В современных условиях растущих санкционных ограничений все больше затруднений вызывает эксплуатация зарубежного оборудования. Обеспечение запасными частями и материалами, получение доступа к сервисным услугам, проектной документации и технической поддержке, а также выполнение гарантийных обязательств – далеко не полный перечень вопросов, с которыми сейчас столкнулись отечественные предприятия.
Рекомендации, которые даются в этой статье, возможно, и не могут полностью снять указанные проблемы, но в большинстве своем позволят выиграть время для адаптации к сложившейся ситуации и поиска альтернативных решений.
Действенность предлагаемых подходов базируется на том, что настоящие рекомендации сформулированы, а иллюстрирующие их примеры приведены во многом на основе опыта эксплуатации зарубежного оборудования на территории Донбасса, промышленные предприятия которого в течение нескольких последних лет функционировали в жестких условиях экономических, финансовых, транспортных и других ограничений.
С целью систематизации и для удобства восприятия предлагаемые материалы структурированы в соответствии с последовательностью стадий жизненного цикла, как они рассматриваются в рамках методологии управления отказами оборудования. Каждая из выделенных стадий характеризуется особой спецификой возникающих и реализующихся на ней процессов. Обеспечение работоспособности и увеличение продолжительности эксплуатации зарубежного оборудования могут быть достигнуты только на основе понимания и учета его особенностей на всех стадиях жизненного цикла.
1. Проектирование: различия в подходах к управлению жизненным циклом оборудования
Для рациональной организации эксплуатации, в том числе технического обслуживания и ремонта (ТОиР), иностранного оборудования нужно понимать отличия доминирующих подходов к управлению жизненным циклом, на основе которых осуществляется его разработка у нас и за рубежом.
Для отечественной практики характерно применение подхода, нацеленного на максимизацию срока службы оборудования за счет реализации широкого комплекса работ по ТОиР. В противоположность этому за рубежом стремятся минимизировать работы по ТОиР в рамках предустановленного срока службы оборудования с последующей его плановой заменой.
Как следствие, зарубежное оборудование проектируется под заданный срок службы, практически без запасов прочности относительно планируемых нагрузок, с рассчитываемым минимально необходимым, но обязательным объемом работ по ТОиР. Преимущественное внимание при этом уделяется не восстановлению работоспособности (в идеале оборудование должно отработать свой срок службы без ремонта), а профилактическому техническому обслуживанию, замене (как правило, быстрой, поузловой) сменных и быстроизнашивающихся элементов.
2. Изготовление, транспортирование и хранение: дефекты и повреждения, полученные на доэксплуатационных стадиях – редки, но не исключены
Надежность оборудования не превышает верхний предел, заложенный на стадии проектирования, однако может оказаться значительно ниже вследствие недостаточного качества изготовления деталей и их последующей сборки, вероятность чего не исключается полностью и для зарубежного оборудования. Особенно актуальным это является в условиях поиска альтернативных поставщиков, среди которых могут оказаться работающие с недобросовестными производителями контрафактной продукции.
Так, встречались изделия, выполненные из материалов ненадлежащей марки, с несоответствующей микроструктурой, существенными отклонениями по твердости, что было вызвано отсутствием требуемой термообработки и другими нарушениями технологии изготовления. Ожидать удовлетворительной работы оборудования после установки таких запасных частей невозможно.
Неоднократно доводилось выявлять подшипники качения именитых производителей, которые были собраны из разукомплектованных, уже бывших в употреблении.
Например, возникают большие сомнения, чтобы знаменитая фирма SKF могла допустить на своих предприятиях выпуск подшипника с заваренной трещиной на сепараторе (рис. 1), хотя упаковка и сертификат были фирменными. С другой стороны, обвинять фирму FAG в небрежности, что привело к появлению следов коррозии на посадочной поверхности наружного кольца, также не следует (рис. 2). Это следствие того, что в процессе хранения не учли явления конденсации воды из теплого воздуха при охлаждении ночью.
