Часть 1
Общение с разными специалистами, которые вовлечены в процесс планирования ТОиР, показывает, что вопросы организации снабжения необходимыми ТМЦ (товарно-материальными ценностями) занимают чуть ли не большую часть времени. Очевидно, что это обусловлено высокой стоимостью ТМЦ, так как на предприятиях может эксплуатироваться импортное оборудование, поддержание которого достаточно дорого. При этом вопросы снабжения ТМЦ затмевают вопросы планирования персонала, опять-таки потому, что у нас традиционно затраты на персонал очень низкие, и отсутствие необходимого количества людей становится важным лишь тогда, когда их становится так мало, что ремонтировать оборудование становится просто некому.
Часто службы снабжения рассматриваются как некий внутренний враг, который не привозит запчасти вовремя, постоянно просит каких-то заявок на год, да еще и помесячно. Во время таких заявочных кампаний большинство инженерного персонала дружно заходит в систему снабжения и составляет те самые заявки на запчасти и материалы.
Мы бы хотели немного приоткрыть тайну в организации «черного ящика» под названием «управление запасами» и рассмотреть ряд вопросов, на которые должна отвечать современная система управления запасами, обеспечивающая потребности служб ТОиР.
Основные проблемы, характерные для большинства традиционных организаций:
- ограничения по стоимости запасов на складе по ремонтной номенклатуре;
- закупками ТМЦ для ТОиР занимаются ОМТС, не ОГМ: цена прежде качества;
- большой объем пересортицы и малооборачиваемых ТМЦ на складе;
- несоблюдение сроков поставки;
- необходимость иметь фонд оборотных агрегатов и обоснование его состава и стоимости;
- сложность изменения плана закупок при изменении потребности в ТОиР;
- отсутствие адекватных нормативов расхода ТМЦ;
- данные о фактическом расходе за период не адекватны реальной потребности;
- слабый контроль фактического расхода ТМЦ.
Основные требования к системе МТС со стороны системы ТОиР
Основным требованием к процессу управления материальными запасами со стороны ТОиР является качественное обеспечение ТОиР необходимыми ТМЦ. Качественное обеспечение ТМЦ, с точки зрения ТОиР, характеризуется следующими параметрами:
- своевременностью обеспечения;
- полнотой обеспечения;
- соответствием характеристик ТМЦ предъявляемым требованиям.
Номенклатурный справочник
Первым обязательным условием для нормальной работы системы снабжения и интеграции ее с системой ТОиР является наличие номенклатурного справочника позиций. Именно этот справочник позволяет общаться на одном языке и минимизировать ошибки, связанные с неправильным описанием позиций на складе.
Номенклатурный справочник должен удовлетворять следующим условиям:
- полнота — каждая позиция справочника содержит перечень атрибутов, необходимых для ее однозначной идентификации;
- непротиворечивость — каждая позиция справочника содержит атрибуты, не противоречащие друг другу;
- идентифицируемость — каждая позиция справочника имеет уникальный код;
- отсутствие дублей — несмотря на многообразие кодов и наименований одной и той же номенклатурной позиции у различных поставщиков, номенклатурная позиция должна уникально идентифицироваться в номенклатурном справочнике.
Методы работы по созданию унифицированного номенклатурного справочника достаточно хорошо описаны в различных рекомендациях по построению системы снабжения. Номенклатура ТОиР составляет лишь долю от общей номенклатуры (сырья, материалов для производства, товаров для канцелярии и т.д.).
Существуют программные инструменты, позволяющие унифицировать справочник номенклатуры и управлять процессом поддержания этого справочника (например, отслеживать и удалять дубли, искать похожие названия одной позиции, вести номенклатуру аналогов для позиций, отслеживать правильность заполнения описания позиции, вести наборы описательных атрибутов по категориям запасов и т.д.).
