Реорганизация ремонтных и диагностических подразделений предприятий, внедрение информационной системы ремонта, нормативной базы позволили качественно изменить состояние управления основными фондами.
«СИБУР Холдинг» — достаточно большая компания, одна из ведущих в нефтехимии и химии в России. В нее входит до 30 разных предприятий, основная часть из которых связана по передаче продуктов в технологической цепочке.
В 2006 году это все начиналось с некой озабоченности менеджмента холдинга:
«А на что мы тратим деньги?» Было понимание, что, по ощущениям, этих денег тратится много, не очень понятно, на что конкретно они расходуются, какое состояние фондов мы за эти деньги получаем, как оно будет меняться в перспективе, достаточно этих денег или недостаточно. В общем, хотели получить некую прозрачность и, возможно, какой-то инструмент для оценки эффективности этих затрат.
Было проведено обследование состояния всех предприятий холдинга, они пришли в него из различных отраслей промышленности: химии, нефтехимии, со сложившейся историей обслуживания, уровнем обслуживания оборудования, со своими практиками, часто даже со своими отдельными процессами. И когда провели это экспресс-обследование, стало понятно, что деньги тратятся неэффективно. Насколько неэффективно — непонятно, потому что инструментов для оценки этой эффективности и понимания, что такое эффективность расходования средств на содержание основных фондов, — нет. Нет статистики, никто не собирает данные, которые можно подвергнуть анализу и получить какую-то достоверную картину состояния средств или эффективности их расходования.
Стало понятно, что с этим надо что-то делать, если хотим как-то развиваться. Отсюда родилась корпоративная программа «Внедрение передовых методов поддержания основных фондов».
Концепции этой программы разрабатывались вместе с внешними консультантами. На тот момент у заводов в холдинге понимания того, как это все начать, как реализовать и как построить процесс, не было.
Совместно был выработан такой подход. Определились, что для приоритетного развития нужно выделить четыре направления, которые позволят сдвинуть процесс с мертвой точки и придать положительную динамику развитию самой системы ТОиР. Внедрение информационной системы ремонтов позволит накапливать статистику в нужном формате, годную для анализа и в дальнейшем для принятия каких-то решений. Для информационной системы нужна нормативная база, которую тоже нужно делать. Для того чтобы эффективно планировать, нужна диагностика, мы должны понимать, в каком состоянии находятся наши основные фонды, чтобы более точно планировать и в дальнейшем снижать затраты на ремонт и содержание основных средств. Для этого всего нужна реорганизация ремонтных и диагностических подразделений (предприятий).
Выше уже говорилось, что все предприятия имели разную организационную структуру. Ремонтники находились в производственных цехах, где-то они были централизованы, подчинение было разное. В таких условиях эффективно управлять и настраивать процессы было невозможно. Но мы полагали, что последовательное решение этих четырех задач нам позволит качественно изменить состояние управления основными фондами.
Практически осуществляться программа начала с 2007 г., когда было выделено финансирование и выбраны два достаточно крупных завода для пилотного проекта.
Цели были амбициозные: применить все или почти все из лучших практик, что было известно на тот момент. Максимальные конфигурации, лучшие средства диагностики, самые передовые подходы в реорганизации, нормативная база — на все оборудование 100%. Такой подход не совсем себя оправдал, был слишком амбициозен.
Цели программы ПОФ | Рычаги достижения |
1. Сделать бюджетирование и учет затрат на поддержание основных фондов прозрачными и обоснованными для центрального аппарата и предприятий | 1. Создание единой базы данных нормативов затрат на трудовые и материальные ресурсы для каждой ремонтируемой позиции. 2. Наличие объективной информации о техническом состоянии оборудования. 3. Применение информационной системы для эффективного планирования объема ремонтов и ресурсов, необходимых для его выполнения. |
2. Повышение эффективности вложения средств в поддержание основных фондов. | 1. Увеличение межремонтных периодов. 2. Оптимизация объема ремонтных воздействий. 3. Предотвращение дополнительных затрат на внеплановые ремонты. |
4. Получение дополнительной прибыли за счет увеличения рабочего времени оборудования. | 1. Сокращение количества и времени внеплановых простоев. 2. Сокращение длительности плановых остановочных ремонтов. |
5. Повышение надежности оборудования и уровня промышленной безопасности | 1. Применение современных средств диагностики и неразрушающего контроля для постоянного мониторинга технического состояния оборудования и предотвращения аварийных остановок. |
Итак, какие задачи мы себе ставили и чего собирались достичь:
- сделать бюджет и учет затрат на поддержание основных фондов прозрачным и обоснованным;
- выяснить эффективность вложения средств на поддержание основных фондов;
- получить дополнительную прибыль за счет увеличения рабочего времени оборудования;
- повысить надежность оборудования.
Наименование проекта | «Внедрение передовых методов поддержания основных фондов на предприятиях третьей очереди ОАО «СИБУР Холдинг» |
Номер проекта | Предварительный приоритет |
Функциональная область | Управление техническим обслуживанием и ремонтом оборудования на предприятиях |
Организационная область | ОАО «СибурТюменьГаз»; ООО «Тольяттикаучук»; ОАО «Красноярский завод синтетического каучука»; ОАО «Уралоргсинтез»; ОАО «Сибур-ПЭТФ»; ОАО «Пластик» |
Бизнес-цели проекта | — прозрачное бюджетирование и учет затрат по мероприятиям поддержания ОФ; — повышение эффективности затрат на текущие объемы ремонтного обслуживания; — увеличение рабочего времени оборудования; — сокращение внеплановых остановок и объемов недополученной продукции. |
Результаты проекта | — управление процессом ТОиР в информационной системе с помощью разработанных нормативов по стандартизированным процедурам; — создание функций управления надежностью на основе статистики ремонтов, данных диагностических систем и производственных рисков. |
Функциональный заказчик | Департамент технического развития и ремонтов СТиОП, Дирекции |
Составные части (этапы) | Внедрение ИТ-решения, сбор НСИ для ИТ-решения, внедрение средств и методов диагностики, реорганизация ремонтных и диагностических служб |
Срок начала (плановый) | 1.07.2010 | Срок окончания (плановый) | 30.09.2011 |
Оценка бюджета | |
Затраты на оборудование и его инсталляцию | Затраты на лицензии ПО | Консультационные услуги | Сопровождение |
Уже закуплена корп. лицензия |
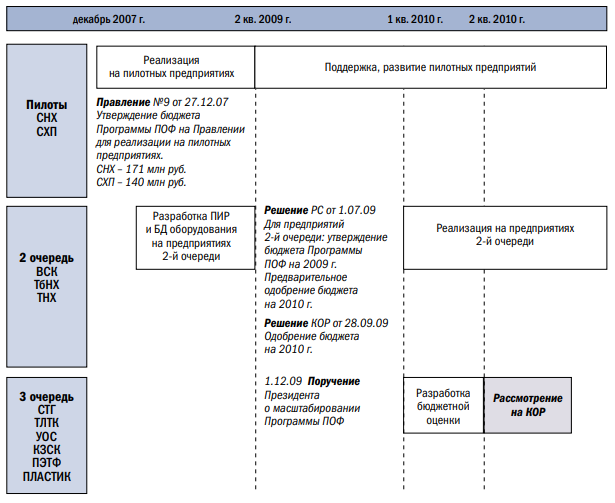
Мы определили, какие направления будут реализованы на каждом из предприятий. Например, база данных оборудования и нормативов собиралась для всех предприятий. Было собрано более миллиона позиций по всем предприятиям. Диагностику мы также делили на несколько направлений: портативные средства, стационарные системы вибродиагностики, приборы неразрушающего контроля и диагностика электрооборудования. По этим направлениям проводили анализ каждого предприятия, выбирали, что для кого нужно поставлять. Таким образом мы сформировали «пакет», который будет реализовываться на каждой производственной площадке. В среднем реализация одного этапа занимала от полутора до двух лет.
