Уровень компетентности ремонтной службы предприятия, квалификации ее специалистов во многом определяется отношением к смазочным системам и, соответственно, их состоянием.
Смазочные системы имеют индивидуальные особенности, изучение которых происходит постепенно (от события к событию, от отказа к отказу), полученный опыт накапливается медленно, приводя к возникновению внештатных ситуаций, повторения которых следует избегать.
Эксплуатация смазочных систем основана на простых правилах, о необходимости выполнения которых предлагается напомнить в данной работе, рассмотрев некоторые нетипичные случаи, в том числе связанные с ошибками в принятии решений при нестабильном режиме работы предприятия.
Термины и определения
Смазка – действие смазочного материала, в результате которого между двумя поверхностями уменьшается сила трения и (или) интенсивность изнашивания.
Смазывание – подведение смазочного материала к поверхностям трения.
Смазочный материал – материал, вводимый на поверхности трения для уменьшения силы трения и (или) интенсивности изнашивания.
Смазочная система – совокупность устройств, обеспечивающих подачу смазочного материала к поверхностям трения, а также его возврат в смазочный бак.
Задачи смазывания: снижение коэффициента трения между двумя контактирующими, трущимися поверхностями за счет их разделения смазочным материалом; уменьшение износа; защита поверхностей трения от коррозии; отвод тепла и продуктов износа из зоны трения.
Эти задачи связаны между собой, невыполнение одной из них приводит к невыполнению другой. Например, если не выполняется задача снижения коэффициента трения, увеличивается износ и происходит повышенное выделение тепла в зоне контакта. Задача отвода продуктов износа из зоны контакта эффективно решается только при наличии системы смазывания жидким маслом.
Трение является одним из эксплуатационных факторов воздействия на детали механического оборудования, что проявляется в виде механического износа – окислительного, абразивного, усталостного. Практически во всех расчетах сила трения Fтр учитывается значением коэффициента трения fтр, относительно действующей нагрузки N:
Fтр = fтр×N.
Минимальное значение коэффициент трения (0,001-0,003) отмечается при жидкостном трении, при толщине масляной пленки 5 мкм. Граничное трение приводит к увеличению значений в десять раз (0,01-0,03). Сухое трение (сталь по стали без смазки) – 0,15. При схватывании контактирующих поверхностей коэффициент трения увеличивается до 1,0-2,0.
Запас мощности современных двигателей в 10-20% позволяет работать и без смазки, но износ поверхностей при этом становится критическим фактором, ограничивающим срок службы деталей, в частности подшипников.
Оценить значение коэффициента трения при работе механизма можно лишь при проведении точных измерений токовых характеристик. Однако такая возможность также появляется при свободном выбеге. Для электродвигателя, вентилятора, дымососа, эксгаустера, насоса и др. представление механизма в виде одномассовой расчетной модели позволяет, используя уравнения Лагранжа 2-го рода, получить зависимость между временем выбега и коэффициентом трения:
J×ε = Mтр; ω = ε×t/2.
Если
J ≈ 0,5×m×R2 ; Mтр = r×m×g×fтр;
тогда
fтр = (0,25×m×R2 × ω)/(r×m×g×t);
или
fтр = (0,25×R2 × ω)/(r×g×t);
где J – момент инерции ротора, кг×м2 ; ε – угловое ускорение, с-2; ω – угловая скорость, с-1; t – время свободного выбега, с; Mтр – момент трения, Н×м; m – масса ротора, кг; r – радиус трения в подшипнике, м; R – радиус ротора, м; g – ускорение свободного падения, м/с2.
Пример 1. Свободный выбег двигателя мощностью 1,2 МВт с частотой вращения 960 об/мин при приемке после ремонта составил t1 = 60 с. Известны параметры: r = 96 мм, R = 290 мм. Следовательно, коэффициент трения составляет:
fтр1 = (0,25×0,292 ×100,5)/(0,096×9,81×60) = 0,037.
После проведения дополнительных работ по выверке положения подшипников и смазывания выбег составил t2 = 420 с, а коэффициент трения:
fтр2 = (0,25×0,292 × 100,5)/(0,096×9,81×420) = 0,006.
Таким образом, в результате проведенных работ коэффициент трения снизился, что позволило начать длительную эксплуатацию механизма.
Пластичные смазки
Пластичные смазки и жидкие масла по своим достоинствам дополняют друг друга. Однако некоторые, казалось бы, преимущества пластичных смазок без учета многочисленных факторов внешнего воздействия приводят к отказам.
Использование централизованных петлевых или конечных систем подачи пластичной смазки в обычных условиях обеспечивает стабильную подачу смазочного материала к узлам трения. Мазепроводы данных систем иногда располагают рядом с паропроводящими магистралями, нагревательными печами, трубопроводами подачи горячей воды и др., чтобы исключить замерзание пластичной смазки в зимний период. Остановка движения пластичной смазки при простое приводит к снижению подвижности и образованию пробок из окисленного материала.
