Из-за ограниченных ресурсов и смешанного парка, включающего как объекты долговременной эксплуатации, так и новые электростанции, могут возникнуть трудности с поддержанием различных мест контроля на одном уровне и отслеживанием данных, полученных с помощью программы обнаружения ускоренной потоком коррозии (FAC).
Кроме того новичкам в подобной области непросто выбрать локацию для начала проверки ввиду их многочисленности. Чтобы исправить данную ситуацию, следует использовать подход, основанный на оценке риска, который в первую очередь фокусируется на областях с наибольшим воздействием. Данный подход использует сетку рисков, или матрицу рисков, где составной балл можно получить с помощью формулы: Риск = Вероятность x Последствие (Р = В x П). Этот балл впоследствии может быть использован для определения наиболее уязвимых участков, нуждающихся в ресурсах, и установлении, какие последствия могут привести к травме персонала, серьезному повреждению оборудования и потерянной генерации.
Для начала нужно определить, какие механизмы влияют на ускоренную потоком коррозию на электростанциях. В целях данной статьи основное внимание будет уделено знаниям, полученным в ходе улучшения внутренней программы обнаружения ускоренной потоком коррозии для парка котлов, сжигающих бурый уголь на низкоэнергетических трубопроводах. Системы трубопроводов включают воду для питания котла, конденсат, дренаж подогревателя, пар в отборе, сепаратор воды для питания котлов и системы продувки котла. Как видно, даже при мгновенном устранении других систем трубопроводов электростанций все еще остается много компонентов, которые необходимо проверять по всему парку активов. Для более подробного изучения случаев, в которых ускоренная потоком коррозия наиболее вероятна, может пригодиться имеющаяся документация.
Списки, содержащие информацию о размерах трубопроводов, составе материалов, проектных и рабочих температурах, давлениях и объеме перекачки за единицу времени, представляют собой особую важность. Подобная информация позволяет оценить риски для завода и подверженность ускоренной потоком коррозии.
Промышленный опыт показал, что ускоренная потоком коррозия встречается преимущественно в системах с водяной или водно-паровой смешанной средой и трубопроводом из углеродистой стали, который эксплуатируются в диапазоне температур от 150 до 500 градусов по Фаренгейту. Получив информацию о температуре и давлении, вы сможете лучше понять степень перегрева и определить, есть ли в трубопроводе одно— или двухфазный поток. Согласно отраслевой информации, износ по причине ускоренной потоком коррозии усиливается при определенном диапазоне температур. Используя эту информацию, вы можете определить систему оценки в зависимости от того, где именно на кривой вы находитесь.
Например, температурный диапазон, вызывающий коррозию, может быть разделен на пять категорий, каждой из которых присваивается балл согласно оценке степени тяжести применительно к скорости износа. Этот же принцип применим для установления, где предприятие работает в диапазоне pH и каков объем перекачки за единицу времени в трубопроводе. Данные точки отсчета наряду с их оценками в итоге будут соответствовать вероятностной оценке восприимчивости.
Понятно, что не у всех есть детальная документация. В этом случае тепловой баланс — ваш следующий лучший союзник. Чтобы дать свою оценку сложившейся ситуации, рекомендуется посмотреть на восприимчивые к коррозии системы и получить базовое представление о температурах, давлениях и объеме перекачки за единицу времени. Проверить систему управления и посмотреть, что отображается во время работы завода, можно в операторной. Используя тот же вероятностный подход, можно задавать дополнительные вопросы, поскольку они относятся к химическим аспектам и эксплуатационным особенностям. Например, более старый участок мог подвергаться восстановительной химии, такой как гидразинно-аммиачный водный режим, или добавлению гидразина. В этом случае производственные объекты, работающие в условиях восстановительной химии, очень чувствительны к ускоренной потоком коррозии, поэтому необходимо провести тщательный анализ. Встреча с местной командой химиков позволит понять, в каком диапазоне рН изначально работала установка. Если речь идет об эксплуатации более новых производственных объектов, то, скорее всего, используются химические составы, обогащенные кислородом, такие как гидразинно-аммиачный водный режим (оксидировка) или кислородный водно-химический режим с более высоким pH.