Подробнее остановлюсь на реорганизации ремонтных и диагностических подразделений. Какие процессы мы рассматривали, подходя к реорганизации? Какие процессы мы хотели либо улучшить, либо переконфигурировать, либо вывести их в ноль (так как не все эти процессы на предприятиях реализовывались вообще):
- стратегическое управление основными фондами предприятия,
- планирование работ и воздействия по управлению фондами,
- подготовка запланированных воздействий реализации,
- управление работами по ТОиР,
- контроль и учет работ,
- бизнес-планирование и управление издержками по основным фондам предприятия,
- управление структурой и деятельностью подразделений ТОиР,
- управление и развитие базы данных оборудования, базы данных нормативов АСУ ТОиР,
- управление подрядными организациями, выполняющими работы по ТОиР,
- учет технического состояния основных фондов,
- управление техническим состоянием основных фондов,
- управление надежностью,
- анализ результатов ТОиР.
Те структуры, которые были у нас на предприятиях, часть задач, конечно, выполняли, так как предприятия функционируют, выпускают продукцию, занимаются ремонтами, осваивают бюджеты, модернизируют и обновляют основные фонды. Все это было, но часть функций либо не выполнялась вообще, либо эти функции у подразделений или специалистов были не основными, выполнялись, на наш взгляд, в недостаточном объеме, не позволяли развивать систему в целом. Поэтому, когда мы думали, как реорганизовать подразделение, мы исходили из нескольких принципов:
- Функция планирования работ по ТОиР должна быть выделена, она не должна быть смешана ни с какими другими функциями.
- Функция исполнения работ также должна быть отделена от других функций.
- Функция контроля должна быть выделена.
- Подразделения должны быть централизованы и управляться из единого центра (ремонтные подразделения), то есть
управление, направленное на эффективное использование средств и повышение эффективности обслуживания основных фондов, должно реализовываться из
одного центра.
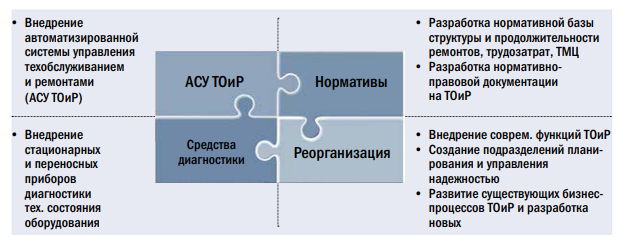
Собственно, из этого мы исходили, когда предлагали какие-то целевые структуры.
Надо сказать, что наше представление о том, какими они должны быть, тоже менялось.
Направление | СТГ | ТЛТК | УОС | Пластик | ПЭТФ | КЗСК |
Реорганизация | • | • | • | • | • | • |
Обучение персонала | • | • | • | • | • | • |
АСУ ТОиР | • | • | • | • | • | • |
БД оборудования | • | • | • | • | • | • |
БД нормативов | • | • | • | • | • | • |
Портативная вибродиагностика | • | • | • | • | • | • |
Стационарная вибродиагностика | • | • | • | • | ||
Приборы неразрушающего контроля | • | • | • | • | • | |
Диагностика эл. оборудования | • | • | • | • |
Изначально мы предлагали централизовать службы (то есть вывести весь ремонтный персонал из производственных подразделений в единые службы, подчиненные главным специалистам, которые, в свою очередь, подчинялись главному инженеру); выделить службы управления надежностью; создать единую службу планирования, которая бы планировала все работы по ТОиР по всем направлениям, в подчинении главному инженеру.
Задачи | СТГ | ТЛТК | УОС | Пластик | ПЭТФ | КЗСК | Всего |
Обучение и реорганизация персонала, чел. | 120 | 110 | 57 | 32 | 18 | 20 | 357 |
Обучение и реорганизация персонала, чел. | 20 | 50 | 63 | 24 | — | 10 | 167 |
Приобретение МФУ, принтеров, шт. | 10 | 35 | 31 | 12 | — | 5 | 83 |
Приобретение сетевого оборудования, компл. | — | 1 | — | — | — | 1 | 2 |
Прокладка сетей, км | — | 1 | — | 1 | — | — | 2 |
Приобретение серверов, шт. | 6 | 3 | 3 | 3 | 3 | 3 | 21 |
Консалтинг по внедрению | 864 | 652 | 530 | 333 | 303 | 303 | 2985 |
Интеграция с существующими системами | 86 | 65 | 53 | 33 | 30 | 30 | 298 |
Со временем у нас это представление несколько изменилось. То, что мы используем уже сейчас, — это объединенная служба технического заказчика, куда входят отделы по ТОиР механического и энергетического оборудования и оборудования КИПиА и отдел обеспечения ТОиР. То есть эта служба занимается всеми вопросами, связанными с реализацией технической политики (и только с реализацией!) и обслуживанием основных фондов.
Задачи | СТГ | ТЛТК | УОС | Пластик | ПЭТФ | КЭСК | Всего |
Создание БД оборуд., кол-во записей, тыс. шт. | 124 | 123 | 94 | 38 | 19 | 20 | 418 |
Создание БД нормат., кол-во комплектов, тыс. шт. | 4,2 | 8,2 | 6,5 | 2,6 | 0,7 | 0,7 | 22,8 |
В данном случае главная служба главного специалиста сфокусирована на вопросах развития и технических вопросах переоснащения и формирования технической политики. Эта служба выполняет регламентные работы и те работы, которые связаны с реализацией технической политики. Это модель работающая, на нескольких предприятиях она реализована и успешно работает, но еще не на всех.
