не можем и не должны».
Остается поражаться, насколько слова, сказанные 90 лет назад, во многом актуальны и для современной действительности.
Развитие идей ППР
Идеи планирования организации ремонтов оказались плодотворными. В это же время появляются первые публикации, в которых предлагается основывать ремонтную стратегию на проведении периодических осмотров. Путем периодических осмотров оборудования определялось его состояние, на основе этого намечались срок и объем ремонта. Такая стратегия системы послеосмотровых ремонтов в 1933-1938 годах получила в нашей стране широкое распространение. Недостаток системы послеосмотровых ремонтов – отсутствие нормативов на ремонт и невозможность планирования ресурсов на длительный период.
В 1934 году Ю.С. Борисов и Г.П. Жуков разработали систему ППР, в которой:
- Плановые ремонты каждого объекта проводятся периодически, через определенное количество отработанных часов. Последовательные различные виды ремонтов одного объекта образуют периодически повторяющийся ремонтный цикл.
- Планирование ресурсов, необходимых для ремонта, основано на «нормальном объеме ремонтных работ», который, в свою очередь, определяется ремонтной сложностью объектов, разбитых на группы. Каждая из групп объединяет оборудование, имеющее примерно одинаковую рудоемкость ремонта и обслуживания.
- Между периодическими плановыми ремонтами каждый агрегат подвергается плановым проверкам (или осмотрам). В процессе проверок устраняются мелкие дефекты, производится регулировка и чистка, а также определяется номенклатура деталей, которые должны быть подготовлены для замены при очередном плановом ремонте.
Организация ОГМ
В основе социалистического хозяйствования лежит четкое планирование, но в годы индустриализации о выполнении принципа «точно вовремя» не могло быть и речи, а ремонты металлургических машин часто приходилось выполнять вне плановых сроков. Для того, чтобы из-за непоставленной детали, узла не останавливался металлургический завод, были организованы отделы главного механика – машиностроительные подразделения, включающие литейные, кузнечные, механические, ремонтные и другие цеха. Это позволило обеспечить выполнение принципов проведения ТОиР металлургического оборудования, которые отличаются комплексностью, большими объемами и сжатыми сроками, что требует решения вопросов подготовки, планирования, скоростного и качественного проведения работ.
В 1937 году в эти отделы стали приходить первые инженеры-механики. Начало работы главных механиков, имевших большой практический опыт и три класса образования, с молодыми инженерами-механиками с высшим образованием было непростым. По воспоминаниям одного из них, некоторые вопросы главного механика часто ставили в тупик – какая нарезана резьба, какой диаметр каната и др. Однако, когда из Москвы пришел запрос рассчитать коэффициенты динамичности прокатных клетей, все стало на свои места. Эта задача, непростая даже по сегодняшним меркам, была успешно решена молодым инженером-механиком. Правда, глядя на документ с формулами и расчетами, главный механик сказал: «Это все для замутнения пролетарского самосознания». Тем не менее, документ подписал. Далее работать стало значительно легче. Надо было осваивать непростые ремонты импортной техники, обеспечивать работу оборудования во время Великой Отечественной войны, восстанавливать металлургические заводы. Так, например, известным фактом является предложение заместителя главного механика Магнитогорского металлургического комбината Н.А. Рыженко впервые в мировой практике катать броневой лист на блюминге.
Статистический рай
Использование одинаковых технологий и оборудования, увеличение количества металлургических предприятий, а, следовательно, и парка металлургических машин в 50-60-х годах потребовали повышения безотказности работы механического оборудования. Проведенные исследования долговечности деталей металлургических машин позволили получить статистические данные и выдать рекомендации по времени принудительных замен.
Разработка и внедрение основных положений о ППР механического оборудования предприятий черной металлургии позволили сформировать полноценную систему ТОиР оборудования. Были решены вопросы ее содержания; периодичности, продолжительности и трудоемкости работ; их организации, планирования и выполнения; отчетности; обеспечения запасными частями и др. Систематизированы термины, определены формы технической документации, содержание типовых и специфических работ, выполняемых при плановых ремонтах металлургического оборудования. Накопленный опыт обобщался в правилах технической эксплуатации механического оборудования по переделам металлургического производства и отдельным агрегатам (рис. 12).