Этот профиль, как было отмечено, почти полностью исключает вероятность развития коррозии в однофазных сплавах. Если это действительно так, то область поиска сужается до двухфазного потока в системах, где возможно мгновенное испарение, например, в секциях трубопровода дренажа подогревателя, после регулирующих клапанов. По мере сбора информации о трубопроводе, восприимчивом к коррозии, добавляйте ее в свой алгоритм оценки вероятности. Чем больше информации, тем точнее расчет. Если начнет казаться, что вы ограничены в информации, которую можете получить, не расстраивайтесь: недостаток информации и логический инженерный подход к определению вероятности лучше, чем вообще ничего.
Следующая часть уравнения является следствием расчета. Первым следствием, о котором следует подумать, является безопасность персонала. Определив участки трубопровода, которые наиболее подвержены коррозии, совершите обход и сфотографируйте каждое осмотренное место. Разработайте коммуникационный пакет и запланируйте время для встреч с операторами в диспетчерской, а также людьми, которые осуществляют обходы, и другими опытными работниками на предприятии, знающими наиболее загруженные участки. Дайте оценку, используя числовые значения. Например, наиболее загруженному участку присвойте значение 5, а участку с наименьшей нагрузкой — 1. Не стоит забывать о местах рядом с мастерскими, туалетами или любым другим участком, где персонал может иметь тенденцию собираться. Для более старых участков с асбестовой изоляцией следует добавить дополнительную категорию оценки, чтобы учесть повышенный риск для персонала.
Далее следует рассмотреть последствия повреждения оборудования. Выполняя обход, подумайте о том, что произойдет, если в этом месте произойдет утечка пара или разрыв. Есть ли распределительное устройство или другое электронное оборудование на данном участке? Обратите внимание на любое оборудование, которое в случае повреждения может привести к аварийному останову или потребует значительного перерыва в работе на период ремонта. Наконец, обсуждая участки с операторами, спросите, что произойдет с работой агрегата в случае разрыва трубы или утечки. Оцените ответы соответственно, например, 1 — не будет влиять на работу установки, тогда как 3 — может привести к ухудшению функциональных возможностей единицы, а 5 — к ее отключению.
Теперь вы готовы приступить к составлению таблицы рисков и перечня областей проверки. Пример таблицы рисков можно увидеть на рис. 1. В настоящем примере оценка была применена к различным категориям по осям X и Y, так что может быть отображена составная оценка степени риска. Далее таблица делится на секции в зависимости от показателей риска: низкий, средний, высокий и крайнее значение. Эта информация может быть применена к списку областей проверки и электронной таблице ранжирования рисков, пример которой можно увидеть на рис. 2. По мере выставления оценок каждому предложенному трубопроводу становится понятно, какие участки представляют наибольшую угрозу безопасности и производству. Эта информация также полезна в случае сокращения бюджета или простоя оборудования. Если возникнет любая из перечисленных ситуаций, вы будете владеть информацией, необходимой для принятия правильного решения, основанного на оценке риска, и поймете, где провести черту. Обязательно добавьте удаленное место проверки в план на следующий год.