Расположение мазепровода рядом с нагревательной печью прокатного стана является традиционным решением. Однако в случае недельного или двухнедельного простоя системы смазывания отключаются, а нагревательные печи переводят на работу при пониженной температуре. Локальный нагрев мазепроводов при неподвижной пластичной смазке приводит к ее частичному коксованию, что выражается в повышенном сопротивлении потоку.
Система управления после простоя работает в обычном режиме периодического включения. Давление в магистрали при этом увеличивается до уровня срабатывания электроконтактного манометра, а смазочный материал в узел трения поступает в меньшем объеме. Масляное голодание обнаруживается через некоторый промежуток времени, приводя к необходимости замены подшипников на всем участке транспортирующих рольгангов, оставшемся без смазки.
Остановка оборудования снижает его работоспособность, поэтому:
- необходимо периодически включать систему смазывания при простое и наблюдать за поступлением свежей смазки и выходом старой из узла трения;
- после включения системы следует контролировать работу питателей по их одновременному перемещению.
Оптимальной является постоянная подача смазочного материала с малым расходом, решаемая применением автоматического лубрикатора. Здесь газогенерирующий картридж создает в рабочей камере устройства напор инертного газа, который толкает поршень, постепенно выдавливая смазку. Однако и в этом случае следует учитывать закономерности движения смазочного материала в подшипниковом узле.
Например, перемещаясь из зоны подачи и проходя через тела качения, структура смазочного материала меняется (рис. 1). Следовательно, через несколько лет эксплуатации подшипниковые узлы необходимо очищать от старой, отработанной пластичной смазки.
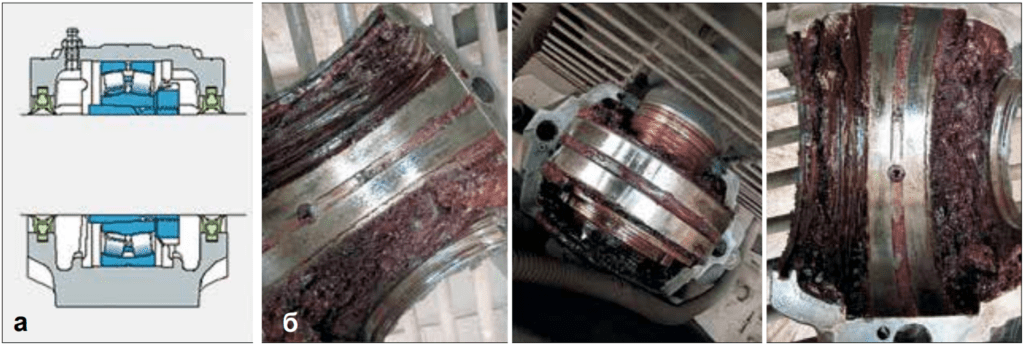
Если старый смазочный материал не выходит из подшипникового узла, он накапливается там, создавая сопротивление поступлению свежего в зону трения. Существующие свободные объемы постепенно заполняются окисленной пластичной смазкой, накапливающей продукты износа (рис. 2), коэффициент трения увеличивается, приводя в конечном итоге к заклиниванию.
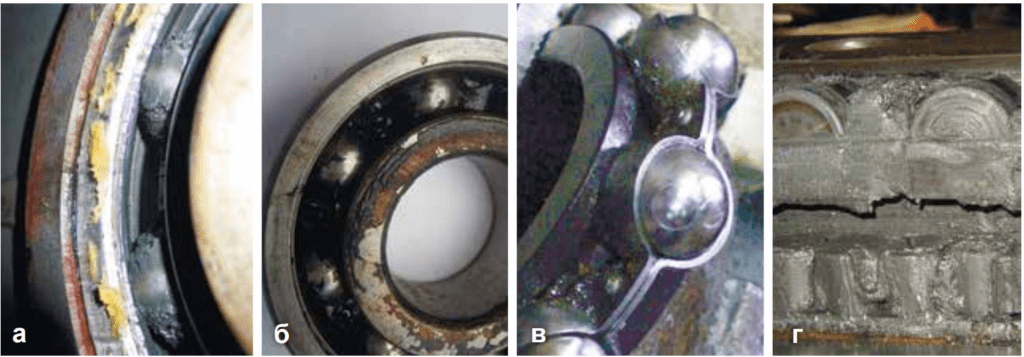
При очистке подшипника следует помнить, что смазка располагается не только в подшипнике, откуда она уходит при вращении. Именно карманы, заполненные пластичной смазкой, создают условия для постоянного поступления смазочного материала в подшипник. Добиться этого непросто даже в однотипных подшипниковых узлах.
Так, два одинаковых двигателя мощностью 250 кВт с частотой вращения 2980 об/мин смазываются с различным периодом. Один – каждые 6 месяцев, второй – по потребности, каждые 3 месяца. Причина – различная самоорганизация движения смазочного материала в подшипниковом узле (вопрос, так и не получивший окончательного решения).
