Оборудование на предприятиях находится в работе фактически без остановки, в силу чего к нему предъявляются жесткие требования по эксплуатационной готовности. Бесперебойная работа является важнейшим условием для оборудования критических инфраструктурных и стратегических объектов.
Существующая технология предусматривает при поломке оборудования включение резервного, в результате чего предприятие не несет потерь, связанных с остановом технологического процесса. При этом возникает задача выявления дефектов в неисправном оборудовании.
Значительный разбор оборудования с последующим выявлением неисправностей зачастую является дорогостоящим мероприятием в силу сложности оборудования, его размеров и веса.
Типовым решением ранней диагностики и сигнализации развития неисправности оборудования является регулярный мониторинг их состояния с использованием датчиков вибрации корпусных деталей и осевого смещения вала насоса. Однако показания этих приборов в реальных условиях эксплуатации характеризуют уже значительное развитие неисправности, и в случае с критичным оборудованием восстановление работоспособности может привести к существенным финансовым и временным затратам.
Другой задачей, связанной с повышением эффективности технического обслуживания и ремонта, является точная локализация неисправного узла или поломки. Превышение допустимого уровня вибрации говорит о наличии неисправности, но для локализации причины необходимо полностью демонтировать и разобрать оборудование. Отсюда вытекает основная задача – это обнаружение и точная локализация неисправности на ранней стадии до этапа ее активного проявления.
Для решения поставленных задач существует программно-аппаратный комплекс – акустическая камера. Он представляет собой видеокамеру, по контуру которой расположены чувствительные элементы (микрофоны).
Схема установки имеет следующий вид (рис. 1). Акустическая камера направляется на геометрически сложный, массивный объект, каким, к примеру, является насосный агрегат. Звуковая волна до каждого из микрофонов доходит за разное время, что обусловлено разными дистанциями от источника вибрации до каждого из чувствительных элементов. Каждый из четырех микрофонов фиксирует одновременно поступающие звуковые волны, и при резком изменении частоты, не соответствующем технологическому процессу (стук, треск и т.п.), акустическая камера фиксирует это и рассчитывает точное расположение в плоскости «некорректного» звука путем наложения вычисленных координат на изображение, полученное с камеры, с учётом расстояний от источника вибрации до микрофонов.
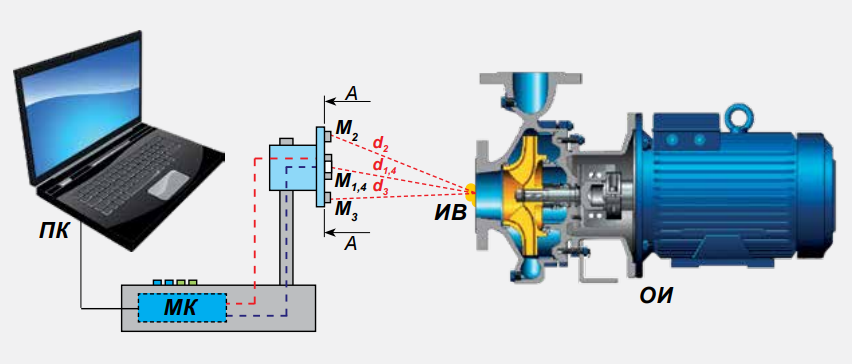
Расчет производится с использованием уравнений окружности с центрами в месте расположения микрофонов, где единственная неизвестная переменная z – интервал времени прохождения звуковой волны от источника шума до ближайшего микрофона (определяет первый радиус d1) (рис. 2).
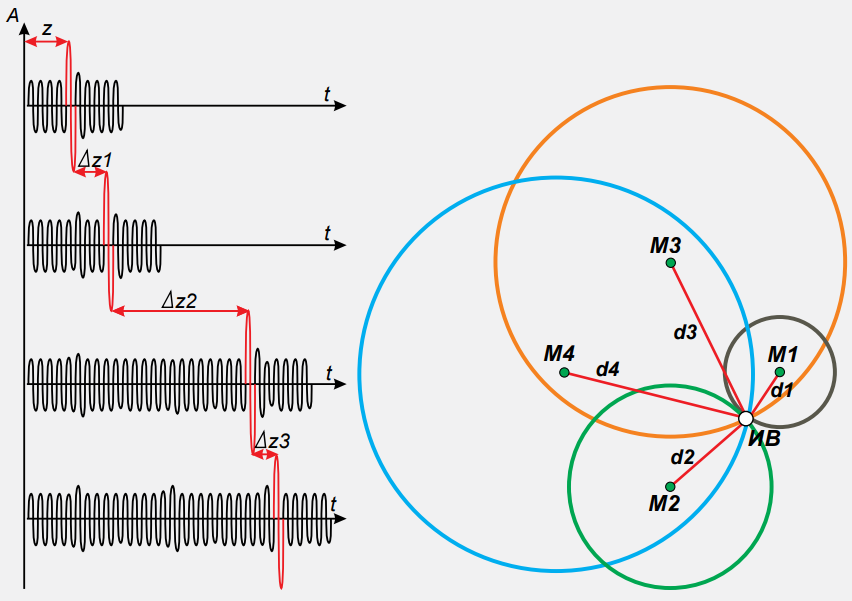
Затем из системы уравнений определяется интервал времени z, после чего из каждого центра строится окружность, и находится общая точка пересечения с координатами области, которая характеризуется «некорректным» звуком.
Микроконтроллер обрабатывает сигналы с аналоговых датчиков (микрофонов), преобразует их в цифровой вид и передает массивы данных на персональный компьютер, где производятся все вышеописанные расчеты. Калибровка микрофонов производится встроенными в систему потенциометрами путем формирования эталонного звука.
