В условиях возрастающей конкуренции на рынке производства цемента, а также повышения стоимости сырья, материалов и комплектующих для оборудования очень остро встает вопрос о себестоимости продукции. Разработка и внедрение современной системы управления техническим обслуживанием и ремонтом оборудования является неотъемлемой частью политики ОАО «ХК «Сибцем» в части снижения себестоимости производства, повышения его надежности, развития предприятий холдинга.
При обсуждении необходимости изменений в существующей системе ТОиР на предприятиях ОАО «ХК «Сибцем» вариант ограниченного по времени динамичного проекта не был принят. Мы пошли по пути небольших постепенных изменений. По прошествии трех лет можно сказать, что путь выбран верно, так как при изучении опыта внедрения подобных проектов всегда выявлялся целый ряд неизбежных проблем. Нам же удалось либо избежать этих проблем, либо они были не настолько острыми. Например, проблемы мотивации, компьютерной грамотности, резкого увеличения функционала и нагрузок на персонал, отсутствие финансирования, неприятие системы на активах (от механика до директора). Из-за отсутствия «агрессивного» внедрения эти проблемы были нивелированы временем, а когда пришли первые результаты, многие из них и вовсе перестали существовать.
Сам проект призван не только оптимизировать систему ТОиР, но и улучшить жизнь ее пользователей на всех уровнях. Ставилась задача не добавить обязанностей людям, а сделать их работу комфортнее и удобнее, убрать лишние действия, сконцентрировать их на профильной деятельности.
Для получения результата в данном случае нужен длительный промежуток времени и, как итог, модернизация системы ТОиР и в целом ремонтной службы. Но реорганизация существующей структуры нам видится как один из завершающих этапов проекта. В настоящее время идет активная фаза внедрения — создание модуля ТОиР в ERP-системе, базы НСИ, журналов и справочников, технологических карт, функционала автоматизации и управления процессом в модуле, разработка новых методических и должностных инструкций, регламентирующих документов, которые «де-юре» закрепят новые бизнеспроцессы.
Проект реализуется на базе ERP-системы Axapta 4. Для этой программы готового решения, которое бы нам полностью подходило, производителем или ИТ-компаниями создано не было. Разработка всех составляющих модуля и его функционала осуществляется путем совместной работы ИТ-специалистов, специалистов предприятий и специалистов Департамента производства, обслуживания и ремонта оборудования Управляющей компании.
Цель — обеспечить оптимальный и качественный переход от системы ППР к системе технического обслуживания и ремонта оборудования по реальному техническому состоянию на основе глубокого анализа множества данных о его работе.
В настоящий момент реализовано несколько блоков в модуле ТОиР.
Первый и основной — каталог оборудования
В разработанной нами структуре и функционале каталога оборудования нет ничего нового для справочников подобного уровня. Он содержит все то, что необходимо для нормальной работы модуля ТОиР: информацию о количестве оборудования, месте его применения, его комплектующих (спецификацию), схемы и чертежи, технологические карты ремонта. Через данный каталог можно перейти в другие модули и справочники, в которых содержится информация о стоимости запасных частей к этому оборудованию, информация о поставке, истории его ремонтов.
Каталог постоянно пополняется. Нет никаких специальных сроков или задач по его наполнению, но в случае проведения ремонта на любом оборудовании специалист обязан предоставить полную информацию о нем (по специальной форме) в службу ИТ для внесения ее в каталог. Соответственно, каталог наполняется информацией постоянно, и только той, которая необходима уже сейчас. Это позволяет применить функционал каталога в модуле тут же конкретным специалистом и не создавать аврала в работе ИТ-службы.
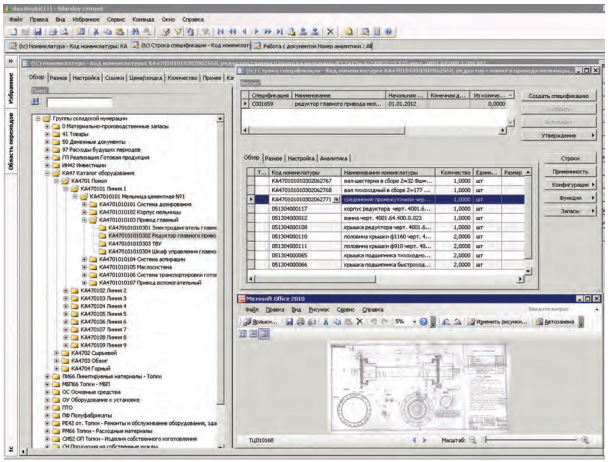
Доступная информация в каталоге позволяет быстро и качественно оформить ремонт оборудования, используя справочники —
спецификации и типовые сметы на ремонт. При выборе нужного оборудования и конкретной детали в нем необходимо указать и способ воздействия — «замена», «ремонт» или «ревизия». Расчет ведомости дефектов для ремонта произведется автоматически на основе данных справочников для конкретной детали и операции. Таким способом решаются задачи нормирования, автоматизации процесса и контроля за бюджетом.