В некоторых случаях на качество смазывания влияют внешние причины.
Пример 2. Если при монтаже подшипника не были учтены тепловые расширения, при работе появляется радиальный зазор, из-за дополнительного сопротивления подшипник греется. Износ роликов происходит со стороны больших диаметров. Идет шелушение поверхностного слоя и осповидное выкрашивание. Проводится дополнительное смазывание, температура временно снижается. Ситуация повторяется многократно. Подшипник заполняется окисленным смазочным материалом, начинается износ сепаратора в виде шелушения. Увеличивается момент сопротивления, подшипник нагревает вал, происходит смещение по оси и сколы буртов. Замыкается зазор – увеличивается температура, внутреннее кольцо расширяется и лопается. Далее – заклинивание и проворот внутреннего кольца (рис. 3).
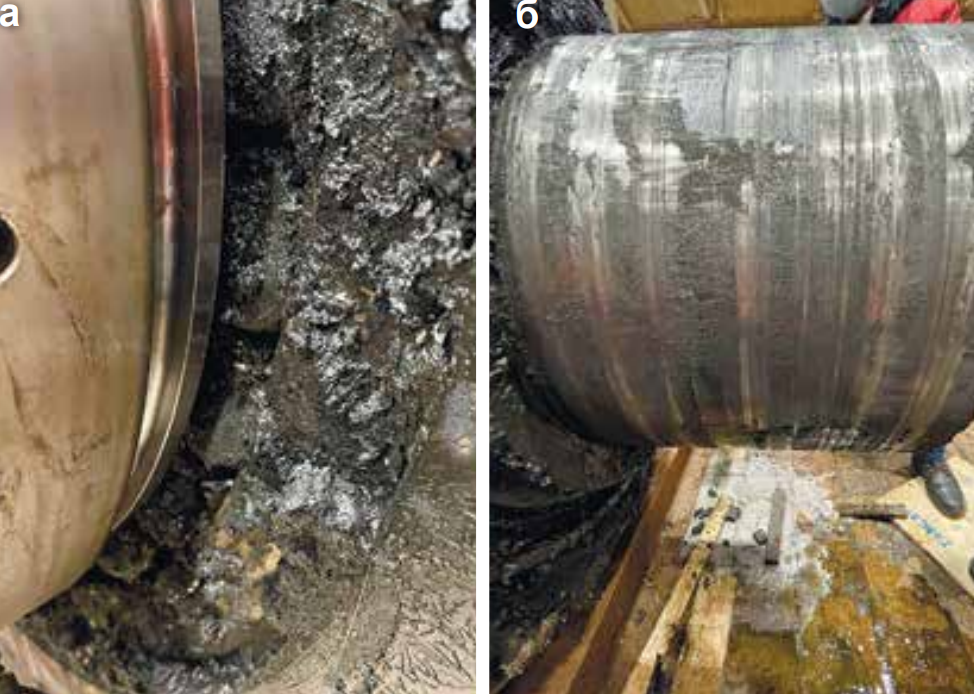
Пример 3. В случае косых резов газорезки МНЛЗ внешним воздействием, после семи лет работы, стало засорение внутренней полости водоохлаждаемых балок. Повысилась температура в рабочей зоне механизма и сократился срок службы пластичной смазки. Замены подшипников пришлось осуществлять каждые две недели.
Замеры температуры в рабочей зоне показали значения – 85-188 °С. Согласно данным фирмы SKF, минеральное масло сохраняет свои свойства в течение 30 лет при температуре 30 °С, а повышение температуры на каждые 10 °С приводит к двойному увеличению скорости окисления масла и снижению срока его службы вдвое. Следовательно, зависимость геометрическая: 30 °С – 30 лет; 40 °С – 15 лет; 50 °С – 7,5 года; 60 °С – 3,75 года; 70 °С – 1,87 года; 80 °С – 0,94 года; 90 °С – 0,47 года; 100°С – 0,24 года; 110 °С – 0,12 года; 120 °С – 0,053 года; 130 °С – 0,026 года (9,5 суток).
Это подтвердилось и на практике (рис. 4). При высокой температуре происходит ускоренное старение, интенсивное маслоотделение и отвердение смазочного материала, что приводит к разрушению одного из подшипников и косому резу.