Нужно учесть, что условия, которые были в 2006—2007 годах, и те, которые есть сейчас, существенно отличаются. Если ранее 80—90% работ по ТОиР выполнялись собственным ремонтным персоналом предприятия, то сейчас это соотношение изменилось. На некоторых предприятиях нет вообще собственного ремонтного персонала, а на большей части процент выполнения работ внешними подрядчиками колеблется от 60 до 80 %. То есть персонала становится все меньше и меньше, и доля работ, которая выполняется собственными силами, постоянно уменьшается на предприятии.
Собственно, это была одна из причин создания службы заказчика, которая бы могла эффективно работать с подрядными организациями, с одной большой или с несколькими. Как правило, имеется несколько крупных подрядных организаций, которые закрывают весь спектр ремонтных работ. Служба технического заказчика управляет и собственным ремонтным персоналом, если таковой еще остался, и работает с внешней поддержкой.
Задачи | СТГ | ТЛТК | УОС | Пластик | ПЭТФ | КЗСК |
Портативные приборы замера вибрации (виброметры), шт. | 4 | 15 | 12 | 5 | 4 | 3 |
Спектроанализаторы, шт | 2 | 3 | 2 | 2 | 2 | 2 |
Пирометры, шт. | 4 | 15 | 12 | 5 | 4 | 3 |
Компьютеры* | 7 | 16 | 13 | 6 | 5 | 3 |
Стационарные системы вибродиагностики, шт | + | -(1) | + | -(2) | + | -(3) |
Диагностическое ПО | + | + | + | + | + | + |
Дооснащение лаборатории НК | + | + | + | + | + | -(3) |
Дооснащение электролаборатории | + | + | -(4) | + | -(5) | + |
1 На предприятии всего одна единица первой критичности (мешалка), стационарная система экономически не обоснована.
2 На предприятии нет оборудования первой критичности.
3 Предприятие небольшое, оборудования первой критичности нет. Диагностику целесообразно проводить переносными
приборами и на иные диагностические работы привлекать сторонние организации.
4 Услуги предоставляются сторонними организациями.
5 Нет потребности в дооснащении.
Рис. 6. Внедрение диагностических систем и приборов — объем закупок
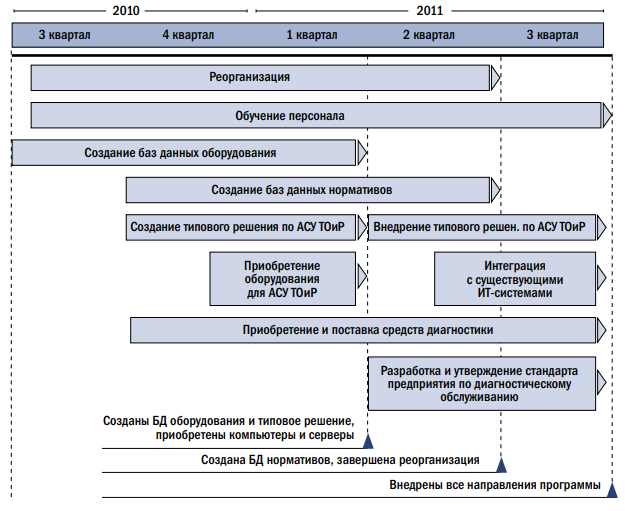
В: Местный персонал остался в подчинении цехов, или он выведен?
О: Ремонтный персонал выведен из состава цехов, централизован.
В: А подрядные службы на аутсорсинге — это, как у нас обычно бывает, все те же самые люди, которые раньше работали, или это реальные компании, с нормальными базами, отчетностью и так далее?
О: И так, и так. Часть компаний — это те, которые просто вывели на аутсорсинг собственный ремонтный персонал, и это дочернее зависимое общество.
В: Дочерних сколько процентов от общего числа?
О: У нас 4 завода имеют такие ремонтные подразделения. И на сегодня эта практика прекращена (вывод на аутсорсинг собственных ремонтников и создание из них новых компаний, которые оказывают услугу материнскому предприятию). Эту практику приостановили.
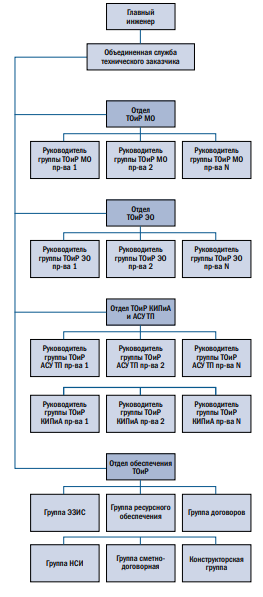
В: Когда эти люди переходят в так называемый аутсорсинг, у вас на себестоимости это отражается?
О: Когда выводят «дочку», на себестоимости это не отражается, потому что условием вывода является вывод на те затраты, которые предприятие несло на содержание этого ремонтного персонала. С этими же затратами выводятся в «дочку».
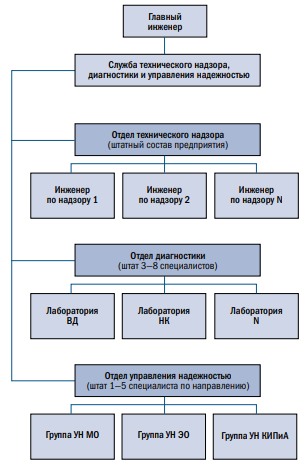
подразделений ТОиР предприятия
В: Смысл выводить, если нет сокращения затрат?
О: Хороший вопрос. Любой расчет показывает, что снижение затрат приводило к снижению качества ремонта. В лучшем случае не меняется ничего, т.е. вновь образованная компания поддерживает тот же уровень ремонтов, но сильно сокращает персонал, при выводе теряется часть квалифицированного персонала, который просто уходит, не переходит из одной компании в другую, а ищет другое рабочее место. Эти компании не развиваются, не становятся конкурентоспособными на рынке, поэтому сейчас эту практику прекратили. Изначально стратегически предполагалось, выводя таким образом часть ремонтного персонала в дочернюю компанию, что через несколько лет, развиваясь, она станет конкурентоспособной на рынке, часть работы она будет получать уже не на материнском предприятии, а на рынке, и со временем ее можно будет продать как активы. Таким образом, если полагать, что этот бизнес не совсем профильный, то продажа таких активов для оценки компаний выгодна. В данном случае идея здравая, но не получилось того, что хотели, эти компании не стали конкурентами, они неинтересны для покупателей.
В: Обратный процесс не планируете?
О: Сейчас рассматривается возможность обратного процесса. По одному из предприятий это уже произошло. Вернули обратно выведенный персонал. По другим предприятиям пока не планируется такого, но процесс пока приостановлен, т.к. наши компании не научились это делать хорошо и получать тот результат, на который рассчитываем.
