Реализация подходов TPM, таких как автономное обслуживание, становится все популярнее у российских предприятий. Существует много литературы и статей, описывающих преимущества данного подхода, но это все теория.
В этой статье мы поделимся своим практическим опытом внедрения ТРМ: с какими трудностями придется столкнуться, и пути их преодоления.
TPM (Total Productive Maintenance — всеобщее обслуживание оборудования) — это один из инструментов бережливого производства, применение которого позволяет снизить потери, связанные с простоями оборудования из-за поломок.
Как правило, решение о внедрении тех или иных инструментов исходит от руководства, и здесь самое главное — создать необходимую информационную поддержку на всех уровнях по всем возможным каналам, таким как:
- газета и интернет-ресурсы, предприятия;
- информационные доски предприятия;
- встречи руководства с коллективом;
- еженедельные и ежедневные планерки;
- закрытие/открытие смен
— через которые простым и понятным языком доносится информация о предстоящих изменениях с описанием этапов реализации изменений, указанием подразделений, кого коснутся изменения, и их роли, а также выгод для работников соответствующих подразделений и компании в целом. Конечной целью информационной поддержки должно быть сформированное понимание работников, что изменения необходимы и неизбежны, что от этих изменений будет всем только лучше.
На этапе информационной поддержки мы описываем текущее состояние и этапы преобразования, составляется план-график реализации проекта.
Повышение эффективности работы технических служб планируется осуществлять в 6 этапов (этапы 3–5 могут идти параллельно)
Ситуация до начала внедрения проекта:
- Не проверяется состояние оборудования перед запуском.
- Недостоверная информация об остановках производства.
- Слабый фокус системы на предупредительных ремонтах.
- Недостаток персонала в дежурной службе.
- Технический персонал часто узкоспециализирован.
- Часто нет согласованности внутри ТО (например, электрики и электронщики).
- Система поиска первопричин поломок развита слабо.
Оптимизация:
- Система обходов осмотров.
- Изменение системы учета простоев.
- Создание и внедрение системы ППР.
- Обучение базовым ремонтам.
- Реорганизация ТО.
- Постоянное совершенствование системы.
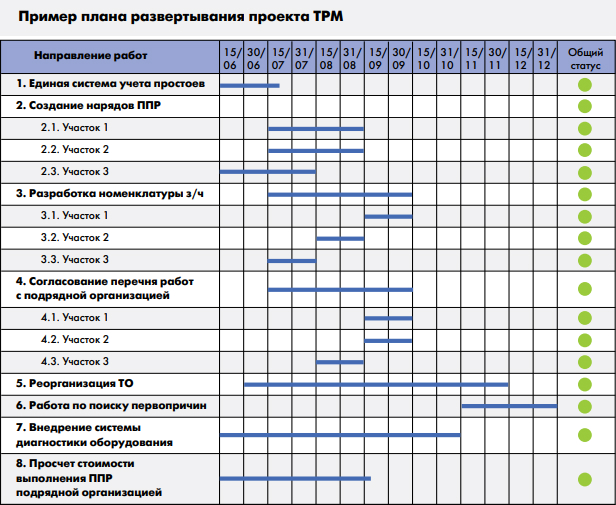
Наверное, самое сложное — это изменить отношение служб к процессу обслуживания и ремонта оборудования, искоренить извечный спор между производством и технической службой. Из «противоборствующих» сторон создать тандем, который будет решать общие задачи для достижения общих целей.
Для этого необходимо разграничить зоны ответственности подразделений, обозначить роли каждого участника. С самого начала реализации проекта ТРМ нужно максимально вовлекать работников соответствующих подразделений, формируя из них кросс-функциональные команды для разработки стандартов осмотра и обхода оборудования, регламентов взаимодействия между службами и т. д. Как правило, в кросс-функциональную команду входят менеджер проекта ТРМ в роли модератора, мастер участка, лучший оператор, механик, слесарь и технолог, при необходимости также привлекаются электрик, электронщик и другие необходимые специалисты. На этом этапе нужно ввести небольшую доплату для всех участников таких команд, кроме менеджера проекта ТРМ (это и так его работа). Вовлекая работников в изменения, мы убиваем несколько зайцев сразу. Во-первых, даем чуть заработать участникам команд — это будет для них приятно и послужит хорошим мотиватором. Во-вторых, вовлекая работников из разных подразделений в совместную деятельность, мы налаживаем конструктивное взаимодействие между подразделениями на базовом уровне. В-третьих, документы, которые разрабатывают участники команд, потом сами же и будут исполнять, это сильно упростит их дальнейшее внедрение.
