Рассмотрены вопросы ремонтосложности и диагностики состояния станочного оборудования.
Мне в свое время довелось редактировать справочник. Это типовая система технического обслуживания и ремонта металло- и деревообрабатывающего оборудования. Здесь есть вся информация по сложности ремонта станков, которые выпускали в Советском Союзе. Есть вся информация о квалификации работ, о стоимости работ, о нормах и т.д. До сих пор этот справочник не потерял актуальности. Многие станки, которые имеются в этом справочнике, до сих пор эксплуатируются на предприятиях, но появились и новые станки. В этом справочнике все приведено к категории сложности ремонта станочного оборудования. Она определяется:
- конструктивными особенностями станков — это компоновка, кинематическая схема;
- технологическими особенностями — точностные параметры, ремонтопригодность и т.д.
Типовая система технического обслуживания и ремонта металло- и деревообрабатывающего оборудования ОПРЕДЕЛЯЕТ:
- состав обязательных регламентируемых операций обслуживания;
- периодичность их выполнения по отработанному оперативному времени;
- распределение обязанностей между исполнителями;
- трудоемкость и стоимость каждой регламентированной операции;
- трудоемкость и стоимость непланового обслуживания;
- организацию выполнения обслуживания и контроля его качества;
- технологическую и материальную подготовку;
- подготовку кадров, тарификацию работ и формы оплаты труда рабочих;
- организацию планирования, учета выполнения и анализа результатов технического обслуживания;
- организацию надзора за соблюдением правил технической эксплуатации станков и машин.
Вот как рассчитать ремонтосложность новых станков, как оценить ремонтосложность и состояние станков ЧПУ? Что такое категория сложности ремонта?
Трудоемкость и степень сложности ремонта станков оценивается категорией сложности ремонта. Чем сложнее станок, тем выше категория сложности ремонта. За эталон принят токарно-винторезный станок, наиболее распространенный станок 16А20 с высотой центров 200 мм и расстоянием 1000 мм, ему присвоена 11 категория сложности.
Номер категории сложности ремонта равен числу единиц ремонтной сложности, которые характеризуют объем работ при капитальном ремонте. Одна единица ремонтной сложности для механической части станков составляет 35 часов, из которых 23 часа выделяется на слесарные работы, 10 часов — станочные работы и 2 часа — прочие (сварочные, малярные и т.п.). Единица ремонтной сложности электротехнического оборудования станков составляет 15 часов (11 часов — электрослесарные работы, 2 часа — станочные, 2 часа — прочие). Нормы часов все привязаны к ремонтоспособности. Все другие станки, расписанные в этом справочнике, имеют такую же привязку. Если новые станки не попали в этот справочник, то рассчитать ремонтосложность можно по эмпирическим формулам.
Определение ремонтосложности токарных станков
RM = KKO (K1dO + K2LМЦ + K3n1) + ROM + RГ , где
KKO — коэффициент конструктивных особенностей станка: KKO = KT KXB KЧТ;
KT — коэффициент класса точности;
KXB — коэффициент исполнения (1,0 — с ходовым винтом; 0,9 — без х.в.);
KЧТ — коэффициент частоты вращения шпинделя ( KЧТ = 1,0 при частоте вращения <2000 об/мин, KЧТ = 1,1 при >2000 об/мин; );
LМЦ — расстояние между центрами, мм;
n1 — число ступеней скорости шпинделя;
ROM — ремонтосложность отдельных механизмов; ROM = RСТ + RБТ + RСД;
RСТ — ремонтосложность суппортов;
RБТ — ремонтосложность механизма бесступенчатого регулирования частоты вращения шпинделя;
RБТ = 2, при dO ≤ 400 мм; RБТ = 4, при dO > 400 мм;
RСД — ремонтосложность механизмов, не входящих в основной комплект станка;
RГ — ремонтосложность гидравлического оборудования.