Следующий и не менее важный блок — электронный журнал состояния оборудования
Электронный журнал — это инструмент, который позволяет следить за реальным техническим состоянием узлов и агрегатов. На основе данных журнала проводится анализ и формируется тренд изменений технического состояния, прогнозируется дата выхода оборудования из строя по причине износа. На основе этих данных прогнозируется дата предупреждающего аварию ремонта, его объем и ориентировочная стоимость. Электронный журнал состоит из двух частей: журнала состояния в межремонтный период (по итогам неразрушающей диагностики) и журнала состояния в период ремонта (оценивается состояние до и после).
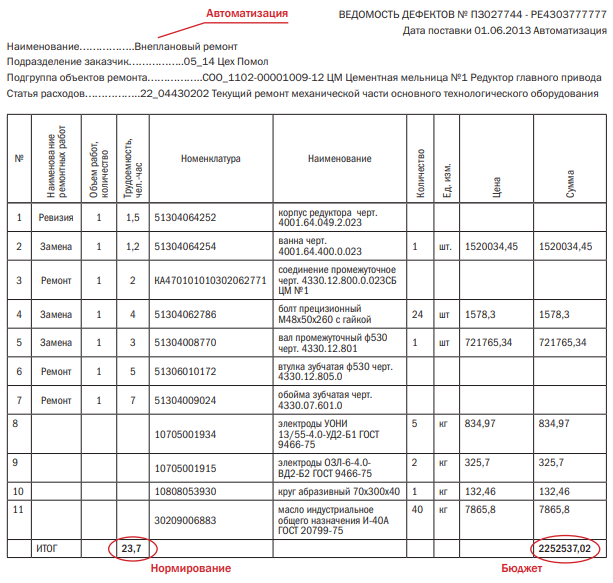
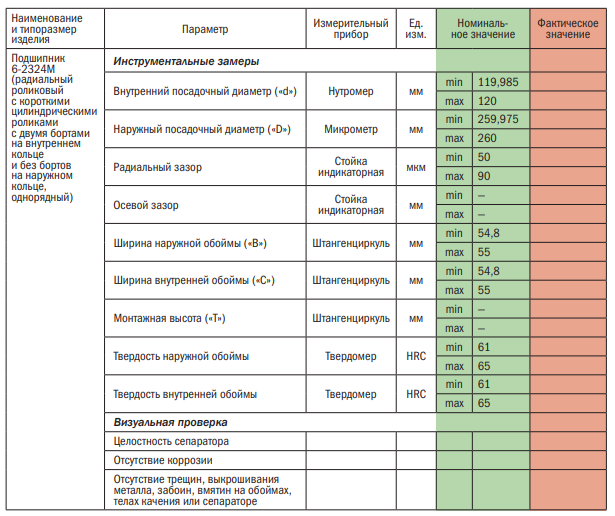
Данные в журнал попадают в три этапа.
- В каталоге оборудования необходимо выбрать тот узел или его части, на которых проводятся замеры, и распечатать формуляр для проведения замеров, в котором указано, что мерить, чем мерить и каковы номинальные значения. Заполняются вручную только фактические значения, полученные в конкретном промежутке времени (рис. 3).
- Необходимо произвести замеры на оборудовании по формуляру.
- Занести данные о фактическом значении параметров в текущем промежутке времени в Axapta. Форма занесения данных в ERP-системе была сделана максимально удобной. При выборе нужного узла все параметры появляются автоматически c номинальными значениями — остается только заполнить поле «фактическое значение» и сохранить данные (рис. 4.).
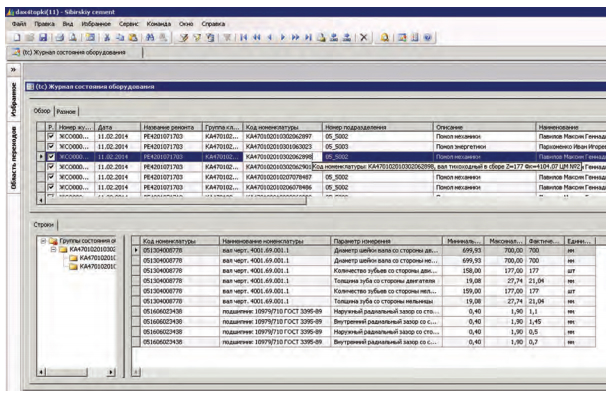
На основе полученных данных Axapta формирует отчеты в Excel по требованию пользователя. В любое время механик или директор могут оценить состояние оборудования на текущий момент в простой и удобной форме.