Во время внедрения любых изменений есть группа работников, кто за изменения, и есть группа, кто против изменений, эти группы примерно равны и в сумме составляют примерно 15–20 %, а остальные 80 % — это те, кто пойдет туда, куда «подует ветер». Привлекая на разработку лучших операторов, которые являются неформальными лидерами, мы тем самым большую часть из 80 % привлекаем на сторону группы, которая за изменения.
Результатом работы кросс-функциональных команд является разработанная и согласованная Система постоянной диагностики оборудования, которая включает в себя алгоритм взаимодействия между службами, стандарт осмотра оборудования оператором, стандарт обхода оборудования слесарем и визуальную поддержку в виде доски обхода.
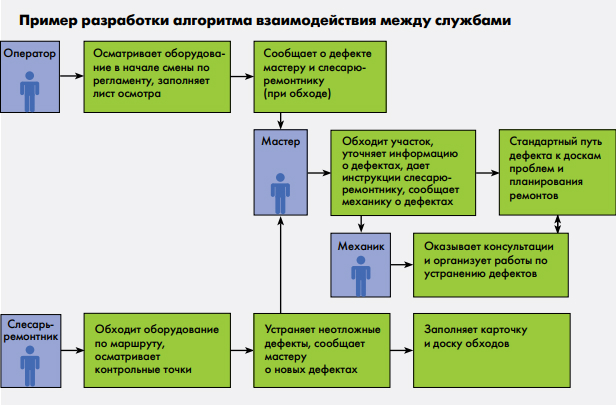
Пример визуализации основных точек осмотра оборудования оператором
Основные точки, которые должен проверить оператор при осмотре линии
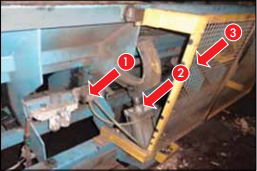
Сброс, визуально проверить:
- Недопустимая утечка воздуха на пневмоприводе (свищ слышно).
- Исправное состояние механизмов сбрасывателя.
- Наличие, надежность крепления ограждения.
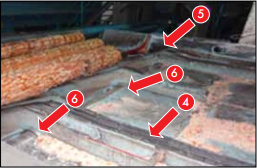
Накопитель, визуально проверить:
- Натяжку и состояние цепей.
- Исправность бортов.
- Состояние подшипников скольжения ведомых колес привода цепи (наличие бронзовой стружки соответствует сильному износу).
При обнаружении неисправности во время осмотра оборудования отметить неисправность в соответствующей графе в чек-листе приема-передачи смены, сообщить о ней мастеру смены.
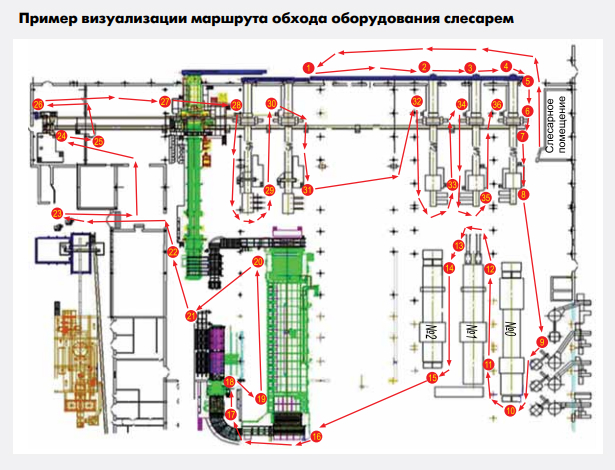
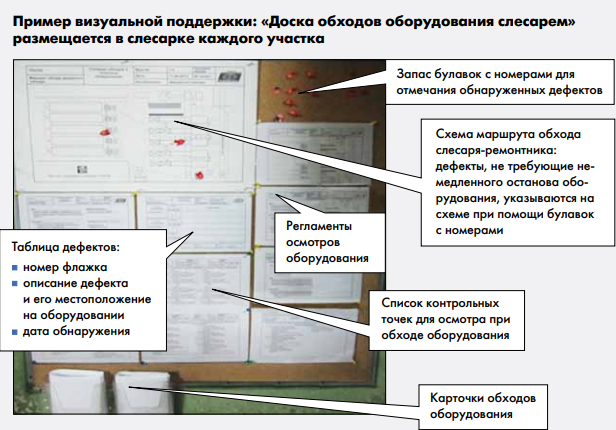
Не редкость, что на предприятиях фиксация и учет простоев ведутся в свободной форме, «кто как умеет», без четкой классификации. В своей работе нам встречались предприятия, где простои фиксировали производственники в своей форме, а техническая служба — в своей, и по итогам месяца службы «бодались» друг с другом за часы простоев, перекладывая вину друг на друга. Об анализе простоев, поиске их первопричин никто и не задумывается. Да что говорить, встречались предприятия, где простои вообще никем никак не фиксировались. Есть компании, где простоем считается только то, что повлияло на выполнение плана производства, где простоем является останов производства на сутки. К чему это все? Для того чтобы на что-то повлиять, нужно иметь понятную и достоверную систему измерения этого чего-то. Система учета простоев должна быть с необходимой детализацией, простой, понятной, чтобы в дальнейшем позволяла проводить анализ и поиск первопричин простоев.