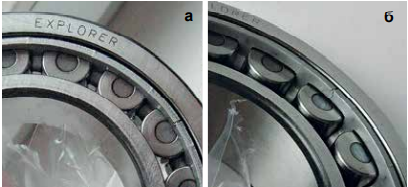
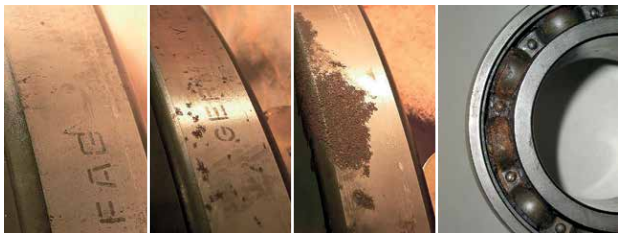
В этой связи отдельное внимание должно быть уделено усилению входного контроля поступающей продукции, особенно той, которая была получена из источников, еще не завоевавших доверия, а также строгому соблюдению требований по организации ее хранения.
Пример 1. После установки нового маслонасоса на компрессор проведены испытания в режиме холостого хода — подача масла без включения компрессора. При этом был выявлен нехарактерный шум и повышенный общий уровень вибрации.
После проверки осевого зазора между ротором насоса и корпусом, установки рекомендуемого
значения, начата обкатка маслонасоса в штатном режиме эксплуатации в составе компрессорной
установки.
В ходе анализа вибрации был выявлен значительный уровень виброскорости в районе подшипникового узла, а также высокие значения виброускорения. Это позволило локализовать район возможных повреждений и оценить их опасность как требующую осуществления немедленных ремонтных воздействий.
В спектре виброускорения присутствовали зубцовые составляющие, указывающие на повреждения деталей внутреннего зацепления, и энергетические, свидетельствующие о наличии металлического контакта и повреждений контактирующих поверхностей зацепления.
Повреждения развивались достаточно быстро, что позволило предположить наличие адгезионного схватывания. Это подтвердилось ростом температуры торцевой поверхности передней крышки, хотя там, исходя из конструкции насоса, трущихся поверхностей быть не должно.
Вал маслонасоса после обкатки рукой не проворачивался. Основные параметры работы (давление масла и ток нагрузки электродвигателя) соответствовали норме. При следующем включении маслонасоса произошла аварийная остановка компрессора – сработало тепловое реле маслонасоса. После этого он был демонтирован.
Разборка позволила установить:
1) на одной из торцевых поверхностей шестерни, на задней крышке насоса и на торцевой поверхности отдельных зубьев рабочего колеса обнаружены следы износа схватыванием второго
рода (рис. 3);
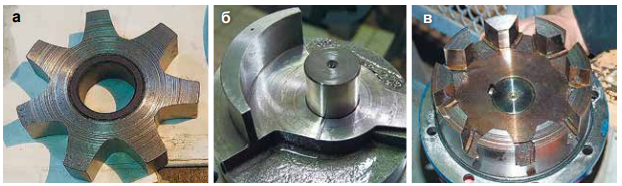
а) на торцевой поверхности шестерни; б) на задней крышке насоса;
в) на торцевой поверхности отдельных зубьев рабочего колеса
2) на краях зубьев другой торцевой поверхности шестерни и на боковых поверхностях рабочего колеса обнаружены затиры (засветления) поверхностей (рис. 4);
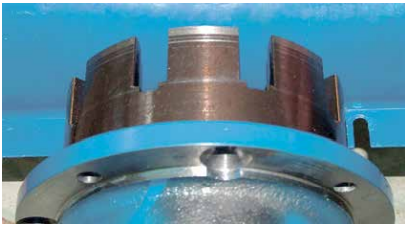
3) на рабочей поверхности корпуса насоса обнаружены засветления и признаки начальной стадии осповидного выкрашивания (рис. 5);
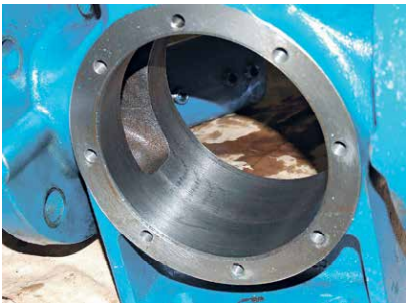
4) при затяжке стопорящих болтов муфты происходит подклинивание вала насоса.
Анализ выявленных повреждений позволил определить причину отказа – перекос валов маслонасоса и электродвигателя из-за непараллельности базовых поверхностей корпуса насоса или неправильной посадки подшипника, неправильно выставленный осевой зазор. Это привело к адгезионному схватыванию трущихся поверхностей и резкому повышению тока электродвигателя. Качество изготовления насоса можно оценить, как неудовлетворительное.