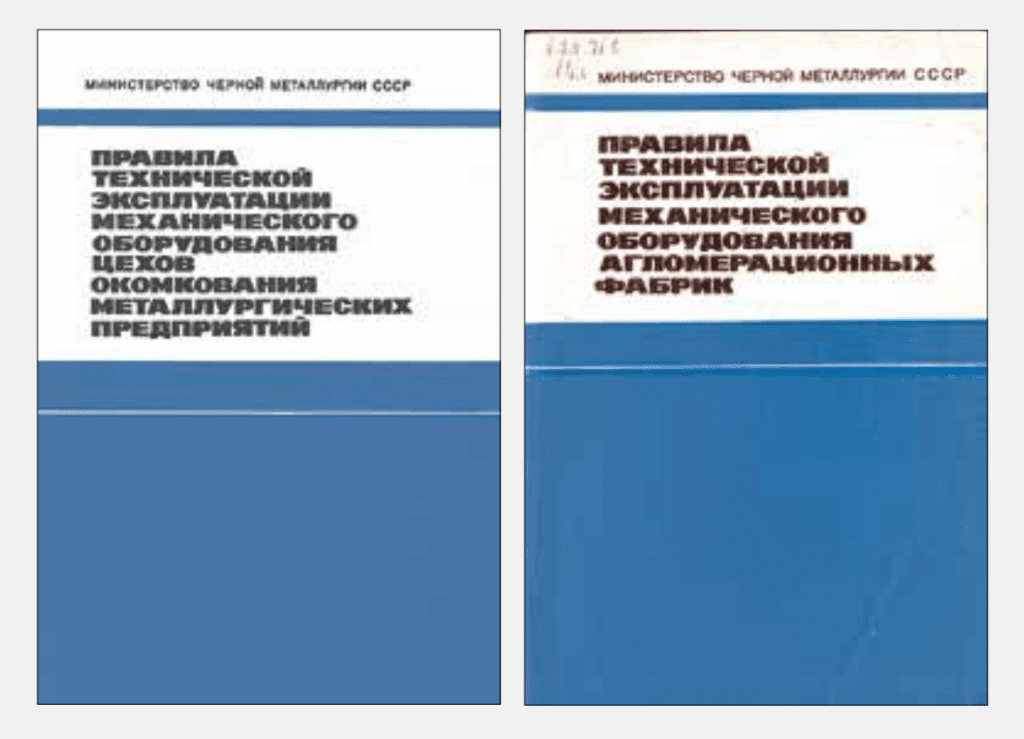
ТОиР по техническому состоянию
Однако отказы, как нарушения работоспособного состояния механизмов, все равно происходили. Поэтому в 70-80-х годах ХХ века были начаты работы по повышению надежности работы металлургических машин, в частности, на основе учета и анализа отказов. Использовались методы статистического и вероятностного анализа событий. Системный подход, использование данных, полученных ремонтными службами, позволили повысить безотказность работы металлургических машин.
Тем не менее проведенные исследования указывали на значительный разброс ресурса однотипных деталей из-за различий в качестве изготовления и эксплуатации. Установить срок службы элементов оборудования индивидуального и мелкосерийного изготовления, работающего в условиях нестабильных нагрузок, оказалось невозможно. Поэтому, в рамках системы ППР, была предусмотрена возможность корректировки сроков замен путем проведения ревизий – осмотров деталей и узлов при неполной разборке механизма, проводимых во время текущих ремонтов.
Одновременно были начаты работы по диагностированию состояния металлургических машин и переходу на ремонты по техническому состоянию. Организационно предполагалось формирование отделов или бюро диагностирования в структуре ремонтных служб предприятия. Основной метод контроля – измерение параметров вибрации и сравнение с нормативными значениями.
В 90-х годах переход на ТОиР по состоянию на отечественном пространстве во многом стал вынужденной мерой. Тогда же было отмечено, что снижение объема производства не приводит к пропорциональному снижению объема ремонтных работ. Неработающее оборудование также изнашивается.
В начале 2000-х годов были сформулированы общие принципы технического диагностирования механического оборудования металлургических предприятий:
- проведение диагностирования и документирование изменений технического состояния, а также определение причин, которые их вызвали;
- проведение диагностирования технического состояния методами неразрушающего контроля, преимущественно без разборки и остановки оборудования;
- определение объемов работ по ТОиР на основе результатов диагностического контроля.
Информационное обеспечение ТОиР
Недостаток информации о техническом состоянии является основной причиной отказов и аварий. Особенностью механического оборудования металлургических предприятий является большое количество разнотипных машин и механизмов, среди которых чрезвычайно затруднительно выделить основные и вспомогательные. Так, например, разрушение соединительной шпонки на механизме подъема литейного крана может стать причиной остановки сталеплавильного производства на 3-4 часа и более.