Этап разработки и внедрения системы учета простоев лучше начинать параллельно с разработкой необходимых нормативных документов, о которых мы написали выше.
Система учета простоев может включать в себя:
- бланк регистрации простоев, где фиксируется время останова и ремонта, определяется группа простоя и указывается причина простоя и действия по его устранению;
- каскад звонков — последовательное информирование о поломке, эскалация проблемы с четко определенными временными рамками;
- картографию линии — документ, позволяющий определить приоритет поломки, правильно скоординировать технический персонал.
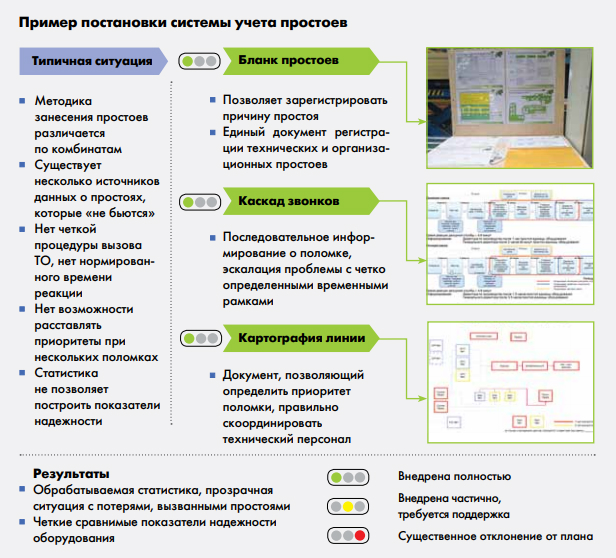
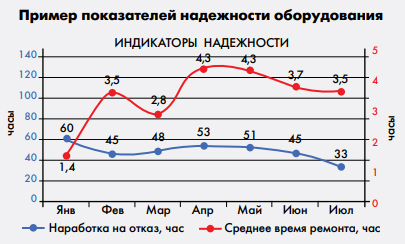
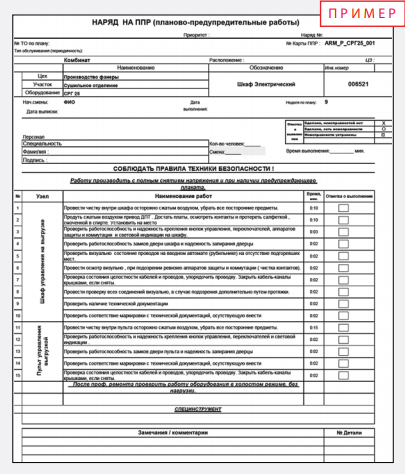
Система учета простоев также служит для построения показателей надежности оборудования, что в свою очередь является ключевым показателем эффективности (КПЭ) работы ремонтной службы.
Одним из самых длительных и трудоемких этапов является разработка нарядов плановопредупредительных ремонтов (ППР). В первую очередь наряды ППР разрабатываются на оборудование, которое является узким местом с точки зрения производительности. В наряде ППР указывается исполнитель, № карты ППР, оборудование, узел, наименование работ и время на выполнение каждой работы.
Управление запасными частями на предприятиях зачастую сводится к заявке в отдел снабжения на покупку вышедшего из строя узла. На складе обычно хранят расходные материалы, а вот слесарные мастерские — это кладезь, но обычно там трудно найти необходимую запчасть по причине отсутствия системы хранения. Как раз внедрение инструмента 5С очень целесообразно в слесарных мастерских. На одном предприятии однажды был такой случай: вышел из строя пневмоцилиндр, что привело к остановке всего процесса производства, в срочном порядке обыскали все слесарные мастерские и склад запчастей, но найти цилиндр не удалось. К производителю оборудования, чей цилиндр вышел из строя, срочно вылетел снабженец и в чемодане привез необходимую запчасть, производство при этом стояло порядка трех дней. Когда же внедрили 5С в слесарной мастерской, нашли несколько таких пневмоцилиндров.
Этап построения системы управления запасными частями самый затратный, но очень важный, в рамках которого определяется необходимый уровень запасов запчастей, разрабатывается номенклатура и правила управления запасными частями.
Важно понимать, что сам по себе учет простоев не повлечет за собой их сокращение, поэтому следующий этап — это система анализа и поиска первопричин простоев. Особое внимание на данном этапе нужно уделить обучению инженерно-технических работников (ИТР):
- методам краткосрочного и среднесрочного планирования,
- методам анализа простоев и поиску первопричин неисправности.