При разработке номенклатурного справочника необходимо учитывать потребности пользователей в группировке и классификации позиций для более удобного поиска. Объем справочника ТМЦ даже для сравнительно небольших предприятий может составлять десятки тысяч позиций, а для промышленных гигантов и распределенных холдингов — до десятков миллионов.
Очевидно, что такой большой объем невозможно просматривать
для поиска нужных позиций, и все операции связаны с поиском по заранее определенным параметрам. Далее мы исходим из того, что справочник номенклатурных позиций есть, в нем описана большая часть номенклатуры, потребляемой ТОиР, и уже есть некая история расходования позиций для работ по ТОиР как минимум за 2—3 года.
Если этих данных нет, то никакие совершенные нормативы не позволят вам спрогнозировать потребление ТМЦ в ваших конкретных уникальных условиях организации работ.
Методы планирования запасов
Для того чтобы нужные запчасти и материалы попадали в нужное время и место, необходимо, чтобы кто-то запланировал это. Мы уже упомянули, что позиций могут быть десятки тысяч, и ожидать, что механик оформит заявку на каждый болт, нет оснований. Но как же заказать этот болт без заявки? Ответом на данный вопрос может служить использование разных методов планирования для разных категорий ТМЦ.
Наиболее популярными и общепризнанными методами планирования в ТОиР являются:
- метод планирования по точке дозаказа;
- метод планирования потребности в запчастях;
- метод планирования под заказ.
Метод планирования по точке дозаказа
Суть метода — определить уровень складских запасов, при достижении которого следует принимать меры по пополнению запасов (если общее количество наличных запасов вместе с уже подтвержденными заказами оказывается ниже этого уровня). В этом случае нет необходимости в планировании работ, пополнение запасов происходит автоматически при снижении до определенного уровня. Это лучше всего подходит для постоянно потребляемых запасов.
Как только уровень запаса опускается до определенной точки (так называемой «точки дозаказа»), запускается процедура в системе снабжения, которая и обеспечивает наличие этой позиции на складе без участия служб ТОиР.
Для этого метода также характерно понятие «страхового запаса», т.е. объем позиций, который может быть использован в случае изменения скорости расходования ТМЦ или увеличения срока поставки из-за каких-то задержек. Этот запас не нужно путать с аварийным запасом, речь о котором пойдет ниже.
Итак, мы имеем следующие параметры:
- точка дозаказа — уровень запасов, при достижении которого формируется потребность в новом заказе на пополнение запасов;
- время доставки — время (в днях) от момента формирования потребности в пополнении запасов до момента поступления запасов на склад. Определяется длительностью цикла поставки данных запасов;
- страховой запас — минимальный неснижаемый уровень запасов на складе.
Данный метод планирования предполагает, что за время доставки уровень запасов не опустится ниже уровня страхового запаса. На основании страхового запаса рассчитывается точка дозаказа:
Nд = (Nс × Tп) + Nз
где:
Nд — уровень точки дозаказа,
Nс — среднестатистический суточный уровень расхода запасов,
Tп — время доставки,
Nз — уровень страхового запаса; - заказываемое количество — количество ТМЦ, заказываемых при достижении уровня точки дозаказа. При определении заказываемого количества рекомендуется использовать размер оптимальной партии поставки. Оптимальный размер партии поставки определяет такое количество заказываемого материала, при котором стоимость получения и хранения единицы материала является (с учетом всех факторов) минимальной.
Данный размер рассчитывается по формуле:
EOQ = √(2×DXK)/H)
где:
EOQ — оптимальный размер партии поставки,
D — годовая потребность в запасах,
K — стоимость организации заказа (погрузка, разгрузка, упаковка, транспортные расходы),
H — стоимость хранения 1 единицы запасов в течение года (налоги, зарплата складского персонала, обслуживание оборудования).
Метод планирования потребности в запчастях
Данный метод основывается на ранее со ставленном плане выполнения ремонтов, а также на прогнозируемых ремонтах. Планирование осуществляется «котловым» мето дом, без привязки к конкретным работам. При использовании этого метода требуется точная информация о наличии доступных остатков запчастей и материалов, а также достоверное нормирование расходов запчастей на проводимые работы, в противном случает будет невозможно рассчитать требуемое количество.