3. Ввод в эксплуатацию: высокая цена ошибок монтажа и наладки
Несмотря на заявленные ранее проблемы, наиболее вероятным сценарием развития событий является стабильная работа зарубежного оборудования в ограниченном временном интервале,
на котором оно не доставляет особых хлопот. Это достигается в случае соблюдения правил монтажа и наладки, в том числе при последующих ремонтах, которые, по сути, могут привносить на стадию эксплуатации все обозначенные здесь и ранее проблемы доэксплуатационных стадий жизненного цикла оборудования.
Помимо общей рекомендации по точному соблюдению указанных правил, акцентируем внимание на нескольких особенно важных моментах. Так, затяжку резьбовых соединений следует проводить динамометрическими поверенными ключами в строгом соответствии с требованиями документации. А, например, смещение при центровке на 0,06 мм при допуске 0,05 мм уже расценивается за рубежом как нарушение гарантийных условий.
Пример 2. Соединение валов электродвигателя и насоса осуществляется компенсирую муфтой с упругими элементами. На заводе-изготовителе насос и электродвигатель закрепляют на раме с допустимыми отклонениями от соосности.
Нарушения соосности возможны при транспортировке, установке, монтаже трубопроводов, заполнении системы жидкостью. При этом в 70-90% случаев центровка насосов после их монтажа на самом деле не проводится.
Если отклонения лежат в пределах допуска компенсирующих возможностей соединительной муфты, это приводит к повышенной вибрации, появлению дополнительных нагрузок и снижению ресурса подшипников, износу вкладышей муфты, износу торцевого уплотнения.
Если отклонения становятся значительными (рис. 6) и достигают 2,0 мм и более, эксплуатация насоса после запуска сопровождается повышенным шумом, вибрацией и нагревом подшипников. Своевременная остановка приведет только к разрушению вкладышей муфты, состояние подшипников и торцевого уплотнения удается сохранить.
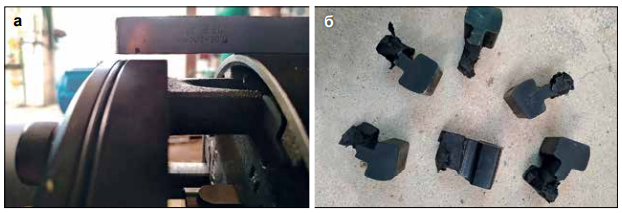
Затяжка резьбовых соединений, установка нового комплекта упругих вкладышей муфты и точная центровка валов двигателя и насоса с точностью 0,05 мм (при частоте вращения 3000 об/мин) позволяют продолжить эксплуатацию. После нескольких дней работы, по завершении приработки, среднеквадратичное значение виброскорости снижается.
Длительность последующей эксплуатации зависит от качества и своевременности технического обслуживания, к которому относятся проверка затяжки резьбовых соединений, проверка соосности
(каждые шесть месяцев), периодическое смазывание узлов, контроль параметров вибрации и др.
Пример 3. Первый запуск насоса выполнен после проведения точной центровки и последовавших за ней работ по установке фильтра на всасывающем трубопроводе. Повторная центровка после ремонта не проводилась. Оценка технического состояния осуществлялась путем измерения уровня вибрации в контрольных точках (рис. 7) и сравнения с нормативными значениями, регламентированными ГОСТ ИСО 10816-1-97. Результаты измерения виброскорости, представленные в табл. 1, указывают на повышенный уровень вибрации, в частности в осевом направлении, что характерно при нарушении соосности.
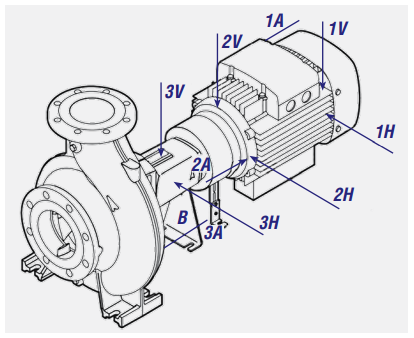
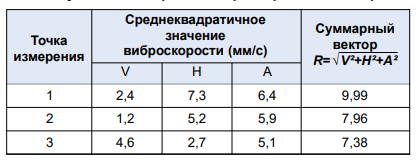
Отклонения от соосности до и после центровки определены по показаниям лазерного центровщика, дополнены значениями суммарных отклонений и представлены в табл. 2. Отклонения от соосности оказались на уровне максимальной точности «грубой» центровки (~0,2 мм), что превысило компенсирующие возможности муфты.