Предотвращение таких внезапных отказов может быть осуществлено путем раннего упреждения на основе диагностирования по комплексу параметров и визуального подтверждения наличия повреждений. Техническое диагностирование следует рассматривать как метод борьбы с энтропией, реализуемый путем введения информации о техническом состоянии в систему, на основании чего осуществляется своевременное проведение обоснованных работ по ТОиР. На многих металлургических предприятиях были сформированы отделы технического диагностирования, оснащенные современными приборами, появились стационарные системы контроля технического состояния. Наряду с данными о событиях, фиксируемых в агрегатных журналах, ремонтными ведомостями и ведомостями дефектов, заявками, актами расследования аварий, это породило громадный объем данных, нуждающихся в обработке для принятия решений.
Эту информацию необходимо собрать и использовать для получения ожидаемого эффекта. Эффективность диагностирования определяется своевременным пользованием полученной информации о техническом состоянии в применении к возможностям проведения ТОиР ремонтной службой предприятия. Анализ комплекса данных о техническом состоянии, формирование оптимальных информационных потоков, учитывающих специфику конкретного предприятия, позволяет вывести систему обслуживания оборудования на принципиально новый уровень, что открывает новую страницу в истории ТОиР.
Современное состояние
В настоящее время на отечественных металлургических предприятиях преимущественно используются первые два уровня диагностических систем:
- отображение состояния – обнаружение отклонений в работе механизмов по признакам, которые определяются органами чувств человека;
- контроль и защита – измерение контролируемых параметров, сравнение их с заданными (нормативными) величинами и защитное отключение оборудования при достижении критической величины.
Кроме того, на основании полученных данных определяются сроки и объемы ТОиР, для проведения которых оборудование останавливают.
Становится очевидной необходимость перехода на следующий уровень – проактивного управления техническим состоянием оборудования по фактическим значениям контролируемых параметров, в том числе технологического процесса, во времени. На основании этого могут быть решены задачи прогнозирования и оптимизации ТОиР, в чем важную роль играют современные тенденции автоматизации и цифровизации.
А что завтра
Завтрашний день в сфере развития ТОиР готовит нам возможность получения комплексных данных на основании применения средств автоматизации и цифровизации, в том числе искусственного интеллекта. Это позволит не только учитывать и анализировать в режиме онлайн сведения о техническом состоянии оборудования, но и формировать оптимальную программу ТОиР, на что направлены усилия специалистов уже в настоящее время.
Кроме того, в перспективных исследованиях, которыми занимаются, в том числе, ученые Донбасса, речь идет о создании саморегулируемых и самовосстанавливающихся систем, что требует кардинального пересмотра подходов к проектированию оборудования. Указанные исследования
особенно актуальны в условиях геополитического противостояния и необходимости формирования экономического превосходства отечественного производства с целью обеспечения перелома в связи с высокой степенью неоднородности уровня развития предприятий Российской Федерации, а также широким заимствованием зарубежных технологий и методов организации ТОиР как передовых.
История подтверждает, что мы не только способны, но и сделаем тот прорыв, который выведет развитие системы ТОиР на отечественных предприятиях на качественно новый уровень.
Список литературы
- Магола Е. Тайны сокровищ Эрмитажа. История золотого павлина [Электронный ресурс] // Петербург Центр. – URL: https://peterburg.center/ln/tayny-sokrovishch-ermitazha-istoriya-zolotogo-pavlina.html (дата обращения: 28.05.2022).
- Пятницкий Ю. «Золотой павлин» Екатерины Великой // Наше наследие. – 2016. – № 117.
- Иллюстрированное пособие паровозному машинисту. – М.: Государственное транспортное железнодорожное издательство, 1953.
- Кац Б.А. Из истории создания системы планово-предупредительного ремонта [Электронный ресурс] // Ассоциация эффективного управления производственными активами (Ассоциация ЕАМ). URL: http://eam.su/iz-istoriisozdaniya-sistemy-planovo-predupreditelnogo-remonta.html (дата обращения: 28.05.2022).
- Попов А.Г. Учет и возобновление запасных частей заводского оборудования через ремонтно-механические мастерские // Система и организация. – №8-9. – С. 5-15.
- Попов А.Г. Рационализация ремонтного дела на заводе. – М., Л.: Гос. науч.-техн. изд-во, 1931. – 79 с.