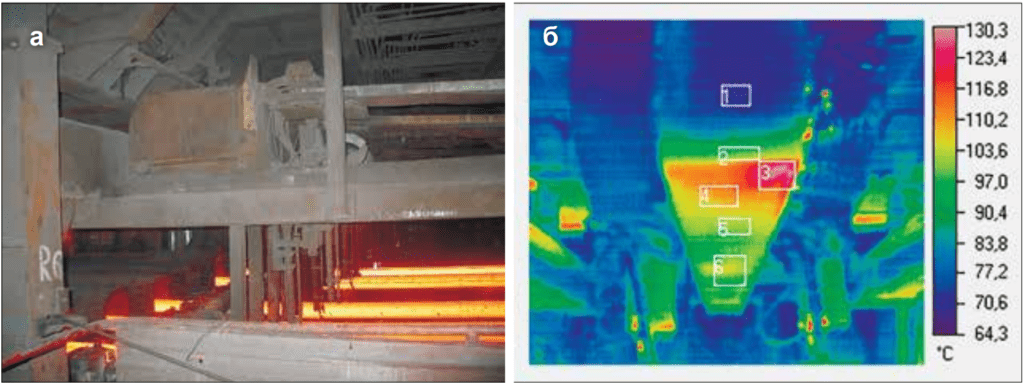
Влияние повышенной температуры для металлургических машин – обычный фактор внешнего воздействия. Этот фактор часто взаимодействует с иными постепенными изменениями.
Пример 4. Поворотная эркерная тарелка смонтирована в нижней части корпуса печи, удерживает кварцевый песок в выпускном отверстии и открывает эркер при выпуске стали. Для поворота используется рычажный механизм с приводом от гидроцилиндра. С начала эксплуатации механизм работал без отказов, но через восемь лет начались частые отказы. Причина заклинивания – закоксованность смазочного материала на вертикальном валу крепления упора эркера. Использование альтернативной смазки не привело к существенным изменениям.
Частые простои печи по причине выхода из строя механизма открытия упора эркера свидетельствуют об изменениях во взаимодействии элементов механизма – консольное нагружение приводит к деформации и выдавливанию смазки из зоны трения, что создает условия для накопления в полостях подшипников смазочного материала, его коксования с последующим заклиниванием.
Внешним воздействием также может быть влияние магнитных полей, приводящее к накоплению металлических продуктов износа в смазке и дальнейшему ускоренному абразивному износу, попадание воды в подшипник и др.
Своевременная подача смазочного материала может привести к улучшению технического состояния подшипника, что диагностируется средствами вибрационного контроля.
Например, подшипники электродвигателя, установленного в 1996 году, работали без замечаний десять лет. Смазывание проводилось с периодом в три месяца. В июне 2006 года появился нехарактерный шум, повысились значения виброускорения. Было принято решение выполнить смазывание с добавлением геомодификатора трения. Через пять дней значения виброускорения снизились в три раза. Следующее отклонение в работе данной пары подшипников зафиксировано в 2020 году – в результате пылевой бури в подшипник попали абразивные частицы, что потребовало увеличения количества смазочного материала для очистки зоны контакта тел качения и беговых дорожек.
На основе практики использования не рекомендуется проводить смешивание пластичных смазочных материалов различных марок, даже изготовленных на одной основе. Последствия могут быть непредсказуемыми.
Так, при монтаже подшипника вала генератора не была проведена расконсервация подшипника, и свежая смазка, смешавшись с внутренним содержимым, дала нерастворимые осадки (рис. 5). В результате генератор механизма подъема экскаватора с новым передним подшипником 3632 отправлен в ремонт по причине повышенного нагрева («задымил»).
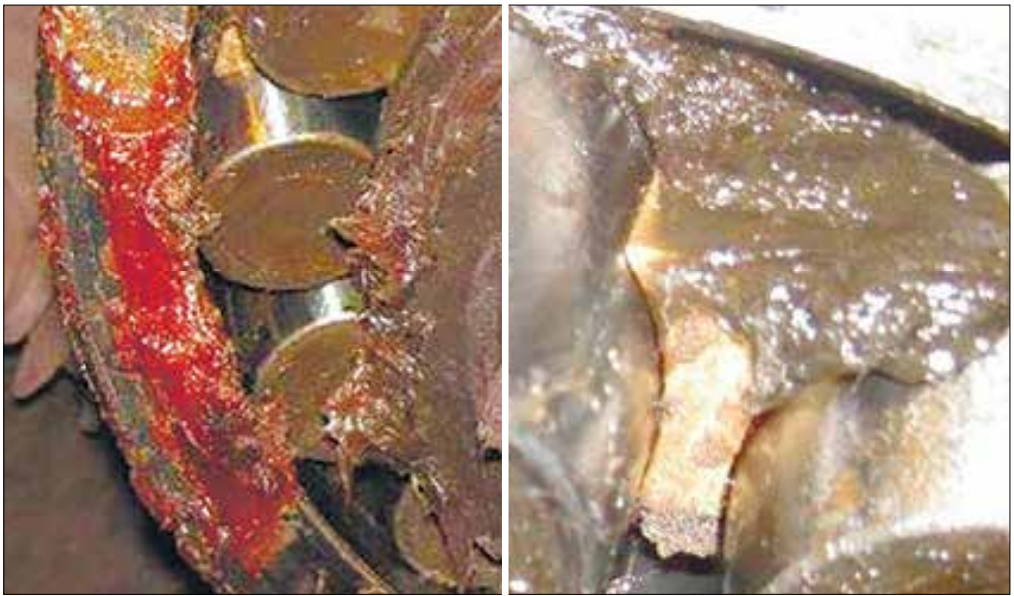
Следует помнить, что цвет пластичной смазки может меняться от светло-желтого до темно-коричневого Соответствие цвета свежего масла – обязательное условие длительной работы подшипника.