Если говорить про сервисное обслуживание, то эти компании не стали сервисными. Они делают очень большую работу, даже занимаются планированием, но при этом не несут ответственности, в том числе финансовой, за результаты своей работы. Договор не предполагает наступление финансовой ответственности при каких-то существенных потерях предприятия. Если заключить такой договор, то при остановке завода на 1—2 дня это компанию просто разорит.
Бизнес они не страхуют, они не отвечают за оборудование, за качественный или инновационный ремонт, это не входит в их обязанности по договору, поэтому это нельзя назвать вполне сервисом. К нам приходила западная компания, которая предлагала взять на полный сервис предприятие, причем по всем направлениям: по механике, по КИПу, по энергетике. Стоимость этого сервиса была в пять раз выше, нежели текущие затраты на содержание персонала и на чистое финансирование. Поэтому нам не подходит. Но при этом они гарантировали, что берут всю полноту ответственности за результаты работы, и требовали пятилетний контракт. Мы оказались к этому морально не готовы.
Функция управления надежностью и технического надзора за время 90-х годов, во время развала и стагнации до настоящего времени, постепенно деградировала: сокращалась численность, терялись те функции, которые были прописаны в правилах, и то, что является основным предметом работы, все выродилось в бумажное сопровождение правил. В подчинении эта функция находилась у разных служб: от главного механика до служб безопасности.
Соответственно, функцию надзора она не выполняла в полном и необходимом объеме, для того чтобы специалисты, принимающие решения, знали и понимали действительное техническое состояние своих объектов и могли обоснованно эти решения принимать. Поэтому решено это подразделение вывести из-под управления непрофильных служб, передать в непосредственное подчинение главному инженеру и ввести в его составе еще отдел по управлению надежностью оборудования. Это новое для нас, ни на одном предприятии такого не было.
Сейчас вкладываемся в программы обучения для специалистов, таких специалистов нет, в вузах их не учат, почти нет людей на рынке, которых можно было бы купить с готовыми знаниями. Если они есть, то стоят дорого, по ценовой политике не подходят. Поэтому мы готовим специалистов по надежности из собственных кадров. Следующим шагом будет приобретение IT-продукта для организации работы этих подразделений. Структура тобольского завода реально действующая — и на сегодня всех устраивает (рис. 10).
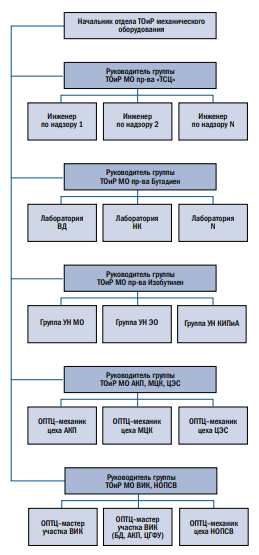
Функции и задачи подразделений ТОиР предприятий
Группа НСИ и ТОиР
- Ведение справочников и классификаторов АСУ ТОиР.
- Разработка и изменение правил ведения справочников и классификаторов АСУ ТОиР.
- Проверка соблюдения пользователями АСУ ТОиР технологических инструкций и регламентов работы в информационной системе Infor EAM EE.
- Управление системным администрированием Infor EAM.
- Функциональное администрирование Infor EAM.
- Состав группы: системный администратор (возможно, сотрудник ИТСК), функциональный администратор, специалист по НСИ.
Группа ресурсного обеспечения
- Организация и контроль работ по интеграции данных АСУ ТОиР с другими информационными системами общества.
- Формирование сводной заявки на ресурсное обеспечение утвержденной Программы ПОФ очередного года планирования.
- Организация и контроль своевременного обеспечения работ по ТОиР расходными материалами и необходимыми запасными частями в местах проведения работ в требуемом количестве и с соблюдением принципа «точно в срок».
- Организация и контроль своевременного обеспечения работ по ТОиР требуемыми грузоподъемными механизмами, спецтехникой, средствами механизации и измерений.
Состав группы: 1—3 специалиста в зависимости от количества технологического оборудования, степени аутсорсинга ремонтных работ и уровня развития процессов МТО предприятия.
Отдел управления надежностью
- Сбор информации по надежности эксплуатируемых основных фондов общества:
- информация и статистика (информация — сведения об объектах, их свойствах и степени влияния друг на друга) по использованию оборудования;
- информация и статистика по наработке оборудования;
- информация и статистика по отказам оборудования;
- информация и статистика по ремонтам оборудования.
- Анализ информации и показателей надежности основных фондов. Контроль фактических показателей надежности.
- Анализ влияния видов и методов ТОиР, применяемых запасных частей и расходных материалов на надежность основных фондов.
- Прогнозирование показателей надежности основных фондов и разработка мероприятий ее повышения.
Группа вибродиагностики
- Организация и проведение имеющимися диагностическими средствами периодического и внепланового мониторинга технического состояния динамического технологического оборудования в установленном порядке.
- Организация и проведение периодического и внепланового мониторинга технического состояния статического технологического оборудования по параметрам вибрации в установленном порядке.
- Разработка актов, рекомендаций, технических и технологических решений по результатам анализа данных по диагностике и мониторингу технического состояния производственных активов.
Отделы ТОиР оборудования
- Разработка мероприятий реализации Технической политики предприятия.
- Управление стоимостью владения и жизненным циклом оборудования предприятия.
- Долгосрочное/перспективное планирование управления основными фондами предприятия.
- Планирование работ/воздействий по ТОиР основных фондов в рамках годовой программы ПОФ.
- Расчет необходимого ресурсного обеспечения выполнения работ/воздействий по ТОиР.
- Подготовка к выполнению всех запланированных работ/воздействий по ТОиР.
- Разработка и оптимизация календарно-сетевых графиков остановочных и крупных капитальных ремонтов.
- Организация выполнения утвержденных планов и графиков работ/воздействий.
- Контроль выполнения утвержденных планов программы ПОФ.
- Контроль соблюдения требований НД при производстве работ/воздействий по ТОиР.
- Организация и исполнение операций приемки выполненных работ по ТОиР производственного оборудования.
- Контроль соблюдения правил технической эксплуатации оборудования технологическим персоналом.
- Участие в разработке и исполнение мероприятий по предписаниям надзорных органов.
Состав группы: 1—2 планировщика производства/группы цехов, механики (оперативные планировщики) цехов/установок.
Вот все, что касается реорганизации. Если есть вопросы, я готов
ответить.
В: В каком году вы начали и когда закончите реорганизацию?