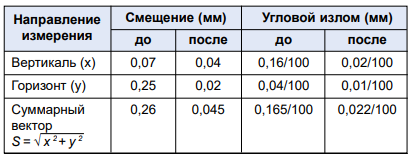
После проведения центровки и приведения отклонений соосности в поле допуска значения виброскорости уменьшились (табл. 3).
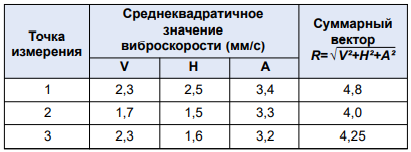
Суммарные векторы вибрации по контрольным точкам уменьшились практически в два раза и стали соответствовать зоне В (машины, пригодные для дальнейшей эксплуатации без ограничения сроков).
4. Эксплуатация: обеспечьте благоприятные условия эксплуатации
Эксплуатация является самой важной стадией жизненного цикла оборудования, на которой реализуется его ценность. Чтобы сделать эту стадию продолжительной и наименее проблематичной, предусмотрены четкие и выверенные требования, которые устанавливаются технической документацией на зарубежное оборудование. Для него каждая деталь в правилах технической эксплуатации существенна и критична. Как для любой глубоко оптимизированной системы, даже незначительные отклонения зачастую ведут к непредсказуемым последствиям.
В сложившихся на отечественном пространстве условиях не все требования могут быть выполнены, тем более своевременно, но негативное влияние этих факторов должно учитываться при эксплуатации зарубежного оборудования. Как и любые случайные воздействия внешних факторов, это способно оказать критическое влияние на работоспособность и долговечность оборудования.
Пример 4. Компрессорная установка мощностью 4 МВт с частотой вращения приводного двигателя 1500 об/мин, и частотой вращения ступеней компрессорного блока 199 Гц, 225 и 277 Гц (рис. 8) находилась в эксплуатации с 2005 г. Замечаний, поломок, отказов до 2020 г. не было. После резкого увеличения виброскорости с 1,0 мм/с до 4,0 мм/с поставлен диагноз – повреждение соединительной муфты. При осмотре выявлены деформация и разрушение упругих пластин муфты.
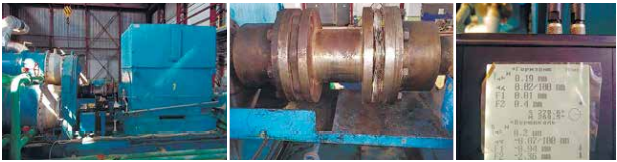
Причина повреждения – частые запуски и внезапные остановки вследствие падения напряжения электрической сети. Дополнительно установлено наличие расцентровки до 0,2 мм параллельного смещения по горизонтали и вертикали.
После изготовления и установки новых пластин соединительной муфты виброскорость снизилась до 0,9 мм/с.
4.1. Техническое обслуживание
Обеспечение благоприятных условий эксплуатации зарубежного оборудования, что достигается, в том числе, за счет своевременного проведения предусмотренных документацией операций по техническому обслуживанию, имеет критическое значение.
Особое внимание должно уделяться равномерности затяжки резьбовых соединений. В противном случае большую часть нагрузки несет наименее затянутый болт, что приводит к его разрушению и последующему отказу оборудования.
Пример 5. Ослабление резьбовых соединений происходит в период длительной эксплуатации, чему способствуют колебания температуры и вибрация, или после ремонта, как следствие забывчивости персонала.
Затяжка резьбовых соединений по окончанию отопительного сезона показывает, что наиболее податливыми являются анкерные болты крепления рамы. В рассматриваемом случае это проявилось в повышении виброскорости в вертикальном направлении на раме насоса свыше 2,0 мм/с.
Большее влияние на значения вибрации оказало ослабление резьбового соединения вертикальной опоры В (см. рис. 7) с консольным корпусом насоса.
Причина ослабления – воздействие вибрации и ошибки при ремонте. Ошибки при проведении ремонта обнаружились по значениям виброскорости (табл. 4) до проведения ремонта (1), после проведения ремонта (2) и после затяжки резьбового соединения опоры В (3).
Анализ данных позволяет констатировать следующее:
– повышенные значения виброскорости до проведения ремонта указывали на необходимость замены подшипников;
– после замены подшипников значения виброскорости возросли по двигателю в полтора, а по насосу – практически в три раза;
– после затяжки резьбовых соединений опоры В значения вибрации упали ниже уровня перед
проведением ремонта;
– цель ремонта не была достигнута, а работа с повышенной вибрацией привела к интенсивному накоплению повреждений в подшипниках насоса, что отразилось на их ресурсе.