- Спиридонов В.В. Рационализация ремонта заводского оборудования / Практическое руководство под ред. Б.О. Кагана. – Вып. 1. – Л., М.: Техника управления, 1931. – 70 с.
- Спиридонов В.В. За планово-предупредительный ремонт (Книжка – ударнику. Серия агитационно-технической литературы) / Под ред. Ремонтной секции Сектора рационализации клуба РНХ им. Ф.Э. Дзержинского. – М.: НКТП, 1932. – 51 с.
- Спиридонов В.В. Система планово-предупредительных ремонтов. – М., Л.: Стандартизация и рационализация, 1934. – 86 с.
- Борисов Ю.С., Жуков Г.П. Методика планирования ремонтов заводского оборудования способом приведения к условным единицам ремонтосложности // Организация производства. – 1934. – №9. – C. 16-21.
- Борисов Ю.С., Жуков Г.П. Система периодических ремонтов оборудования машиностроительных предприятий. – М., Л.: Оборонгиз, 1939. – 242 с.
- Тимофеева Л.К. Планово-профилактический ремонт в металлургии и машиностроении. – М.: Гос. науч. б-ка, 1939. – 28 с.
- Борисов Ю.С. Планово-предупредительный ремонт оборудования в промышленности СССР. – М.: Машгиз, 1949. – 84 с.
- Единая система планово-предупредительного ремонта и рациональной эксплуатации технологического оборудования машиностроительных предприятий / Под ред. проф. М.О. Якобсона. – 6-е изд. – М.: Машиностроение, – 591 с.
- Ящура А.И. Система технического обслуживания и ремонта энергетического оборудования. справочник. – М.: НЦ ЭНАС, 2005. – 502 с.
- Правила технической эксплуатации механического оборудования доменных цехов / М-во черной металлургии СССР. Всесоюз. науч.-исслед. ин-т организации производства и труда черной металлургии «ВНИИОЧермет». – М.: Металлургия, 1969. – 210 с.
- Правила технической эксплуатации механического оборудования мартеновских цехов / ВНИИМЕХЧЕРМЕТ. – М.: Металлургия, 1979. – 202 с.
- Правила технической эксплуатации механического оборудования блюмингов и непрерывно-заготовочных станов / М-во чер. металлургии СССР – М.: Металлургия, 1979. – 191 с.
- Правила технической эксплуатации механического оборудования
агломерационных фабрик / Утв. Черметремонтом М-ва чер. металлургии СССР 10.08.84. – М.: Металлургия, 1985. – 144 с. - Правила технической эксплуатации механического оборудования кислородно-конвертерных цехов металлургических заводов / М-во черной металлургии СССР. Всесоюз. науч.-исслед. ин-т организации производства и труда черной металлургии «ВНИИОЧермет». – М.: Металлургия, 1970. – 204 с.
- Временное положение о техническом обслуживании и ремонтах (ТОиР) механического оборудования предприятий системы министерства черной металлургии СССР. – Тула, 1983. – 390 с.
- Гребеник В.М., Цапко В.К. Надежность металлургического оборудования (оценка эксплуатационной надёжности и долговечности): справочник. – М.: Металлургия, 1989. – 590 с.
- Организация технического обслуживания металлургического оборудования / В.Я. Седуш, Г.В. Сопилкин, В.З. Вдовин и др. – К.: Техника, 1986. – 123 с.
- Гребеник В.М., Гордиенко А.В., Цапко В.К. Повышение надежности металлургического оборудования: Справочник. – М.: Металлургия, 1988. – 687 с.
- Кац Б.А. Зачем ремонтнику компьютер? // РИТМ (Ремонт. Инновации. Технологии. Модернизация). – 2012. – №5. – С. 14-16.
- Данилов О., Скворцов Д., Свистула О. Автоматизация ТОиР. Хроника внедрений [Электронный ресурс] // и-Маш: Ресурс Машиностроения. URL: http://www.imash.ru/materials/automation/35654-avtomatizacija-toir-khronikavnedrenij.html (дата обращения: 28.05.2022).
- Проников А.С. Параметрическая надежность машин – М: Изд-во МГТУ им. Н.Э. Баумана, 2002. – 559 с.
- Нищета В.В. Системы автоматизированного управления – классификация и применение // Вибрация машин: измерение, снижение, защита. –– № 4. – С. 36–41
Журнал Prostoev.NET № 1(30) 2022
В.А. СИДОРОВ, Донецкий национальный технический университет
А.В. СИДОРОВ, Ассоциация эффективного управления производственными активами (Ассоциация ЕАМ)