О: Мы ее начали сразу и не закончили до сих пор. Организационно для нас реорганизация получилась одним из самых тяжелых блоков. Это связано с тем, что часть менеджмента не понимала необходимости этих изменений, на предприятиях было сильное сопротивление руководителей, главных инженеров этим изменениям. К тому же компания старалась сокращать персонал. Мы понимали, что за счет централизации даже возможно сокращение персонала. Шел «тайный» процесс сокращения, который все излишки вычистил. Сейчас мы находимся в ситуации, когда есть, как минимум, дефицит необходимых специалистов, и вся политика компании направлена на то, чтобы не увеличивать персонал. Если сейчас по конкретному предприятию, чтобы сделать нужную структуру, необходимо увеличение численности (а это почти по всем пред приятиям), то нужны каждый раз конкретные решения с бизнесблоками, убеждение, получение дополнительного финансирования. Все затягивается на очень длительное время, организационный процесс очень сложный. Несмотря на то, что уже понимают, что это необходимо, ответ приблизительно такой: «Да, все отлично, давайте делайте, только персонал не увеличиваем». В этом сложность.
В: В каком году вы ее начали?
О: Начали мы ее в 2008 году. Закончим, как я уже сказал, в первом квартале следующего года. Но это только для 18 предприятий. Сначала мы обозначили целевую модель, которая должна применяться для всех предприятий холдинга. В общем виде она была согласована, она была описана и вписана в функции, какие подразделения и чем должны заниматься, описаны основные функции, почему это так формировалось и почему нужно изменить именно таким образом. Это презентовалось руководству, руководство изначально одобрило саму модель. И тогда говорили, что это не приведет к снижению численности персонала и точно не приведет к увеличению персонала на тот момент. Сейчас, несмотря на концептуальное одобрение, время изменилось, появились цели по сокращению. Сейчас приходится каждый раз по каждому мероприятию проходить этот процесс еще раз, убеждая руководителей в необходимости этих изменений. Мы все-таки делаем, убеждаем, но процесс затянулся по времени. Это повлияло на выполнение других проектов, затянуло сроки выполнения всего проекта. На предприятиях, там, где мы открывали или пытались отладить как минимум часть этого процесса реорганизации, мы вводили саму структуру, утверждали, и на предприятии соглашались: «Да, мы это делаем». Когда дело доходило до формирования штатного расписания, до должностных инструкций, до положения отдела, предприятия сами это сделать не могли. Нам приходилось заниматься еще и этим, вплоть до должностных инструкций. Либо качество проработки было такое, что выхолащивало саму идею функций и обязанностей.
Следующее направление нашей программы — это диагностика, внедрение средств диагностики. Это наиболее простое направление из четырех, которые мы внедряли, от которого потенциально можно получать самую быструю отдачу. Если говорить про расходы, то примерно половину всей стоимости проекта заняло приобретение этих средств. На всех предприятиях были разные ситуации: у кого-то диагностика уже была в каком-то виде сформирована, были лаборатории контроля, результатами диагностики активно пользовались, но были и предприятия, где не было практически ничего.
Если говорить про собственно диагностику, то мы пока остановились на вибродиагностике динамического оборудования. Изначально рассматривали вопрос по диагностике и статического оборудования, но решили этот вопрос пока отложить из-за, с одной стороны, высокой стоимости таких систем, а с другой стороны — на наш взгляд, и сейчас еще отсутствуют достаточно внятные методики и оценки результатов такого рода диагностики, которые бы использовались всеми.
По диагностике динамического оборудования все ясно, история развития большая, есть приборы, есть специалисты, центры подготовки — с этим все просто, и можно получать достаточно быстро реальные экономические результаты.
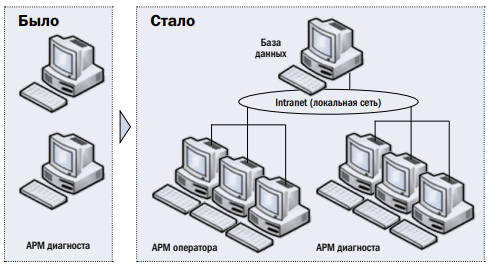
Рис. 11. Доступность диагностических данных. От разрозненных элементов перешли к системе
Мы построили систему двухуровневой диагностики динамического оборудования.
Первый уровень — это простые измерители вибрации, регистраторы, которыми пользуется либо оперативный персонал, либо ремонтник.
Второй уровень — это, собственно, эксперты-вибродиагносты с экспертными приборами, которые делают замеры оборудования уже по каким-то графикам либо по вызову и дают экспертное заключение, рекомендации по дальнейшей эксплуатации, по выводу в ремонт либо по тому, что нужно в этом оборудовании ремонтировать и менять. И к этому уровню также относятся стационарные системы вибродиагностики, которыми оснащается оборудование первого и второго уровня критичности.
Что такое уровни критичности? Первый уровень критичности — это то оборудование, остановка единицы которого останавливает либо цех, либо все предприятие по выпуску продукции; второй уровень критичности — это снижение качества или снижение производительности оборудования.
Вот такие сложные объекты, критичные для предприятия, мы и оснащали стационарными объектами вибродиагностики.
Если говорить про саму систему, это не только приборы, это еще и персонал, который ими пользуется, это некая система, которая построена на предприятии, которая позволяет эффективно применять результаты этих измерений.
Мы выделили функцию вибродиагностики, при необходимости проводили дополнительное обучение. На каждом предприятии, куда покупались приборы, разрабатывался стандарт по обслуживанию оборудования, в котором описывались все процедуры: как и что нужно диагностировать, с какой периодичностью, как принимать решения, кто в этом участвует. То есть описан весь процесс, чтобы можно было новые приборы и новые компетенции встроить в систему ТОиР завода и получать ощутимый результат в виде увеличенного межремонтного пробега, увеличения качества ремонта, воевременного ремонта и, как следствие, — сокращения затрат на ремонты.
Это область, где можно быстро получить результаты и считать финансирование достаточно легко. Проект быстро окупается, здесь главное — правильно посчитать. Применение новой техники позволило повысить производительность, снизилось количество расходных материалов, не требуются реактивы на проявку, уменьшилось время на анализ снимков при повышении качества работы, высокое разрешение снимков позволяет быстрее определять дефекты.
Стоимость работы дефектоскописта ниже стоимости работы подрядчика в 2 раза.
На примере одного из предприятий можно увидеть по годам, как после приобретения средств диагностики и увеличения количества персонала снижалось количество проблемных единиц оборудования (рис. 14).
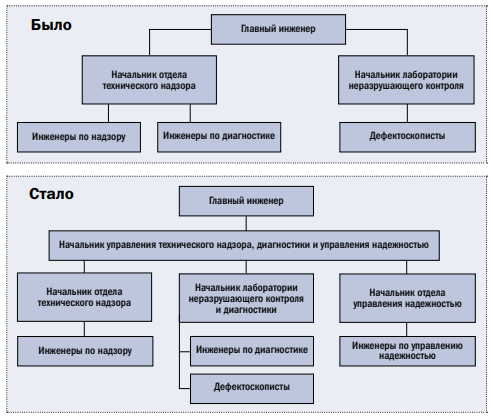
Рис. 12. Структура подразделений технического надзора и диагностики
Это позволило заняться предметным анализом: какие элементы или какие отказы каких элементов наиболее часты, что нужно менять в системе на всем предприятии, какие меры можно принять в целом по предприятию. Это нельзя сделать в рамках одного года, но нужно менять за несколько лет, и нужна какая-то программа.