Определение ремонтосложности вертикально- и горизонтально-фрезерных станков
RM = KKO (K1BСФ + K2n3) + ROM + RГ , где
KKO — коэффициент конструктивных особенностей станка: KKO = KT KИФ KЧФ;
KИФ — коэффициент исполнения:
KИФ = 1,0 для вертикальных и горизонтальных,
KИФ = 1,2 для универсальных и вертикальных с поворотной головкой,
KИФ = 1,25 для широкоуниверсальных и бесконсольных;
KЧФ — коэффициент частоты вращения шпинделя:
KЧФ = 1,0 при частоте <2000 об/мин, KЧФ = 1,1 при частоте >2000 об/мин;
BСФ — ширина рабочей поверхности стола, мм;
K1 = 0,03; K2 = 0,125;
n3 — число ступеней скорости шпинделя, получаемых от коробки скоростей,
ROM = RГФ + RБM,
RГФ — ремонтосложность сменных зубчатых колес или сменных шкивов для станков не имеющих коробки скоростей, RГФ = 0,4;
RБM — ремонтосложность механизма бесступенчатого регулирования скорости шпинделя: RБM = 1,8.
Ремонтосложность гидравлической части станочного оборудования
RГ = 0,1Р + 0,015Q + C + 0,003 ∑үQ1 + 0,001L + 0,003D +0,5n + 0,03m, где
Р — рабочее давление трехплунжерного насоса, МПа;
Q — производительность трехплунжерного насоса высокого давления, л/мин;
С — коэффициент, учитывающий конструктивные особенности трехплунжерного насоса: С=4;
ү — коэффициент, учитывающий конструктивные особенности насосов остальных типов (кроме трехплунжерных);
Q1 — производительность насосов остальных типов (кроме трехплунжерных), л/мин;
L — длина цилиндра, мм;
D — диаметр цилиндра, мм;
n — число цилиндров;
m — число клапанов, золотников, дросселей, реле, регуляторов и т.д.
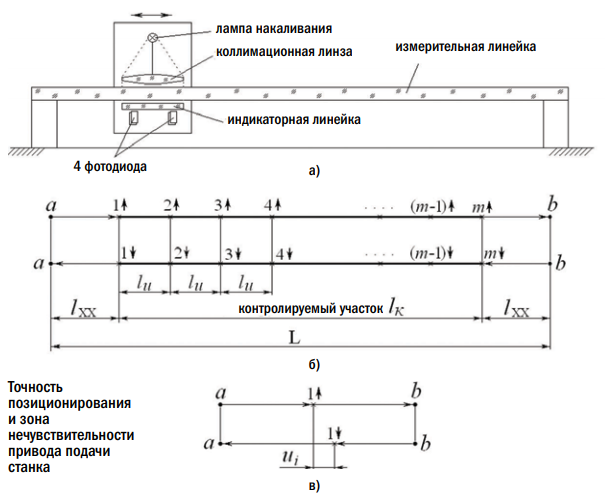
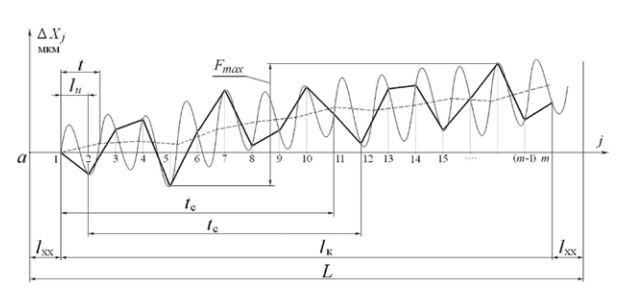
Основные показатели точности позиционирования по ГОСТ 27843-2006 и ISO 230/2:
- Максимальное отклонение от заданного положения при двустороннем подходе Р и одностороннем подходе М.
- Точность повторного подхода Rmax — максимальный размах отклонений от заданного положения при подходе к заданному положению только в одном направлении.
- Максимальная вариация при реверсировании Nmaх — максимальная разность средних величин отклонений от заданного положения при подходе узла станка к заданному положению с противоположных сторон.
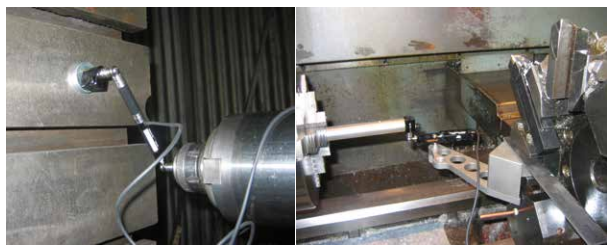
Срок службы станка определяется износом трущихся элементов — это направляющие, подшипники, ходовые винты и т.д. По системе планового предупредительного ремонта станки через определенное время наработки подвергаются ремонту: среднему, капитальному или периодическим осмотрам.