Изменение режима смазывания (свойств, расхода смазочного материала, условий отвода смазки, ее загрязнение и др.) приводит к износу подшипников. Обнаружить малые отклонения по диагностическим параметрам вибрации весьма затруднительно. Часто износ проходит постепенно и незаметно. Кроме того, медленно накапливающиеся повреждения практически невозможно отследить органолептическими методами. Для предупреждения отказа в этом случае рекомендуется с периодичностью в 4-10 дней проводить диагностирование технического состояния оборудования по вибрационным, тепловым, токовым и другим параметрам.
4.2. Ремонт
Опыт по устранению отказов оборудования растет пропорционально объему проведенных ремонтов и убывает по экспоненциальной зависимости. Высокая надежность зарубежного оборудования зачастую не позволяет сервисной службе предприятия должным образом подготовиться к ликвидации всего спектра возможных неисправностей, что может привести к возникновению аварийных ситуаций, требующих длительного периода устранения.
Пример 6. Первый ремонт зарубежного винтового компрессора произошел из-за износа подшипников вследствие неверной технологии замены марки смазочного материала. Для консультации пригласили специалиста, имевшего представление о технологии ремонта. Три дня ознакомления привели к двухнедельному изготовлению необходимых приспособлений и пятидневному ремонту.
Второй ремонт произошел из-за нештатной ситуации – попадания жидкости в аммиачный компрессор. Однако этот ремонт был проведен уже всего за два дня.
Пример 7. Зарубежный комплекс по переработке металлургических шлаков практически без
замечаний отработал около шести лет. За этот период руководство предприятия в целях экономии средств постепенно отказалось от сервисного обслуживания фирмой, лицензированной производителем (сами справимся), от материалов (смазки были заменены на отечественные), запасных частей от изготовителя (дороговизна и сложности логистики). Кроме того, как выяснилось, не был даже приобретен комплект технической документации.
В итоге этот «черный ящик» таки начал отказывать. В результате аварийной остановки элементы оборудования, подлежащие поузловой замене, привычными способами отремонтировать не удалось. Пришлось их вскрывать, по месту эскизировать, менять подшипники на другие по типоразмеру, что привело к необходимости внесения изменений в конструкцию узла. Стоит ли говорить, в каком авральном режиме проходили разработка проектной документации и изготовление запасных частей. Несмотря на это, восстановление работоспособности комплекса потребовало десятидневного простоя с миллионными потерями.
P.S.: Участникам фотосессии (рис. 9) того эпического ремонта хотелось бы напомнить, что на подшипнике не должно быть следов коррозии, монтаж следует выполнять в перчатках, класть подшипник на поверхность, содержащую абразив, не допускается даже в случае наличия защитных шайб. Эти и другие требования к выполнению ремонтных работ позволяют обеспечить длительную эксплуатацию оборудования.
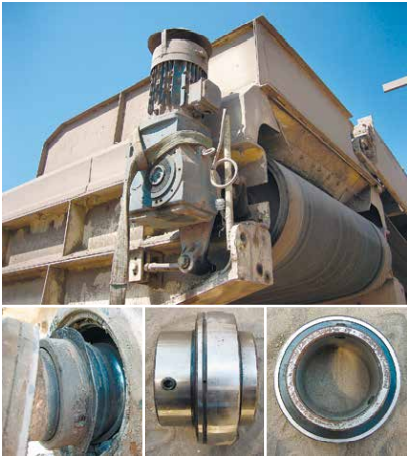
В разрезе рассмотренного примера возникает вопрос, насколько возможно справиться с задачей обеспечения запасными частями своими силами или с привлечением отечественных машиностроительных предприятий. Здесь есть два принципиальных подхода: пытаться восстановить имеющиеся детали либо изготавливать новые.
Как показывает практика коллег, восстановление имеющихся деталей ведет к поэтапному и усугубляющемуся снижению долговечности и надежности восстановленных элементов оборудования. После износа первоначальные характеристики таких деталей нередко проблематично установить и, соответственно, воспроизвести.
Кроме того, в отличие от отечественного машпрома, зарубежные производители не следуют привычным нам требованиям по взаимозаменяемости и стандартизации, но широко используют ноу-хау (специфичные материалы, размеры, способы изготовления, термообработки, инженерные решения и т.д.) для защиты своей продукции и удержания позиции на рынке.