Если говорить о средствах неразрушающего контроля, здесь тоже покупались новые качественные приборы, очень известные линейки выпускаемого оборудования, может, не самый топ, скажем, не «майбах», но «мерседес». Эти приборы еще долго будут оставаться качественными, обеспечивая высокую достоверность полученных результатов. До реализации проекта на предприятии уже была выстроена система входного контроля.
Применение прибора при выполнении входного контроля позволило за два года снизить процент несоответствия марок материалов с 11 до 4 %! Поставщики хорошо знают, что на предприятии есть входной контроль, и не допускают несоответствий. Все выявленные несоответствия устраняются, что позволяет снизить риск возникновения аварийных ситуаций по причине несоответствия марок материалов.
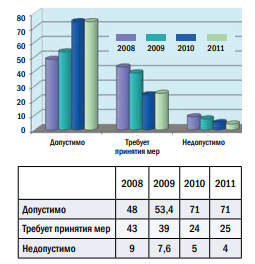
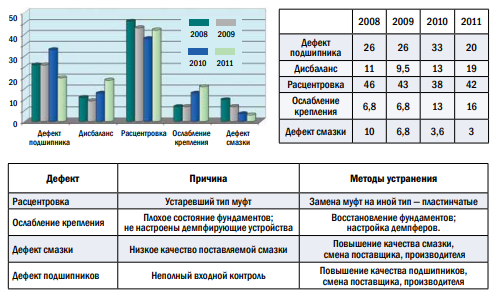
В: Что охватывает спектр входного контроля? Какое количество материалов? Металлы? Подшипники? Объем непонятен: сколько от общего валового материала подвергается контролю?
О: По-разному, это должно определяться регламентом на предприятии. Основное — это металлопрокат (специальный, не конструкционный материал, а какие-то трубы, материалы, используемые для ремонта колонн, трубчатых печей, других опасных объектов). Начинали со стопроцентного контроля, и был очень высокий процент отбраковки. Постепенно поставщиков приучили. Снижение процента дают поставщики, которые знают, что будет проверено и туда везти брак точно не надо. Подшипники сначала проверяли полностью, стопроцентный контроль был с отбраковкой до 30 %. Сейчас, например, из 100 штук берут 10 и если находят один брак, то проверяют всю партию.
На подшипники используют динамические стенды. Разные стенды покупались, сейчас остановились на одном, но не скажу марку стенда — не мое направление. Я знаю, что была проблема: у нас выпускается много стендов, но, как выяснилось, не все они сертифицированы, и результаты измерений не принимаются заводами. То есть вы для себя их отбраковали, а предъявить поставщику вы не можете, потому что они ссылаются на отсутствие сертификации у этого стенда. Поставщиков сертифицированных стендов у нас, по-моему, только два. Для сертификации требуется не только стенд: это некое рабочее
место, мини-комплекс, который включает место для подготовки, расконсервации, нагрева, испытания и пр. То есть когда вы покупаете весь комплекс, тогда дают сертификат, который позволяет вести претензионную работу с поставщиками.
В: Как вы поняли, что нужна именно диагностика?
О: Это касалось того оборудования, по которому происходили возвраты. Просто раньше диагностику не делали либо отбраковывали уже на этапе, когда оборудование начинали резать и пытаться ремонтировать. Раньше диагностировалась какая-то небольшая часть оборудования, ну, скажем, стопроцентно диагностировать входящий металлопрокат, даже черный, без нормальных приборов просто невозможно. Диагностировалось выборочно. Потом, когда купили новые приборы, когда диагностика (анализ) стала занимать несколько секунд, возможно продиагностировать все. Начали выявлять больше случаев несоответствия, делать возвраты, это и привело к улучшению качества поставок.
Обновление и расширение линейки диагностических приборов позволило увеличить количество обследованного оборудования на 70%. Естественно, выбирали для обследования наиболее критичное для технологического процесса оборудование либо наиболее дорогое в ремонте. Это позволило увеличить количество обследований и снизить долю оборудования с диагнозом «недопустимое состояние». Это несмотря на то, что в это время ремонтная база и возможности ремонтных подразделений практически не менялись, ничего особенного для исполнителей ремонта не покупалось. Нельзя сказать, что ремонтники стали более качественно делать, их просто стали контролировать, контролировать состояние оборудования и контролировать ремонты (до ремонта и после ремонта оборудования). Несколько человек-диагностов позволили улучшить работу целой службы.
Мы покупали системы диагностики и переносные приборы, у которых есть возможность передачи данных в сеть завода. Плюс на этих же серверах работали и стационарные системы, что позволило создать единую диагностическую сеть на одинаковых типах приборов и провести интеграцию с АСУ ТОиР. В результате этой интеграции любое обследование, которое выявляет недопустимое состояние или требует принятия мер, автоматически создает у планировщика, который отвечает за это оборудование, заявку на выполнение работ, где уже указан диагноз. Это происходит автоматически. Автоматически происходит учет затраченного времени на диагностирование, автоматически создаются отчеты по состоянию оборудования. Мы значительно снизили затраты диагностов на работу в автоматизированной системе, и по сути диагносты работают только в системе диагностической, результаты их работы попадают напрямую, без их участия, в АСУ ТОиР. Это то, что, на наш взгляд, нам удалось достаточно хорошо сделать, удобно для пользователей.
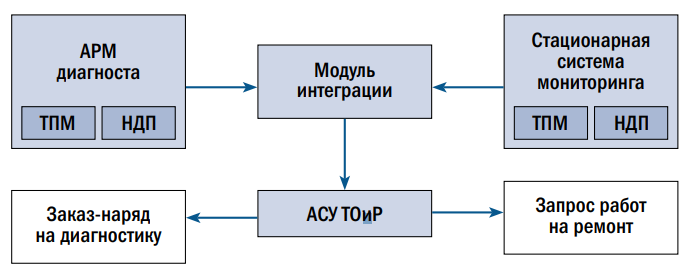
В: Когда данные ТОиР обработались и перешли к исполнителю, а у того свои текущие задачи, как он понимает, что именно эта заявка самая критичная, что там может быть выход из строя?