Рекомендуемый горизонт планирования со ставляет до 3 месяцев, при этом первый месяц составляют «твердые» заказы (если длительность цикла поставки превышает один месяц, то горизонт планирования «твердых» заказов должен быть увеличен), остальное составляют «прогнозируемые» заказы, которые могут быть изменены при дальнейшем перепланировании.
Такой метод наиболее подходит для дискретно потребляемых запасов. Он характеризуется следующими параметрами:
- график ремонтов — календарный график планируемых и прогнозируемых видов работ;
- техкарта — список запчастей и материалов (а также их количество), необходимых для выполнения запланированных/спрогнозированных работ. Техкарты должны быть сформированы для каждой запланированной/спрогнозированной работы;
- текущий уровень складских запасов — текущее доступное количество запчастей и материалов (необходимых для выполнения запланированных/спрогнозированных работ и определенных в техкартах) на складе;
- длительность цикла поставки — время (в днях), необходимое поставщику на поставку запасов от момента формирования запроса на поставку, плюс время, необходимое для внутреннего согласования запроса на поставку (проведение тендеров, внутреннее согласование заявки);
- кратность партии поставки — значения, определяющие количество минимальной/максимальной поставки. Рекомендуется использовать оптимальный размер партии поставки.
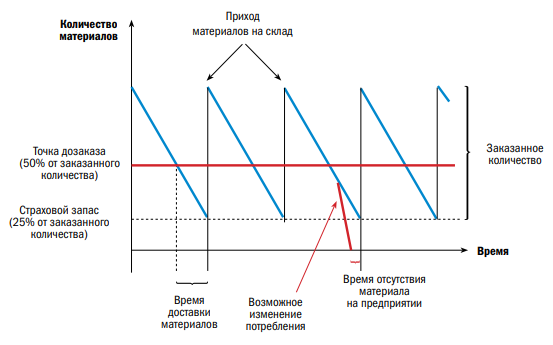
Пример расчета по точке дозаказа
Исходные условия для оптимизации размера заказа:
- среднестатистическая годовая потребность в подшипниках N составляет D = 1 000 шт.
- среднестатистическая суточная потребность:
Nс = 1000 / 365 = 2.75 - затраты на размещение одного заказа поставки К = 280 руб. затраты на хранение подшипника H = 35 руб. на единицу хранения в год
- время выполнения заказа TП = 34 календарных дня
- цена одного подшипника C = 586 руб.
- уровень страхового запаса NЗ = 9 шт.
Размер заказа:
QOPT = √(2 × 1000 × 280) / 35 = 126.5
Точка дозаказа:
Nд = (2.75 × 34) + 9 = 102.5
Стратегия управления запасами подшипника N — при снижении уровня запаса до 103 шт. необходимо заказать 127 подшипников указанной марки.
Допущения:
- потребность в подшипниках известна и равномерно распределена по всему периоду;
- время выполнения заказа поставки неизменно;
- цена на подшипники N постоянна в рассматриваемом периоде;
- затраты на хранение подшипников рассчитываются по среднему уровню запаса.
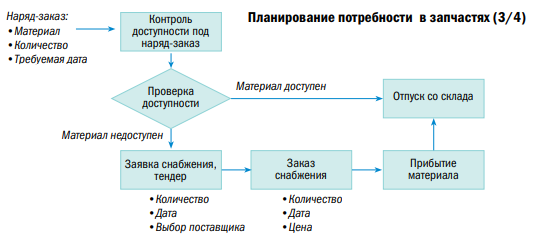
Пример расчета валовой потребности в запчастях
Если кратность поставки запчасти составляет 30 шт., то будет сформирован заказ поставки на 30 шт., который, с учетом длительности цикла поставки, должен будет поступить к шестому периоду.