Программное обеспечение автоматически на основе анализа входных массивов создает на видеокадре вероятностный градиент (область) локализации данного «некорректного» звука (по результатам расчета уравнений) и масштабирует результат под формат окна камеры (рис. 3).
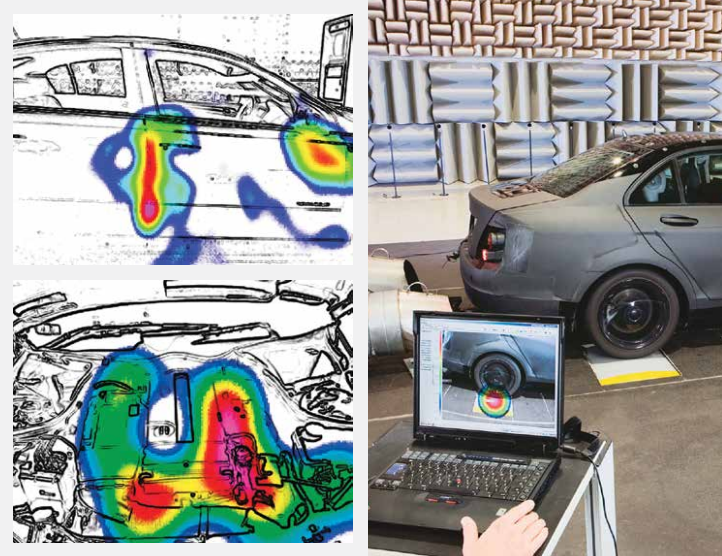
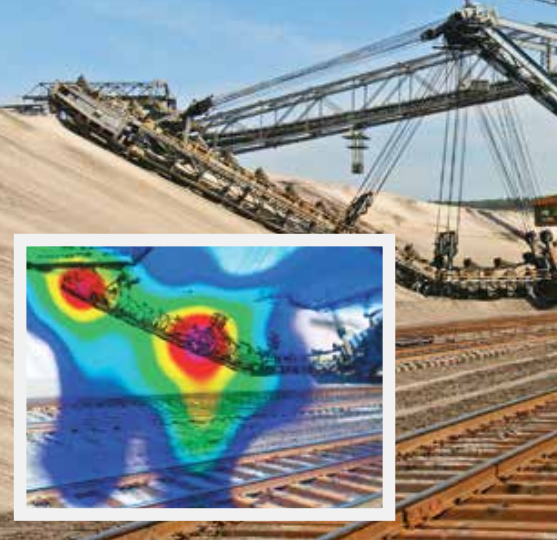
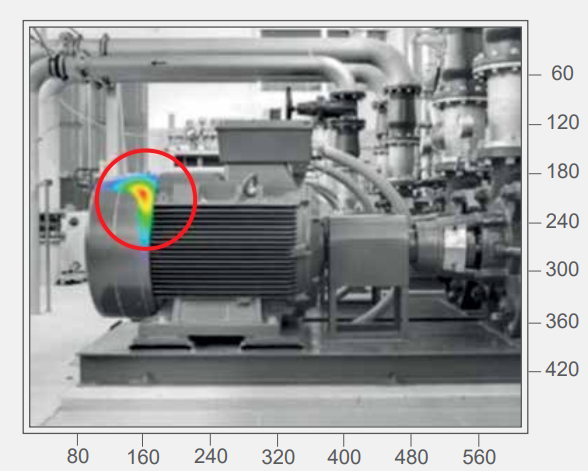
Программное обеспечение позволяет оператору просматривать исторические тренды, на которых изображаются графики эксплуатационного шума насосной станции с возможностью выделения его параметров для точной локализации источника вибрации. Программа автоматически выделяет цветом моменты времени на временной оси, в которые был замечен подозрительный шум.
Отсняв для эталона нормальную работу оборудования, получаем уникальный звуковой отпечаток, и любое изменение данной сигнатуры обозначает недочет в работе, например, сухое трение качения в несмазанном подшипнике. Комплекс сразу выявит данный недочет и на видеоизображении укажет, в какой части агрегата не смазан подшипник. Также комплекс умеет определять неполадки не только на динамическом, но и на статическом оборудовании, емкости, сосуды, трубопроводы – определять утечки жидкостей и газов, указывать на неисправную работу трансформаторов, подстанций, выявлять коронные разряды и пр.
Основным экономическим эффектом является уменьшение затрат на ремонт оборудования за счет увеличения срока службы агрегата. Основными технологическими преимуществами являются диагностика неисправностей на ранней стадии за счет анализа программной системой трендов эксплуатационного шума агрегата и точная локализация выявленной неисправности в визуальной плоскости оборудования, перпендикулярно которой направлена акустическая камера.
Кроме того, гибкость настройки акустической камеры под эксплуатационные и конструктивные особенности оборудования обеспечивает простоту интеграции в действующие на предприятии информационные системы управления производством.
К общим достоинствам комплекса следует отнести также:
- возможность предупреждения аварийных ситуаций;
- регулярность диспетчерского контроля состояния агрегата;
- мобильность при использовании.
Подобный комплекс применяется в Фольфсбурге на заводе VOLKSWAGEN – в прессовом цехе, простой которого остановит крупнейшее производство в мире. В настоящее время в России таких комплексов нет, хотя в нашей стране много предприятий, для которых стоимость комплекса несопоставима с размером рисков, например, атомщики и прочие критичные и стратегические компании.
Журнал Prostoev.NET № 2(27) 2021
Д. АЮШЕЕВ, консультант ООО «Простоев.НЕТ»