О: То, о чем вы говорите, — это процесс принятия решения, он описан в стандарте, который разрабатывался. Автоматизация этого процесса — это отражение части стандарта. Диагност в этом процессе оценивает техническое состояние оборудования и дает заключение. Он участвует в принятии решения, но не принимает этого решения. Он может сказать, что оборудование необходимо останавливать немедленно, ибо оно сейчас разрушится, но решение по остановке принимают несколько человек. Это, условно говоря, механик, который отвечает за него, и представитель производства. Принимают решение по остановке либо по выводу в ремонт коллегиально. Это прописано в стандарте. В данном случае задача диагноста выдать правильный и своевременный диагноз. Когда он появляется у планировщика — этот человек планирует ремонт. Он может запланировать его немедленно, а может поставить его через какое-то время, если это позволяет заключение диагноста. Но это его ответственность — когда он его запланирует, потому что он отвечает за его исправное техническое состояние и работоспособность.
В: У планировщика в текущих задачах 60 ремонтов на сегодня. Как он понимает, что вот эту заявку надо первой смотреть?
О: Ну если говорить так, то в АСУ ТОиР в каждой заявке есть отметка о критичности не оборудования, а самой заявки. То, как ее оценивает инициатор. Соответственно, первое, куда смотрит планировщик при выборе заявок для немедленного реагирования, — на эту оценку инициатора. Дальше он принимает решение. При необходимости он
может уточнить.
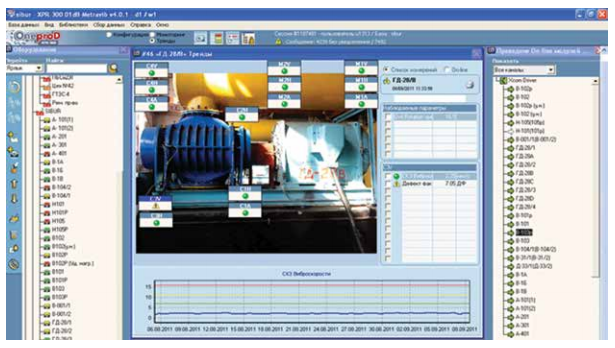
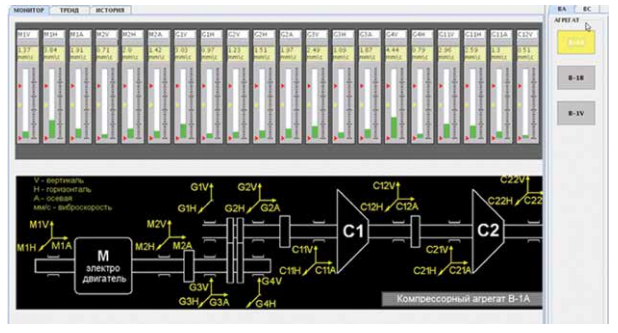
В: Цветовая индикация или как?
О: Нет, там есть просто окно, где указана критичность заявки.
В: То есть надо ее открыть сначала?
О: Заявку? Да, надо открыть.
В: Вот их 60. Как он понимает, какую надо открыть?
О: 60 в день — такого даже у нас не бывает. Ну, в любом случае, если говорить о том, что нужно выполнять немедленно, то все равно есть телефон. Потому что тот же планировщик не сидит целый день за компьютером. Он находится на объекте, как минимум, 30 % времени он должен там находиться. Если в это время приходят какие-то срочные заявки — ему пишут на телефон. Процедуры, которые есть по аварийным ситуациям, по критичным отказам, которые прописаны, наверное, на всех заводах — кто кому что сообщает и что делает, — они не отменяются. То есть если кто-то выяснил, что надо немедленно что-то делать, — людей ищут по телефону, а потом это уже оформляют.
В: А что именно говорит диагност? Что вот это оборудование в недопустимом состоянии, или он говорит, что в этом оборудовании есть подшипник на третьей опоре…
О: Он говорит, например, наименование диагноза — «недопустимо, требует принятия мер». Есть расшифровка, заключение, где он говорит, какой, по его мнению, узел вышел из строя или работает ненормально. Дальше он может еще дать заключение — сколько, по его мнению, это может еще проработать. То есть в заключение обязательно должно входить уточнение места возникновения дефекта.
В: Какое количество оборудования у вас обслуживается, как вы сказали, по фактическому состоянию? Диагностика же проводится для чего — это отражение фактического состояния оборудования.
О: Здесь надо немного разделить объем диагностируемого оборудования и ремонтируемого по состоянию. Потому что оборудование, которое ремонтируется по состоянию, административно должно быть зафиксировано в СТП завода. Должно быть утверждено, что это стратегия обслуживания. Объем такого
оборудования у нас сейчас невелик, и предприятие находится в стадии получения соответствующих разрешений и согласования Ростехнадзора на то, чтобы, имея у себя в арсенале средства диагностики, систему выстроенной диагностики, обученный персонал, стандарт предприятия, который позволяет качественно диагностировать и принимать решения, перевести такое-то оборудование на ремонт по фактическому состоянию. То есть это легальный путь, который надо пройти, он достаточно затратен по времени, потому что у нас с Ростехнадзором ничего быстро не бывает. Если быстро — то дорого. Если говорить конкретно, то, во-первых, это касается только динамического оборудования. По статическому вообще единицы оборудования, которые разрешено по фактическому состоянию обслуживать, их можно просто по пальцам пересчитать. По динамическому оборудованию — на разных площадках по-разному, но, наверное, процентов 20 динамического оборудования. Если говорить про то оборудование, которое обследуется, то по динамическому оборудованию там, где 15 % ремонтируется по состоянию, официально обследуется диагностическими средствами регулярно процентов 70 уже.
В: Вы сказали, что у вас диагностика рекомендательный характер носит. То есть можно не выполнять? Допустим, 50 заказов сделали, а человек, который выполняет ремонт, говорит, что — нет, оборудование будет работать дальше.
О: Такая ситуация еще до недавнего времени была. Сейчас она начала выправляться, но мы специально смотрели, сколько заказ-нарядов сформировано по рекомендации диагностики и висят необработанными либо по ним не принято решение. Их там было до 50, это не значит, что по ним всем нужно было немедленно ремонтировать, зачастую как раз механик посмотрел и решил, что
сейчас это делать не будет. Часть просто, видимо, не смотрели. Такая ситуация возможна. Мы для того, чтоб с этим бороться, ввели KPI, который как раз показывает процент заказов по диагностике, на которые не отреагировали никаким образом механики либо ответственные за оборудование. Границу установили — 10 %. Выше 10 загорается красный свет, это устанавливается нами либо предприятием. Можно установить и 0, и 1. Начали с 10, в нашем понимании при развитии системы этот показатель будет меняться, ужесточаться. Эти KPI сейчас ведет главный инженер. Главный механик их видит у себя на экране, как только заходит в систему. Он видит в виде светофора либо спидометра — что там в красном свете? Опять не работают с диагностами? Есть повод принимать меры.
В: Если можно, немножко про экстренно-аварийный ремонт. Всем понятно, что есть бюджет годовой, есть возможность планировать на ППР годовой бюджет и запасные части. Какова ситуация именно с экстренно-аварийным ремонтом по заключениям диагноста? И как решается прохождение запасных частей именно на незапланированные ремонты с бухгалтерией и со всеми остальными подразделениями?