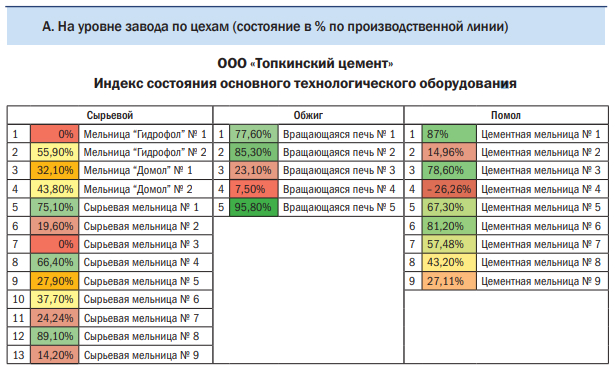
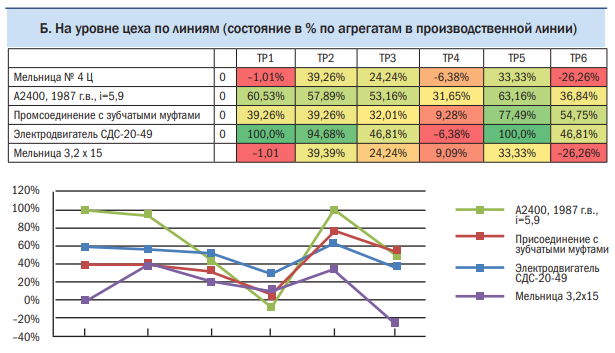
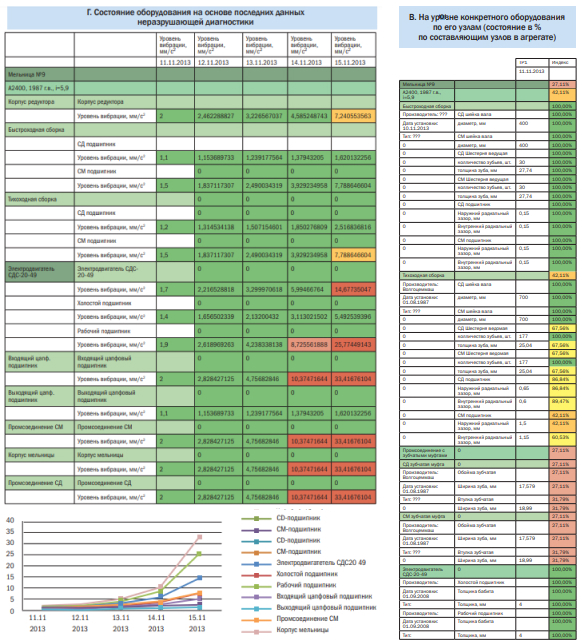
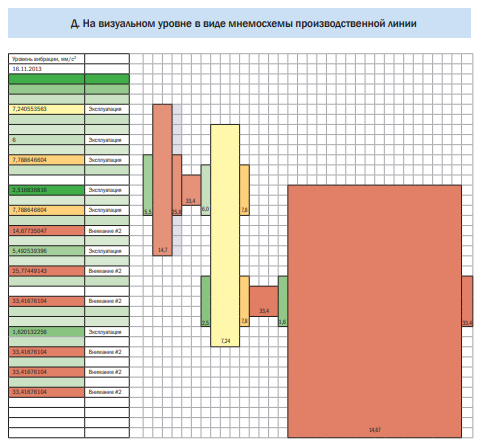
Третий блок в модуле ТОиР — история ремонтов оборудования и ее анализ. Оценка рисков в будущих периодах
Блок истории ремонтов в Axapta на данный момент реализован стандартным функционалом нашей ERP-системы — это перечень закрытых производственных заказов по ремонту оборудования, которые хранятся в системе. Через каталог оборудования можно перейти к таблице, в которой собраны все производственные заказы, и путем фильтров по коду единицы оборудования получить искомое. Печатная форма производственного заказа — ведомость дефектов. В ней содержится вся необходимая для анализа информация: дата ремонта, его вид, его состав, используемые материалы и их стоимость. Стоимость услуг можно найти по коду ремонта в справочнике актов выполненных работ. Данный механизм в системе ТОиР ОАО «ХК «Сибцем» еще не доработан до конца, поэтому не очень удобен. Планируется создать алгоритмы анализа данных из производственных заказов и актов выполненных работ и удобные формы отчетов по ним.