1. Возникновение и ликвидация простоев оборудования (пример)
На оборудование 1-го приоритета (согласно картографии) при простое свыше 1 часа начальником дежурной смены заполняется первый лист в новой форме отчета о длительной остановке. На оборудование 2-го приоритета — свыше 2 часов, остальное — свыше 3 часов.
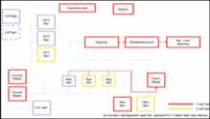
2. Решение о необходимости проведения анализа длительности и/или поиска первопричин поломки (пример)
Заполненные листы отчетов о длительных остановках ежедневно на утренней встрече по планированию ремонтов передаются директору технического департамента (или лицу, его замещающему), который принимает решение о необходимости проведения анализа длительности и/или поиска первопричин поломки, назначает ответственного за проведение анализа из ИТР тех. службы.
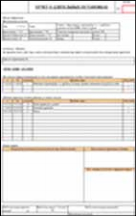
3. Проведение анализа длительности и/или поиска первопричин поломки (пример)
Ответственный за анализ поломки заполняет 2-ой лист отчета о длительной остановке — проводит непосредственно сам анализ, отправляет его на согласование директору технического департамента (ДТД). ДТД отправляет согласованный отчет генеральному директору, директорам департаментов, инженеру ППР.
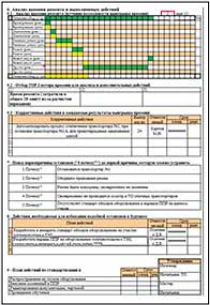
4. Контроль выполнения корректирующих мероприятий (пример)
Инженер ППР сводит согласованные мероприятия в реестр, контролирует статус выполнения, формирует еженедельный отчет.
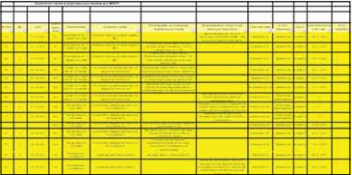
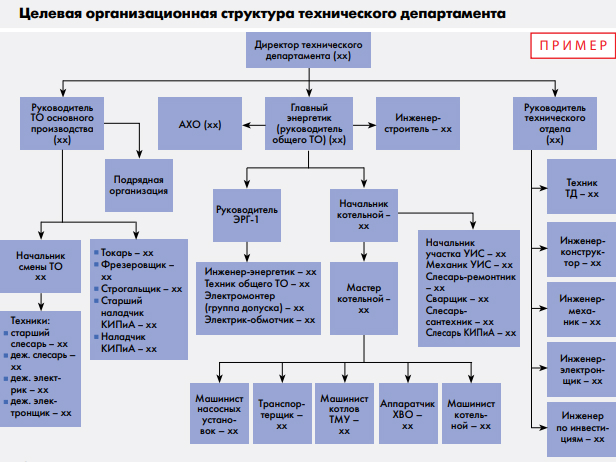
Основные направления организационного развития
- Формирование «штаба» ИТР, в обязанности которой входит еженедельный анализ показателей надежности оборудования, анализ длительных простоев, корректировка карт и плана ППР, контроль качества выполнения ППР, участие в устранении сложных поломок, разработка корректирующих мероприятий, отслеживание и комплектация склада з/ч.
- Разделение ТО по объектам: основное производство, инфраструктура.
При внедрении проекта ТРМ изменяется организационная структура технической службы. Суть изменений заключается в выделении инженерного блока и формировании дежурной службы в составе слесаря, электрика, электронщика и начальника. Функция инженерного блока – это еженедельный анализ показателей надежности оборудования, анализ длительных простоев, корректировка карт и плана ППР, контроль качества выполнения ППР, участие в устранении сложных поломок, разработка корректирующих мероприятий, отслеживание и комплектация склада запчастей. Функция дежурной службы – это выполнение текущих ремонтов и устранение внеплановых простоев.
К изменению оргструктуры можно привязать и изменение системы мотивации работников технической службы. КПЭ технической службы устанавливают показатели надежности оборудования.
В завершение хотелось бы сказать, что успех реализации проекта ТРМ, как и любых изменений на предприятии, зависит от двух основных вещей:
- Заинтересованность высшего руководства с активным вовлечением в процесс реализации проекта, как говорится, «слова назидают, а дела влекут»!
- Тотальный контроль за соблюдением процедур на этапе внедрения, для этого разрабатывается график контроля для всех уровней, включая высшее руководство.
Журнал Prostoev.NET № 1(14) 2018
Авторы: Юрий Стрежень (генеральный директор) & Виталий Соколов (управляющий партнер) ООО «Группа ПРАКТИКА»