Пример 8. Попытка воспроизвести марку бронзового сплава вкладышей для экспандеров в условиях отечественного предприятия снизила срок их службы до 3-6 месяцев вместо трех лет. Секрет был связан с технологией микродобавок и термообработки вкладышей.
В разрезе сервисного обслуживания зарубежного оборудования также часто озвучивается вопрос о возможности организации планово-предупредительных работ, их периодичности и содержания.
Постараемся разобраться в вопросе более подробно, исходя из того, что рекомендаций по осуществлению плановой замены запасных частей завод-изготовитель не предоставил, либо они по тем или иным причинам недоступны (в противном случае наиболее правильным решением было бы воспользоваться указанными рекомендациями).
Итак, в нашем распоряжении есть четыре основных концепции ТОиР, которые представлены в табл. 5.
Агрегативные концепции ТОиР – такие, как ориентированная на надежность (RCM), базирующаяся на оценке рисков (RBM) и другие подобные – намеренно опускаются, поскольку, во-первых, основаны на применении указанных, а во-вторых, в случае наличия на предприятии компетенций, необходимых для их реализации, вопросов, подобных рассматриваемому, уже не возникает. Безусловно, в целом для их решения можно было бы рекомендовать RCM или RBM в качестве универсального средства, но в текущих условиях это равносильно тому, чтобы тонущему предложить научиться плавать – освоение и внедрение потребуют значительного времени
и вложений.
Поэтому вернемся к основным концепциям ТОиР. Можем ли мы эксплуатировать зарубежное оборудование до отказа? Можем – обеспечивая при этом благоприятные условия эксплуатации путем своевременного проведения технического обслуживания. Это позволит с минимальными затратами полностью использовать ресурс оборудования, а в процессе этого рассмотреть вопрос замены на отечественные или более доступные аналоги после выхода его из строя.
Однако если после отказа планируется оборудование восстановить и эксплуатировать дальше, это далеко не лучшая стратегия, поскольку внезапный отказ, помимо прочего, нередко становится причиной вторичных повреждений. Так, например, заклинивший подшипник может привести к повреждению посадочных мест на валу или даже разрушению корпуса. Восстановление в этом случае окажется на порядок более затратным, чем своевременная замена.
Но можно ли здесь реализовать планово-предупредительный подход? Увы, в большинстве случаев нет. Как правило, сведений об опыте эксплуатации аналогичного оборудования у предприятия редко оказывается достаточно для того, чтобы получить результаты статистической обработки данных с приемлемым уровнем погрешности. В силу корпоративной специфики также малоприменим опыт, полученный на других отечественных и зарубежных предприятиях, да и они не так уж спешат им делиться. По тем же причинам не удастся воспользоваться методом аналогий, перенося на зарубежное оборудование ремонтные циклы и содержание планово-предупредительных работ, которые известны для другого однотипного оборудования, либо из справочников. Технические и технологические отличия могут слишком существенно влиять на ресурс.
Поэтому наиболее приемлемым и целесообразным видится перевод такого оборудования на ТОиР с применением одной из концепций, опирающихся на сведения о фактическом техническом состоянии.
Обеспечение благоприятных условий эксплуатации за счет проведения комплекса работ по техническому обслуживанию, с одной стороны, и применение методов и средств технической диагностики, с другой стороны, по мнению авторов, позволяют сформировать оптимальную организацию системы ТОиР для зарубежного оборудования.
4.3. Техническое диагностирование
В условиях ограниченного доступа к зарубежным рынкам оборудования, запасных частей и материалов особое значение приобретает периодический контроль технического состояния оборудования, который позволяет на ранних стадиях выявлять неисправности и не только предупреждать внезапные отказы, но и за счет реализации проактивных мероприятий снижать скорость развития повреждений.
Пример 9. Для получения необходимого разряжения при вакуумировании стали предусмотрены пять линий (рис. 10), в каждой из которых установлены по три агрегата – бустерные насосы и винтовые компрессоры. Работа вакууматора требует включения трех линий, вполне достаточный запас надежности вроде внушает доверие. Однако менее чем за 10 месяцев гарантийной эксплуатации из строя вышли три бустерных насоса, на одном подшипники были заменены, еще
один насос ремонту не подлежал.