На сегодняшний день экономически целесообразно выводить станки в ремонт по их фактическому состоянию. А фактическое состояние можно определить на основе технической диагностики. Под техническим диагностированием понимают оценку износа поверхностей трения отдельных деталей оборудования и состояния их сопряжений в процессе его эксплуатации без разборки.
Результаты комплексной оценки точности станка мод. FQS 400 без его разборки до регулировки.
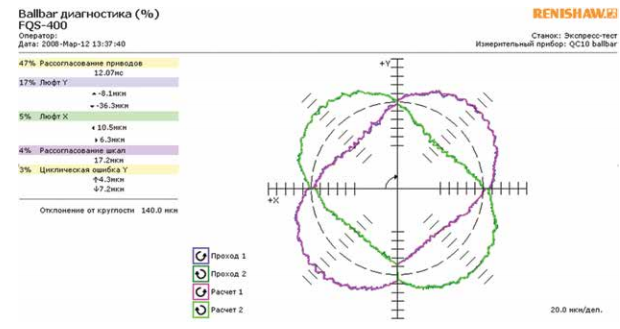
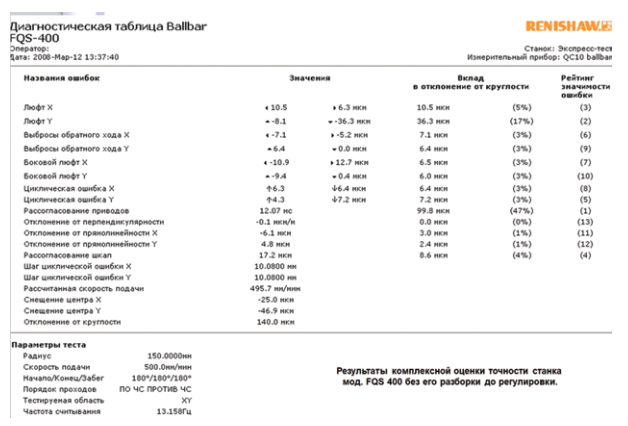
Диагностику износа направляющих можно определить различными методами, например, методом нанесения радиоактивных изотопов, по мере уменьшения излучения устанавливается степень износа направляющих.
Диагностика различных механизмов и узлов, например, приводов подачи, проводится на основе измерения фактического положения узлов при перемещении узла по координатам.
Для одной координаты на подвижном узле ставится внешний измерительный элемент — датчик. Проводится движение по программе, датчиком проводятся измерения фактических положений узла, высчитывается разница между фактическим и запрограммированным. И таким образом можно оценить точность работы станка. По ГОСТу 27843 обозначены показатели, характеризующие точность работы привода станка.
Методика последняя, которая сейчас действует, предусматривает измерения в контрольных точках, которые не коррелируют с основной периодической ошибкой. Фактическая ошибка в приводах носит периодический характер. Есть накопленная составляющая, есть периодическая. Если контрольные точки расположить так, чтобы выбирать разные доли периодических составляющих, можно отдельно оценить и накопленную, и периодическую ошибки.
Эта диагностика по одной координате. Сейчас есть средства, позволяющие отследить состояние оборудования и его приводов по движению по круговой траектории.
Другой метод оценки состояния узлов — с помощью импульсного нагружения. Во всех станках есть движущие станки в виде роторов, это шпиндельные узлы, они всегда на подшипниках.