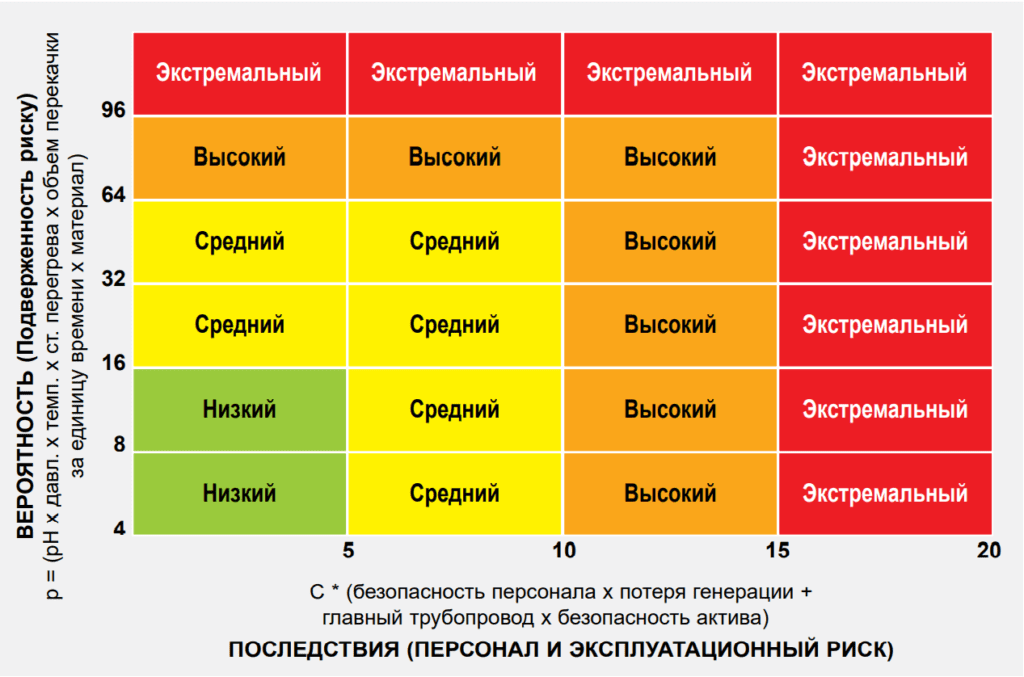
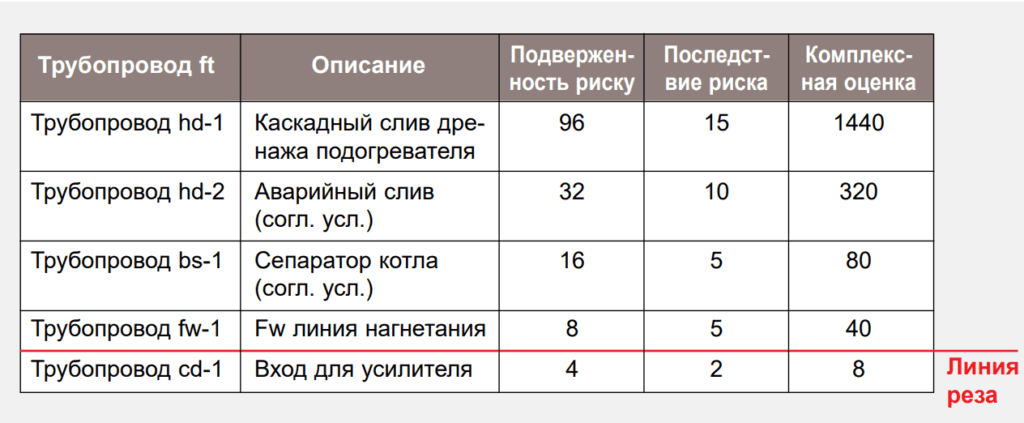
Подобный подход позволяет сосредоточить ресурсы и бюджет и вместе с тем снизить риски безопасности и производительности для вашего производственного парка. Он обеспечивает основу для оценки линий трубопроводов с использованием различных источников данных и институционных знаний.
Он также предлагает организованный подход к сбору и отображению данных для совещаний, входе которых будет распределяться бюджет на проведение дальнейших проверок. Наконец, он предлагает визуальный метод графического отображения информации, чтобы руководители проектов и руководители инспекций могли быстро представить руководителям направления области высокого риска и значительного воздействия, облегчая тем самым процесс принятия решений на основе данных и уменьшая подверженность трубопроводов к коррозии, ведущей к
серьезным поломкам.
Метод разработан Томасом Годби.
Т. Годби — специалист по надежности в компании Luminant Power, обслуживающий угольный завод по производству лигнита. Он является сертифицированным специалистом по надежности технического обслуживания, имеет ученую степень в области инженерного менеджмента в Cal State Long Beach, завершил Executive MBA (программа обучения бизнес-профессионалов с опытом работы) и получил степень бакалавра в области ядерных технологий в государственном колледже Томаса Эдисона. Томас также является ветераном Военно-морского флота США, оператором ядерных реакторов и техником-электронщиком в Программе по разработке ЯСУ для ВМС США.
Журнал Prostoev.NET № 4(21) 2019
По материалам зарубежных публикаций