Работа без резерва повысила опасность срыва производственной программы предприятия. Было принято решение организовать вибрационный контроль механизмов перед запуском. В результате использование информации о техническом состоянии оборудования позволило организовать безотказную работу насосов вакууматора при отсутствии резервирования в течение трех месяцев. Обнаруженные на основании вибрационного контроля неисправности оперативно устранялись установкой исправного оборудования на рабочих линиях.
Применение приборных методов технической диагностики еще не значит автоматически своевременное выявление неисправностей. Во многом диагностирование продолжает оставаться искусством, в значительной степени зависящим от уровня мастерства, экспертности специалиста. Это указывает на необходимость обучения и повышения квалификации таких специалистов.
То же относится к обслуживающему, а еще в большей степени к эксплуатационному персоналу. Обучение органолептическим методам технической диагностики, приемам технического обслуживания и их качественному выполнению – далеко не полный перечень навыков, которые следует прививать.
Все это позволяет не только обеспечить более раннее выявление отклонений в работе оборудования, но и снизить вероятность внештатных ситуаций, в результате которых стремительное развитие повреждений не всегда дает возможность вовремя разобраться в ситуации с применением приборных методов.
Пример 10. Считается, что, если известна скорость развития конкретной неисправности объекта, характеризуемая скоростью изменения значения диагностического параметра, то возможно составление прогноза. Применение этого положения на практике нередко приводит к возникновению аварийных ситуаций.
Оценка технического состояния винтового компрессора проводилась по результатам вибромониторинга параметров общего уровня вибрации и периодически проводимого спектрального анализа (рис. 11).
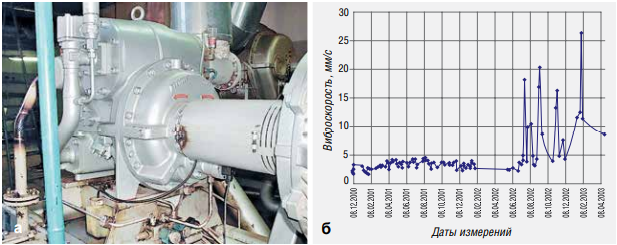
В течение двух лет работы не было зарегистрировано значительных отклонений, уровень вибропараметров был стабилен и не превышал 3,6-5,2 мм/с.
После аварийной остановки компрессора в результате отключения электроэнергии во время грозы в маслосистему попало значительное количество загрязняющего материала (гликоля) из-за повреждения теплообменной трубки в кожухотрубном испарителе системы промежуточного охлаждения. Вибрация компрессора стала увеличиваться, среднеквадратичные значения виброскорости составили – 12,0…16,0 мм/с. Именно в этот период начался ускоренный износ ведомого ротора, что выразилось в износе подшипников, износе шейки вала, неравномерном износе ротора.
Увеличение вибрации по результатам предыдущих измерений предсказать было невозможно. Таким образом, внешнее воздействие окружающей среды, повреждения сопряженных узлов привели к существенному изменению до этого стабильной картины износа.
Вывод из эксплуатации: следим за сроком службы
Хорошо разработанные, проверенные методики расчета на усталостную прочность, широкое применение средств компьютерного моделирования и точное соблюдение технологии позволяют зарубежным производителям изготавливать преимущественно высококачественное оборудование, но при этом с ограниченной долговечностью, о чем нередко забывают при эксплуатации на отечественных предприятиях.
Пример 11. При поставке оборудования для сварки труб большого диаметра немецкая фирма гарантировала работу в течение трех лет. После 40 месяцев эксплуатации появились первые признаки износа, а через 42 месяца потребовалась замена вал-шестерен первых валов редукторов. Стоимость изготовления новых валшестерен была сопоставима со стоимостью изготовления нового редуктора.
Пример 12. Прокатные клети для изготовления дорожных отбойников в количестве восьми единиц без существенных замечаний отработали восемь лет. Первые отклонения в работе были диагностированы по появлению бракованной продукции. Рекомендация специалиста фирмы-изготовителя – заменить прокатные клети – вызвала недоумение у руководства завода. Видимо, предполагалось, что оборудование будет работать бесконечно долго…
Пример 13. При производстве минераловатной плиты в камере волокноосаждения используется барабан, вращающийся на двух вертикально установленных четырехметровых шариковых опорных кольцах. После трех месяцев эксплуатации в опорном кольце начали прослушиваться приглушенные стуки. Специалисты зарубежной сервисной компании, присланные для выполнения гарантийных обязательств, добавили в кольцо 20 тел качения и уверили руководство, что более шести месяцев эти опорные кольца при вертикальном расположении не работают.