Жидкие масла
Проблемы с масляным голоданием при смазывании жидким маслом накапливаются постепенно, а проявляются внезапно. Так, например, облитерация (зарастание каналов подачи жидкого масла лаковыми отложениями) приводит к снижению количества подаваемого масла, масляному голоданию, разрушению сепаратора, заклиниванию и проворачиванию внутреннего кольца подшипника по валу (рис. 6). Увеличение диаметра канала подачи, как временное решение, приводит к снижению давления. При этом скорость масла должна быть достаточной, чтобы часть его проникала через завихрения, образующиеся вокруг вращающегося подшипника.
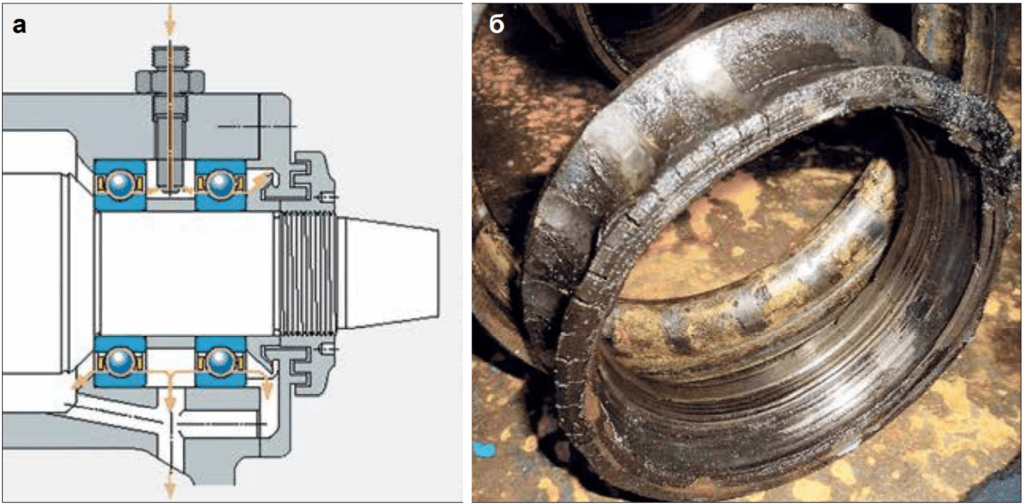
В настоящее время смазочные системы «масло – воздух», «масло – пленка» являются наиболее эффективными и экономными при правильной настройке и эксплуатации. Надежность точно отрегулированной системы масловоздушного смазывания может быть велика настолько, что соответствующая служба забывает о ее устройстве. Отсутствие отказов не позволяет накопить опыт ремонта.
Иногда причиной отказов становится изменение или неверно выбранное положение форсунок. Так, при осмотре комбинированного редуктора прокатной клети непрерывного прокатного стана после аварийной остановки выявлены следы износа муфты (рис. 7), служащей для переключения привода клети (горизонтального и вертикального). Присутствуют накопленные продукты отработанного смазочного материала и износ зубьев муфты вследствие нарушения положения форсунок, подающих масло в зону трения.
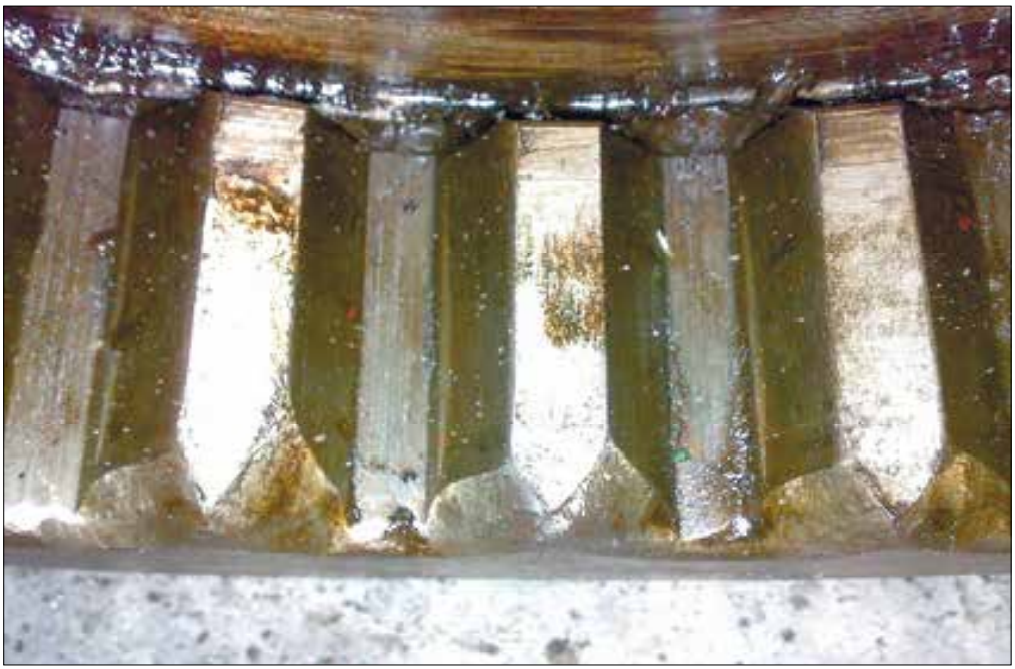
Кроме того, существующее в механике правило «лучшее враг хорошего» указывает, что, если используемое масло выполняет свои функции, не следует стремиться получить значительный выигрыш при переходе на самое лучшее масло. Следует учитывать ряд сопутствующих факторов.