О: Мы к этой задаче подходили давно, насколько я помню, это было еще в самом начале нашего проекта одной из задач. Это формирование технического запаса для предприятия и регламент о его использовании, но мы от него отказались, когда наступил кризис, и эту задачу вычеркнули. Сейчас к этому вернулись, разработана методика формирования аварийно-технического запаса, методика формирования перечня и количества тех запасных частей, которые на предприятии должны находиться в любой момент, и методика пополнения этого запаса и доступа к нему. Пока это реализовано на трех предприятиях из всех, на остальных эта методика сейчас в стадии распространения. Формирование самого запаса оказалось достаточно непростой вещью, когда готова методика, затраты, ресурсы, и все это посчитать на предприятии… Для формирования всего этого перечня необходимы значительные затраты. Если сравнивать с годовым бюджетом закупки материалов на любой завод, то в зависимости от того, что лежит на складах, это может составлять от 20 до 50 %. Поэтому на предприятиях стоимость этого аварийно-технического запаса высока, и его пополнение разбивают на два года (условно). Таким образом, если у вас возникает аварийная ситуация или необходимость в ремонте внеплановом, то есть возможность обратиться к аварийно-техническому запасу и взять оттуда, либо, если там нет, предполагается, что эта запчасть либо материал будут куплены очень быстро, отходя от рыночной процедуры. Что касается бухгалтерии. Сейчас у нас вводится (только на двух заводах введен) новый регламент, новый стандарт формирования бюджета на поддержание основных фондов. Со следующего года будет введен на всех предприятиях. Одной из статей этого бюджета является лимит на аварийные работы. То есть это фиксированный процент от общего бюджета, выделенная статья. Все затраты и незапланированные работы привязываются туда, берутся из этой статьи. Для нас это несколько ново, хотя вроде бы для всех очевидно, что если раньше планировался бюджет, то предполагалось, что он будет «безаварийный», все деньги идут на какието плановые работы, внеплановых нет. Понятно, что такого никогда не бывает, поэтому решили упростить всем жизнь, не обманывать друг друга, и выделили статью. Какой здесь нужен процент, пока не очень понятно, 10—15 % пока выделяется на эти затраты, но это скорректируется, когда будет получена первая статистика. Официально такой статистики никто не вел — сколько денег тратится на внеплановые расходы, — потому что это было одной из причин последующих каких-то репрессивных действий. Сейчас можно будет оценить, сколько же денег туда уходит, соответственно, скорректировать целевую цифру этой части бюджета.
В: Вы можете сформулировать механизм формирования перечня бюджета?
О: В общих чертах могу, но сама методика очень громоздкая. Мы привлекали для этого западную компанию, которая работает на нашем рынке. Она разрабатывала методику совместно с предприятием и предложила методику, которая была сильно изменена по нашему пониманию и пониманию специалистов предприятия. Учитывала целый ряд показателей, я сейчас не смогу их выставить все по важности, но основные назову:
- критичность оборудования;
- необходимое количество запчастей и материалов на все единицы оборудования на предприятии;
- стоимость этих запчастей;
- стоимость их хранения;
- время, необходимое на приобретение этого материала или запчасти, если возникла потребность немедленно заменить;
- вероятность возникновения отказа на конкретной единице оборудования;
- количество таких единиц оборудования, где участвует этот материал;
- стоимость запчастей.
Все не помню. Там в системе расчета достаточно сложная формула, на мой взгляд, вообще непонятная, там даже факториалы есть. Не знаю, что там можно факториалами считать, но те результаты, что получаются, в основном интуитивно принимаются специалистами предприятий. На некоторых предприятиях специалисты разных служб сделали сами аварийно-технический запас, исходя из собственной компетенции, знаний и опыта — сформировали некий список. Эта методика значительно расширяет этот список, то есть он получается больше и дороже. Но компания на это пошла. Сказали: раз вы нам посоветовали — хорошо.
В: Скажите, как проводится (если проводится) анализ потенциальных рисков и отказов процесса?
О: Я говорил, что мы к этому направлению только подступаемся, мы создаем службы, на предприятиях набираем специалистов и собираемся их учить. Действующее подразделение, которое занимается надежностью, в каком-то виде у нас есть на одной площадке, ни чем таким оно пока не занимается. Они собирают статистику по всем видам отказов. Эти все отказы привязаны к критическому оборудованию. Считаются последствия в деньгах и в коэффициентах, в которых исследуется возможный ущерб или возможная опасность (если это связанно с техникой безопасности), и даются прогнозы по отдельным позициям критичного оборудования по раз витию ситуации, которую обсчитывают. Нельзя сказать, что это уже какой-то полноценный анализ. Еще недостаточно в подразделениях людей, недостаточно компетенции. Но есть результаты обработки статистики за два года, и даже это уже позволило сделать две про граммы обновления оборудования (как
минимум две) на предприятиях, только затратных — полностью обновлена часть оборудования, закуплены новые комплексы. И позволило сменить позицию руководства, т.к. по отдельным объектам причиной основных отказов являлась неправильная эксплуатация оборудования. Руководство начало более внимательно следить за производственным персоналом, что позволило без каких-либо затрат улучшить ситуацию с отказами. В этом и следующем году у нас будет серьезное масштабное обучение для сотрудников разного
уровня управления, начиная с главных специалистов и заканчивая специали стами службы надежности. Со следующего года мы намерены этим более плотно заниматься, так как будут сформированы на всех предприятиях отделы, будет персонал, у которого эта функция будет основной и единственной, они будут обучены. Мы надеемся, что в следующем году будут уже общие методики, стандарты некоего минимально го уровня на небольшую перспективу, с чего должны все начинать работу, будет построена система отчетности и динамики. И тогда уже, надеемся, будут какие-то результаты, более структурированные и понятные, которыми можно будет пользоваться. В дальнейшем планируем закупку специализированного программного продукта.
В: Скажите, обучение на какой базе будет проводиться? У вас уже есть люди, которые будут обучать? Где их вы взяли?
О: Нет, у нас таких людей нет, которые сами бы могли обучать. У нас есть несколько человек, которые этим занимались и имеют некий практический опыт. Они могут только говорить о том, как они это строили и какой опыт у них есть. Для обучения мы нанимаем компанию, имеющую в своем составе специалистов, которые занимались внедрением, постановкой и самой этой функцией на предприятиях, сами были сотрудниками управления надежности, знают программные продукты и имеют приличный опыт. Часть из них — это зарубежные специалисты, к сожалению. О покупке программного обеспечения речь пока не идет, потому что некогда его покупать.
Руководитель проекта внедрения передовых методов поддержания основных фондов на предприятии.
Журнал Prostoev.NET № 2(11) 2017