Четвертый блок — журнал дефектов оборудования
Журнал дефектов оборудования на данный момент представляет собой простую форму в Axapta для занесения информации о дефектах с функцией оповещения о выявленном дефекте.
Бригада ремонтной службы предприятия, которая занимается ежесменным техническим обслуживанием оборудования (обходы, визуальный контроль, ревизия), при выявлении дефекта должна занести о нем информацию в модуль ТОиР. В зависимости от присвоенного статуса на почту главного специалиста отправляется информационное письмо о месте возникновения дефекта и его характеристиках. Главный специалист принимает решение о методах и способах его устранения.
Блок «Журнал дефектов» также находится в разработке. В перспективе оптимизация блока в части создания классификации дефектов и справочника, а также алгоритмов взаимодействия с другими блоками в модуле.
Пятый блок — автоматическое управление периодическим техническим обслуживанием (ПТО)
Данный блок позволяет управлять техническим обслуживанием оборудования в реальном времени. Он был реализован посредством решения следующих задач:
- нормирование материалов и операций по проведению ПТО оборудования;
- привязка к наработке по времени;
- автоматизация процесса в части документального оформления процесса.
Таким образом, имея журнал норм по времени проведения обслуживания (в зависимости от наработки в часах), нормы материалов и операций, система сама планирует проведение ПТО, формирует производственный заказ и отправляет его на почту всем участникам процесса за сутки до начала проведения работ, а именно: профильному специалисту цеха, кладовщику, директору подразделения сервисного предприятия на активе.
Бригада рабочих сервисного предприятия получает данный заказ от своего директора и приступает к работе. Кладовщик снабжает бригаду материалами. Профильный специалист (механик или энергетик) осуществляет контроль и принимает работу, закрывает заказ в системе.
Перспективы развития
Создаваемый в ОАО «ХК «Сибцем» модуль ТОиР на базе Axapta 4 еще не завершен и требует дальнейшей разработки. Существующая версия позволяет решать ряд локальных задач и оптимизировать часть бизнес-процессов в сфере технического обслуживании и ремонта оборудования. В дальнейшем перед проектной командой стоят следующие задачи:
- Создание алгоритмов взаимодействия между блоками в модуле ТОиР, которые позволят в автоматическом режиме формировать графики ремонта оборудования в краткосрочной перспективе (квартал—год) на основе данных о реальном техническом состоянии и прогнозе критических изменений на оборудовании;
- Создание механизмов расчета рисков и управления ими на основе иерархии оборудования в производственном процессе;
- Автоматизация процесса — датчики наработки, планшетные компьютеры, дополнительное оборудование для неразрушающей диагностики;
- Реорганизация ремонтной службы в Управляющей компании и на предприятиях — создание отделов технического анализа и планирования.
Павилов Максим Геннадьевич
1985 г.р. Ведущий инженер Департамента производства, обслуживания и ремонта оборудования ОАО «ХК «Сибирский цемент», руководитель проекта «Создание системы ТОиР оборудования цементных активов на базе Microsoft Dynamics Axapta 4».
В 2007 г. закончил Кемеровский государственный университет, в 2010 г. аспирантуру Института истории СО РАН.
В 2008—2009 гг. участвовал в качестве члена рабочей группы во внедрении ERP-системы SAP для ФСК ЕЭС, г. Москва.
Начал работать в ОАО «ХК «Сибцем» в 2011 году над проектом по созданию и внедрению современной системы ТОиР оборудования активов холдинга.
Должностные обязанности: планирование и контроль исполнения ремонтных программ цементных активов; взаимодействие с ремонтными службами предприятий, контроль их деятельности, контроль работы ООО «Торговый дом «Сибирский цемент» (снабжение) на предмет своевременной и качественной поставки запасных частей и услуг по ремонту.
Журнал Prostoev.NET № 1(2) 2015
Авторы: Максим Павилов, ведущий инженер ОАО «ХК «Сибирский цемент»
1 комментарий
Опыт работы ОАО «РКЦ «Прогресс» по повышению эффективности системы ТОиР станков с ЧПУ · 20.02.2021 в 15:17
[…] работоспособности оборудования, реструктуризации системы управления ремонтной службой, формированию системы технического обслуживания и […]
Комментирование закрыто.