Пример 5. Жидкое масло ХА-30 отработало в составе винтовой компрессорной установки нормативные 20 тысяч часов. Улучшение экономической ситуации позволило при замене перейти на аналогичное Mobil Arctic 300. Условия замены были согласованы с предприятием-поставщиком после консультации с заводом-изготовителем.
Прекрасные свойства масел фирмы Mobil, не вызывающие сомнения, после замены были дополнены наблюдением – масло Mobil Arctic 300 обладает чудесными моющими свойствами. Для маслозаполненного двухроторного винтового компрессора это привело к перемещению окисленных смазочных материалов из полостей маслоотделителя во входной фильтр, который засорился через один час работы. Замены фильтров привели к исчерпанию их запаса, а в дальнейшем – к износу подшипниковых узлов (рис. 8) роторов компрессора, вращающихся с частотой 3000 об/мин и 2400 об/мин.
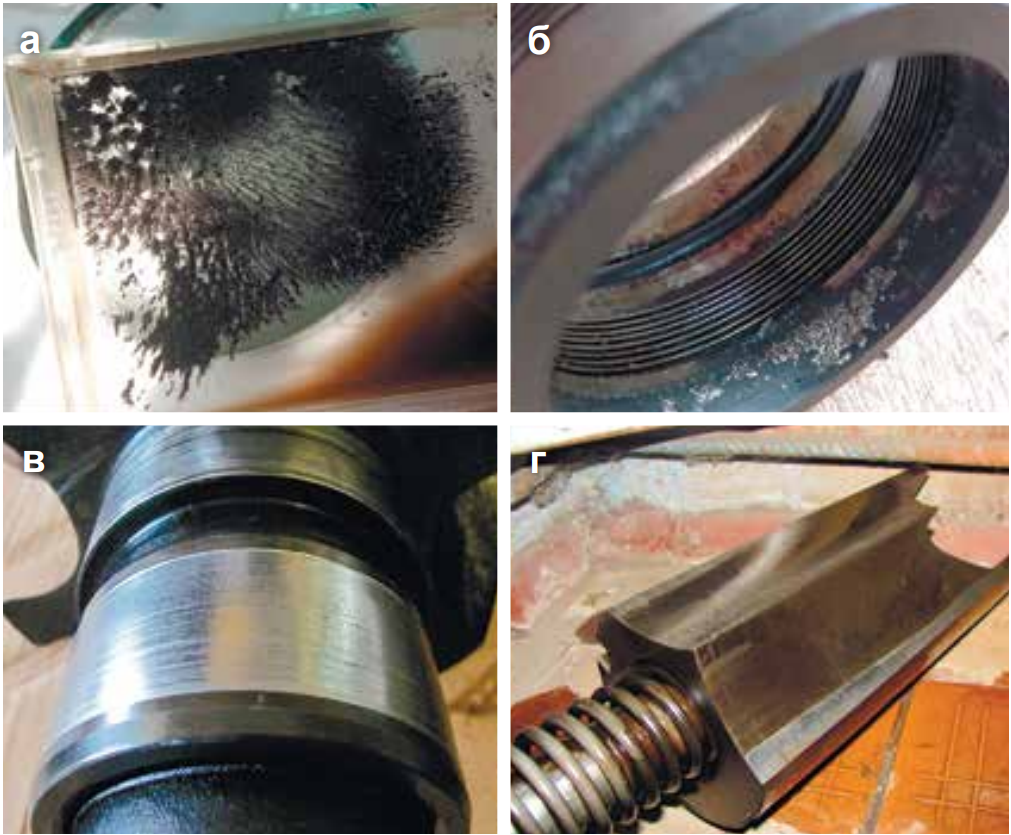
Обязательной перед заменой масла должна быть операция по промывке смазочной системы с последующим контролем, поскольку остатки промывочной жидкости могут привести к изменению свойств нового масла. Это весьма актуально, учитывая большие объемы смазочного материала и число элементов систем жидкой смазки современных прокатных станов.