Период | Валовая потребность в запчасти | Поставка | Доступно | Результат | Чистая потребность в запчасти |
1 | 0 | 0 | 23 | 23 | 0 |
2 | -20 | 0 | 23 | 3 | 0 |
3 | 0 | 30 | 3 | 33 | 0 |
4 | -25 | 0 | 33 | 8 | 0 |
5 | 0 | 0 | 8 | 8 | 0 |
6 | 15 | 0 | 8 | -7 | 7 |
7 | 12 | 0 | 0 | -12 | 12 |
8 | 0 | 0 | 0 | 0 | 0 |
ВСЕГО | 72 |
Данный метод позволяет обеспечивать потребность в ТМЦ под работы, которые выполняются достаточно регулярно, с небольшими отклонениями в сроках и объемах. Для удобства планирования таких работ рекомендуется включить в техкарту набор ТМЦ, который будет автоматически формироваться в заявку при планировании соответствующей работы. При этом часть ТМЦ, которая потребляется регулярно и имеет небольшую стоимость, можно не включать в техкарту, а планировать по точке дозаказа.
При создании шаблонов работ на ТОиР (нормативов, техкарт, типовых объемов работ и т.д.) необходимо найти баланс между детализацией номенклатуры ТМЦ в таком шаблоне и трудоемкостью поддержания этой информации при изменениях и в повседневной работе. Представьте себе ситуацию, когда по такому детальному шаблону будет выдан заказ на работы, и мастер на складе будет выписывать по 0,012 л керосина, чтобы протереть контакты. Соответственно, по факту потребления этого количества надо будет списать его на этот конкретный заказ и потом провести соответствующие транзакции в бухгалтерии.
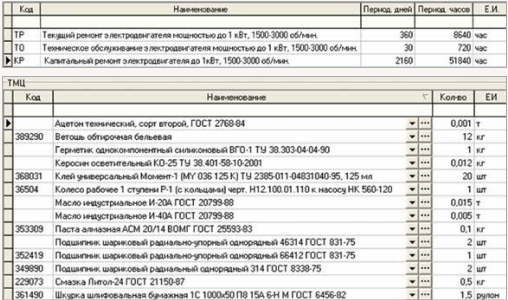
Рекомендуем включать в шаблон на работы те позиции, которые потребляются менее регулярно, чем смазки, обтирочные материалы. Набор этих ТМЦ должен включать в себя достаточно значимые позиции, но их реальное использование зависит от конкретного технического состояния оборудования, на которое они планируются. При этом наличие в шаблоне избыточных позиций позволит механикам более гибко выбирать их из заранее определенного списка. Многие системы АСУ ТОиР позволяют «вычеркнуть» из заказа те позиции, которые в данном ремонте не нужны.
Метод планирования под заказ
Данный метод основывается на формировании заказа поставки запчастей и материалов для конкретного спланированного наряд-заказа. Горизонт планирования в этом случае не может быть меньше максимальной длительности цикла поставки запчастей или материалов.
Данный метод наиболее подходит для дискретно потребляемых запасов. Он позволяет в максимальной степени связать конкретную работу по ТОиР с той номенклатурой ТМЦ, которая нужна именно под этот заказ.
Очень часто при принятии решения о введении системы заказов на все работы ТОиР руководство требует, чтобы все ТМЦ также проходили через такие заказы. Но мы уже отметили, что такой подход очень трудоемкий. Так же, как в методе «валового» планирования ТМЦ под «валовые» заказы, в случае единичного заказа следует в первую очередь заказывать наиболее дорогие позиции.
Продолжение следует
В следующем номере мы обсудим различные методы категоризации ТМЦ и разделение номенклатуры по разным методам планирования ТМЦ, а также расскажем об особенностях формирования аварийного
запаса ТМЦ.
Дмитрий Скворцов, директор по развитию ООО «Простоев.НЕТ»
Журнал Prostoev.NET № 3(4) 2016