Срок в шесть месяцев заканчивался, средств для замены опорных колец не было. Через 2-3 недели после начала наблюдений за состоянием опорного кольца появились приглушенные непериодические стуки в одном из подшипников. Осмотр тел качения ø32 мм через монтажное отверстие ø35 мм показал, что подшипник бессепараторный, между шариками установлены полиамидные вставки. Вертикальное расположение опорного кольца приводило к местной нагрузке наружного кольца, а нехватка шариков – к ударам по полиамидным вставкам.
Благодаря тому, что дополнительный комплект тел качения и вставок имелся в ЗИП, разрушенные вставки были заменены на новые, а количество тел качения увеличено еще на 10. После проведенных работ подшипник проработал еще полгода. Затем наружное кольцо было повернуто на 90°, и начался еще один год эксплуатации.
Таким образом, техническая смекалка, принятие решений на основе информации о техническом состоянии, своевременное и качественное техническое обслуживание способны продлить работу зарубежного оборудования сверх гарантийного срока службы, в том числе в текущих условиях турбулентности и ограничений.
Выводы
Ситуация, сложившаяся в настоящее время на отечественном пространстве, формирует новые угрозы и вызовы, связанные с необходимостью обеспечения эксплуатации зарубежного оборудования в условиях ограниченного доступа к иностранным рынкам товаров и услуг.
Для решения комплекса указанных проблем в статье на основе опыта эксплуатации такого оборудования на предприятиях Донбасса даются следующие рекомендации:
- Необходимо изначально разработать, а затем придерживаться оптимальной для предприятия стратегии управления жизненным циклом зарубежного оборудования, которая может включать заблаговременное приобретение проектной документации или достаточного количества запасных частей, проработку вариантов внесения изменений в конструкцию или поиск альтернативных каналов снабжения и т.д.
- Особое внимание должно быть уделено организации эффективного входного контроля запасных частей, материалов и оборудования, поступающих от поставщиков.
- Операции по монтажу и наладке зарубежного оборудования должны выполняться в строгом соответствии с требованиями технической документации. Обеспечение затяжки резьбовых соединений и соосности как на этой стадии, так и на последующих, является важным фактором, оказывающим значительное влияние на техническое состояние оборудования и возможность его длительной эксплуатации.
- Техническое обслуживание должно выполняться по возможности своевременно и в полном объеме.
- В ходе эксплуатации следует минимизировать риски неблагоприятного воздействия внешних факторов (окружающей среды, неквалифицированных действий эксплуатационного и обслуживающего персонала).
- Высокая надежность зарубежного оборудования зачастую не позволяет сервисной службе должным образом подготовиться к ликвидации всего спектра возможных неисправностей, что может приводить к возникновению аварийных ситуаций, требующих длительного периода устранения.
- Ремонт зарубежного оборудования в ряде случаев может быть сопряжен с существенными трудностями, поскольку нередко подразумевает поузловую замену элементов оборудования, а не замену отдельных деталей. Сложности могут возникнуть как с попытками воспроизвести, так и с попытками восстановить детали, материал и технология изготовления которых часто содержат элементы ноу-хау производителя.
- При выборе концепции ТОиР для зарубежного оборудования следует предпочесть:
а) эксплуатацию до отказа, если дальнейшее восстановление работоспособности оборудования не планируется;
б) планово-предупредительные работы, если такие предусмотрены технической документацией производителя;
в) обслуживание по техническому состоянию, в том числе проактивные воздействия, если предприятие располагает такими возможностями либо может привлечь сторонних специалистов;
г) агрегативные концепции ТОиР (RCM, RBM), если указанные уже практикуются на предприятии и сотрудники обладают соответствующими компетенциями.
После окончания гарантийного срока службы техническое состояние зарубежного оборудования может быстро деградировать, о чем следует помнить и к чему следует готовиться. Тем не менее в ряде случаев продолжительность эксплуатации может быть существенно увеличена.
Непрерывное обучение и повышение квалификации персонала, в особенности эксплуатирующего и обслуживающего оборудование – неотъемлемое условие для обеспечения его длительной, безопасной и безаварийной работы.
Журнал Prostoev.NET № 1(30) 2022
А.В. СИДОРОВ, Ассоциация эффективного управления производственными активами (Ассоциация ЕАМ)
В.А. СИДОРОВ, Донецкий национальный технический университет