Пример 6. Смазывание подшипников скольжения быстроходного вала редуктора ЦОС-120 привода прокатных клетей осуществлялось с использованием жидкого масла ТНК-510. При замене масло ТНК-510 из системы смазывания редуктора и шестеренной клети было слито, система промыта и залито масло Shell Morlina S2 BA 100, имеющее практически аналогичные характеристики. После этого последовательно, с интервалом в два месяца, дважды проведена замена подшипников быстроходного вала редуктора ЦОС-120 по причине обнаружения начальной стадии наволакивания баббита подшипника от муфты.
Насколько данные отказы могут быть следствием замены масла? Длительная эксплуатация масла ТНК-510 приводит к увеличению вязкости. Замена на Shell Morlina S2 BA 100 снижает несущую способность смазочного слоя. В характеристике Shell Morlina S2 BA 100 указывалось, что масло отвечает жестким требованиям для чистовых прокатных станов, работающих без кантовки, при эксплуатации подшипников на высоких скоростях. Работа подшипников быстроходного вала редуктора ЦОС120 происходит при низкой скорости 3,5 м/с и ударном воздействии. В этом случае более подходит масло, рекомендуемое для тяжелонагруженных редукторов, работающих с ударными нагрузками при прокатке.
В результате осмотра подшипников скольжения установлено (рис. 9) увеличение пятна контакта до 100-140°, наличие «зеркальной» изношенной поверхности, наволакивание и выкрашивание баббита. Это может быть следствием длительной эксплуатации или ошибок при монтаже.
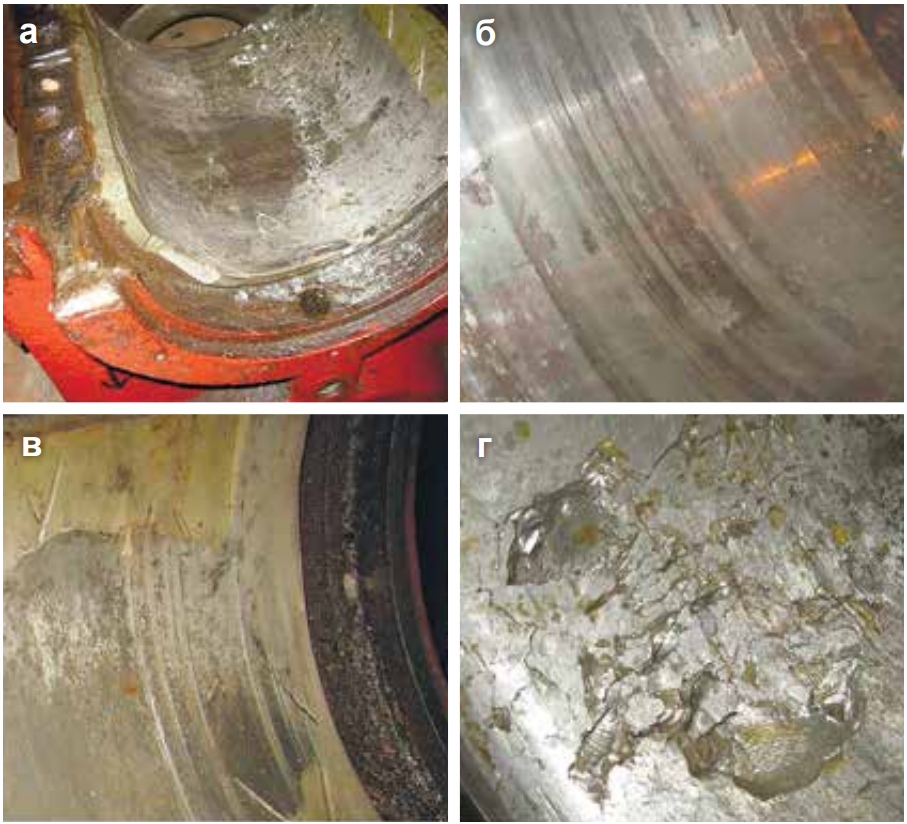
Выполненный анализ пробы масла показал соответствие технических характеристик. При этом были исследованы образцы масла И-20 (использованного при промывке гидравлической системы) и Shell Morlina S2 BA 100 (после начала эксплуатации) с целью определения класса чистоты и состава механических примесей в рабочей жидкости. Уровень загрязнения образца масла И-20 соответствует 10 классу (рис. 10а). Результаты анализа Shell Morlina S2 BA 100 показали, что масло имеет высокую степень загрязнения (вне класса). После фильтрации 100 мл пробы вся поверхность аналитической мембраны покрыта слоем загрязнений темного цвета (рис. 10б). В составе загрязнений обнаружены прозрачные кристаллические частицы, частицы черного цвета, частицы металла, окалины, силикаты, волокна. Это еще раз подтверждает прекрасные моющие свойства импортных масел, что следует учитывать при замене и начале эксплуатации.