Программный комплекс nkRecorder (св-во № 2009613214)
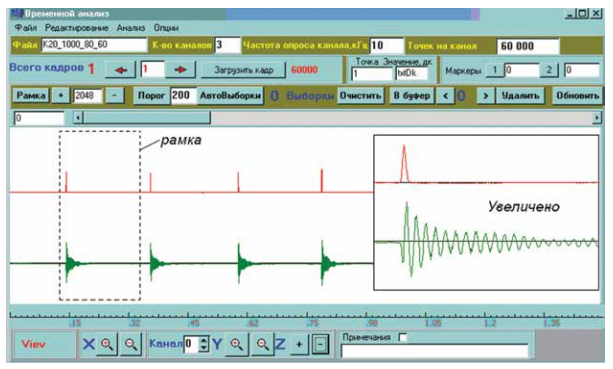
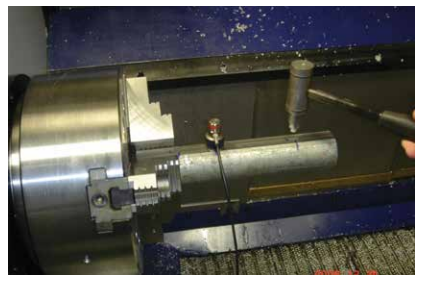
SγP = RγP + i • IγP
Sγγ = R2γ + I2γ
SPP = R2p + I2p
RγP = RP • Rγ + IP • Iγ
IγP = IP • Rγ – Iγ • Rp
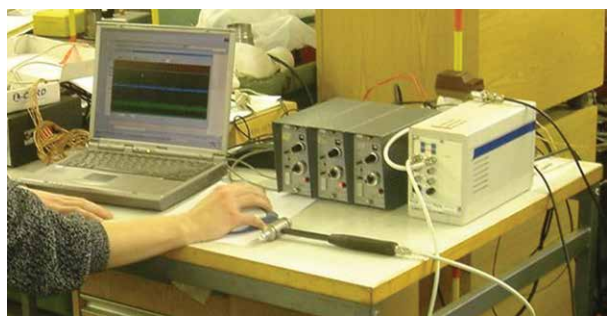
Затем выполняется осреднение спектров по всем выборкам SSРР, SSγγ, RRγР, IIγР
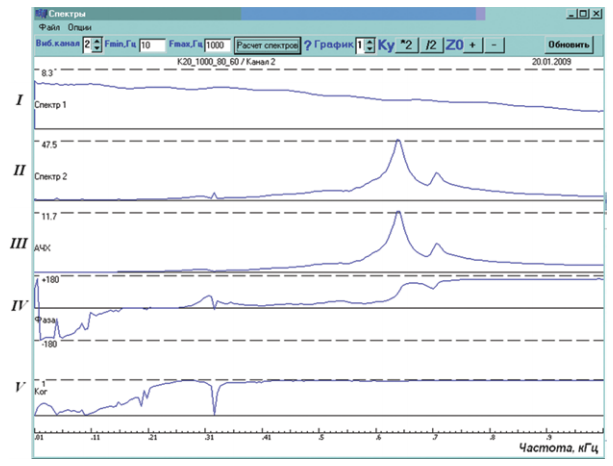
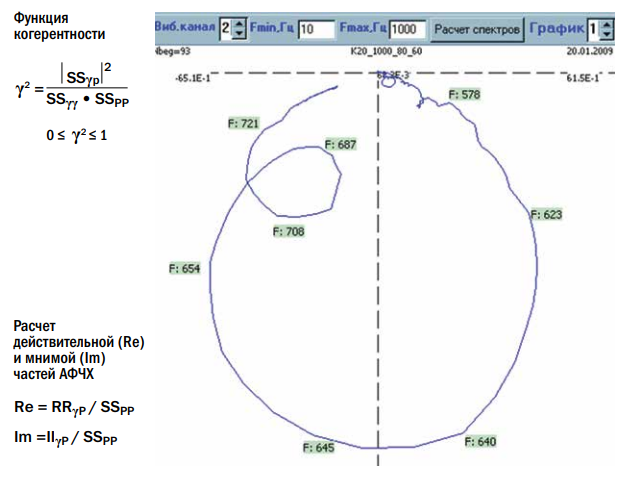
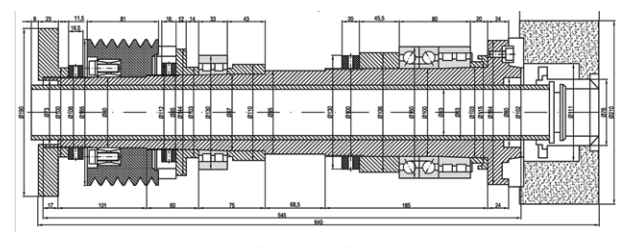
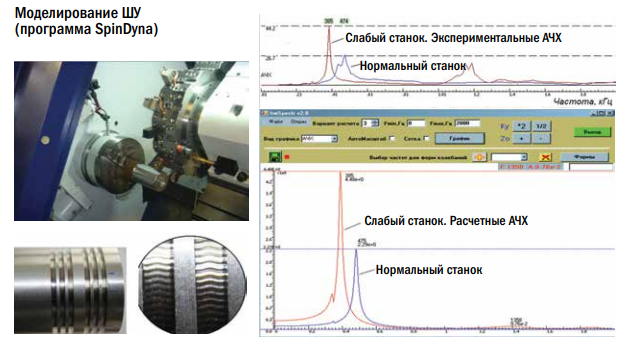
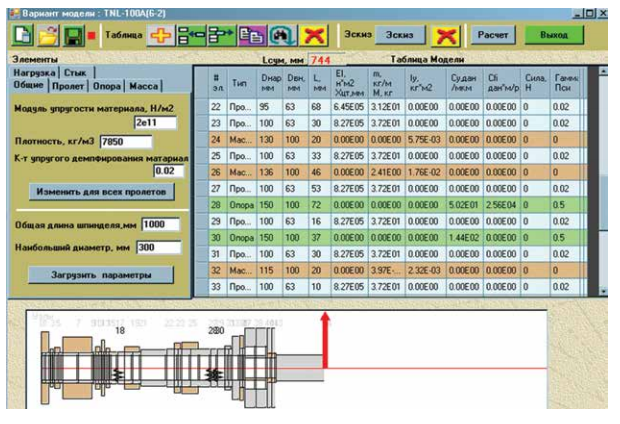
Состояние подшипников можно оценить по реакции на импульсное воздействие. Как невропатолог бьет пациента по коленке молотком и смотрит реакцию, а потом судит о состоянии нервной системы, так примерно и мы судим о состоянии станка по реакции на импульсное воздействие динамометрическим молотком. Ведется запись датчиков абсолютных колебаний акселерометром колебаний на это импульсное воздействие, а дальше идет спектральная обработка. Вся процедура наладки станка занимает не более получаса. В результате получаются характеристики, которые позволяют судить о его состоянии.