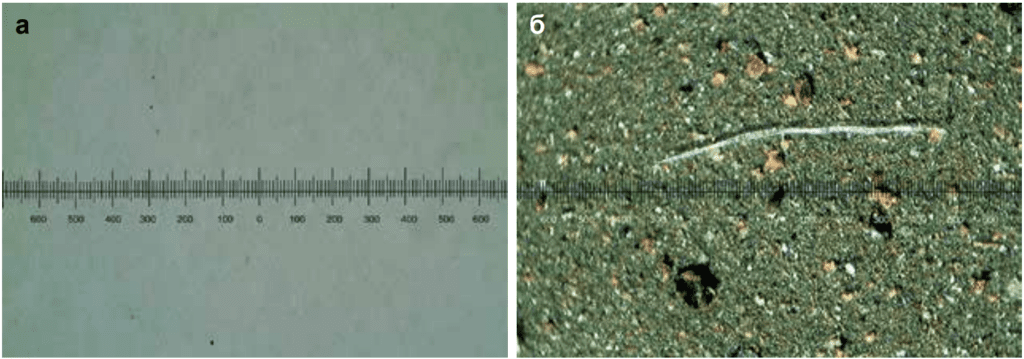
Дополнительно необходимо иметь в виду возможность засорения отверстий, подводящих смазку к подшипникам. Так, смазывание подшипников редуктора механизма подъема литейного крана осуществляется маслом, разбрызгиваемым зубчатой передачей и стекающим по внутренним стенкам крышки редуктора. Засорение отверстия, показанное на рис. 11, приводит к масляному голоданию подшипника и износу сепаратора. Услышать слабый металлический звон, сопровождающий это явление, достаточно сложно, следствие – внеплановая замена подшипника. Альтернативное действие – прочистка отверстия.
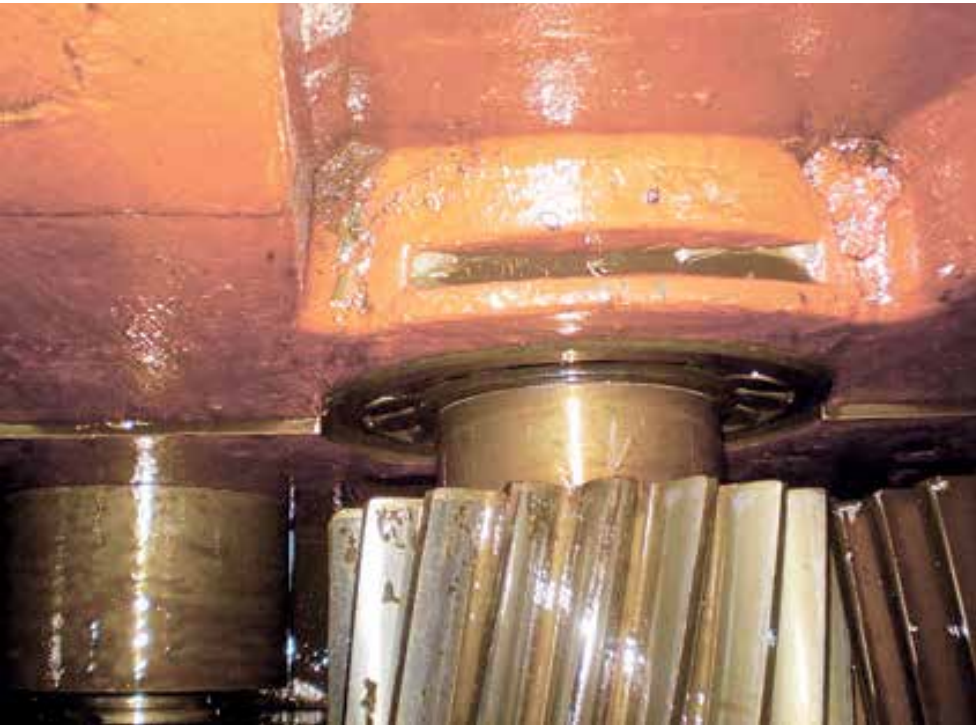
Таким образом, обеспечение надлежащего режима смазывания узлов трения создает благоприятные условия эксплуатации оборудования, что способствует повышению надежности и увеличению срока его службы. При этом эффективная организация смазочного хозяйства требует понимания физических процессов, протекающих в оборудовании, знания свойств масел и смазок, а также учета конкретных условий, в которых осуществляется эксплуатация. В то же время игнорирование указанных требований приводит к самым неблагоприятным, хотя нередко и отдаленным по времени, последствиям.
Здесь уместно будет напомнить правило 1-10-100, которое гласит, что каждый рубль, сэкономленный на техническом обслуживании, впоследствии заберет 10 на ремонте или 100 в случае аварии. Другими словами, экономия на смазывании повлечет необходимость замены подшипника, а в случае его заклинивания приведет к повышенному износу посадочных поверхностей или разрушению базовых деталей, что потребует уже значительно больших затрат для восстановления работоспособности оборудования.
Журнал Prostoev.NET № 1(30) 2022
Н.Ю. ГРИТЧЕНКО, Донецкий металлургический завод
В.А. СИДОРОВ, Донецкий национальный технический университет