Недавно нам удалось решить проблему, которая стояла на заводе «Гидросила». Они купили два новых станка, один нормально работает, а другой — дробит. Изготовитель станка рекламацию не принимает. Мы провели испытания, весь комплекс испытаний занял два часа, в результате получили экспериментальные характеристики, а затем смоделировали шпиндельный узел и реально показали изготовителю, что у них проблема с двухрядным роликовым подшипником в передней опоре.
Когда мы по программе, по модели изменили жесткость подшипника в 6 раз, получили полное совпадение расчетно-экспериментальных характеристик. Им уже деваться было некуда, и они заменили шпиндельную балку на станке, и таким образом он был сдан.
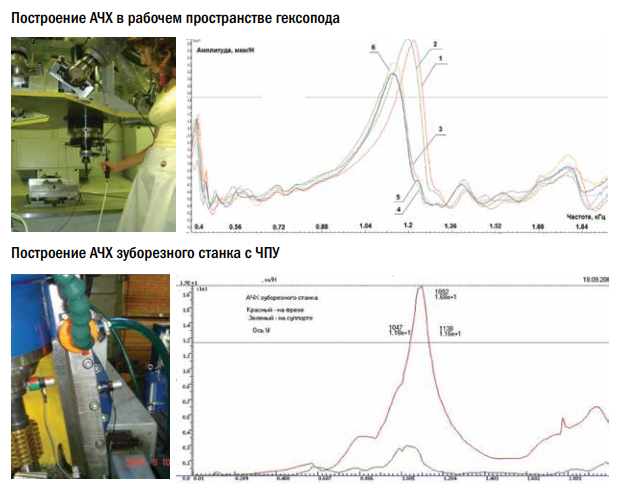
Ф. С. Сабиров, д.т.н., профессор, зав. кафедрой «Станки» МГТУ СТАНКИН
Журнал Prostoev.NET № 2(11), 2017
1 комментарий
Управление эффективностью мобильного оборудования горного производства | Prostoev.NET % · 20.02.2021 в 14:53
[…] готовности машин, оборудования, позволяет оценить ремонтопригодность машины, надежность ее и вообще управление, управление […]
Комментирование закрыто.