Филиала «Металлургический комплекс» ПрАО «Донецксталь» – металлургический завод»
2015 год, 10-я конференция (видео в конце статьи)
Доклад будет посвящен анализу централизации ремонтной службы одного из крупнейших металлургических предприятий Украины.
Краткая характеристика предприятия:
- производственные мощности: чугун — 1,45 млн т в год, сталь — 1,5 млн т в год (в стадии реконструкции);
- крупнейший производитель товарного чугуна в Украине (около 60% доли рынка), один из крупнейших в СНГ;
- высокие технические показатели доменных печей (полная модернизация в начале 2000-х годов); современный уровень технологии доменной плавки;
- одни из первых в мире внедрили технологию вдувания пылеугольного топлива; одна из немногих компаний в СНГ, использующих эту технологию;
- технико-экономические показатели доменного производства одни из лучших в Украине и СНГ и соответствуют самым высоким мировым стандартам производства чугуна.
В соответствии со стандартом предприятия базовой стратегией технического обслуживания являлась стратегия планового проведения ремонтов, доставшаяся нам в наследство еще с советских времен. Тем не менее, когда начали разбираться по факту, для основного оборудования, скорее всего, применялась такая стратегия, когда остановки оборудования выполняются в соответствии с каким-то графиком, а объем работ и их необходимость, их содержание определяются в зависимости от фактического технического состояния. Для вспомогательного оборудования использовалась стратегия эксплуатации до отказа. Для технического оборудования решение о ремонте выполнялось на основе применения средств и методов технической диагностики. Этим занималось бюро диагностики и наладки «Донецкстали», в бюро 4 человека, сами можете представить, сколько техники 4 человека могут охватить.
Школа ТОиР — кузница мастерства
Интернет-проект «Школа ТОиР: кузница мастерства» направлен на решение вопросов управления производственными активами и формирования, совершенствования систем технического обслуживания и ремонта.
«Школа ТОиР: кузница мастерства» — это эффективное управление производственными активами вашего предприятия:
• внедрение прогрессивных стратегий технического обслуживания и ремонтов (ТОиР);
• оптимизация структуры ремонтной службы;
• совершенствование бизнес-процессов ремонтного обслуживания производства, разработка нормативно-технической документации;
• внедрение аналитических инструментов оценки эффективности ремонтного обслуживания производства;
• разработка и внедрение средств автоматизации ремонтных служб;
• оценка технического состояния оборудования (техническая диагностика), целесообразности его дальнейшей эксплуатации;
• обучение персонала и внедрение современных технологий ремонтного обслуживания производства.
Мы столкнулись с тем, что возможности ремонтной службы, по сути, были сильно ограничены: во-первых, это недоукомплектация штатов, во-вторых, финансирование, утвержденное согласно планам на верхнем уровне, осуществлялось не в полном объеме, соответственно, материально-техническое обеспечение ремонта оставалось не на высоте. К этому добавим высокий моральный и физический износ оборудования, что постепенно приводило к системному ухудшению технического состояния оборудования и, соответственно, к увеличению затрат на техническое обслуживание, к снижению производственных показателей. Если у оборудования состояние неважное, вероятность аварий повышается, эти аварии происходят, снижаются доходы предприятий. И в дальнейшем это повторяется, повторяется, и получается, что это не замкнутый круг, а замыкающаяся такая спираль, которая сжимает, как удавка, предприятие.
На предприятии был характерный для многих смешанный способ организации ремонтного обслуживания, при котором имеются децентрализованные ремонтные службы в цеху и централизованная ремонтная служба, то есть какие-то подразделения ремонтников под отделом главного механика.
Способ организации ремонтного обслуживания:
- децентрализованные ремонтные службы производственных и вспомогательных подразделений;
- централизованная ремонтная служба, состоящая из:
— отдела главного механика (ОГМ) — подразделения, осуществляющего общую координацию ремонтного обслуживания оборудования предприятия;
— ремонтных подразделений (цех по производству ремонтов (ЦПР) и цех по ремонту металлургических кранов (ЦРМК));
— производственных подразделений (литейный цех, механический цех и цех металлоконструкций).
У предприятия были свои особенности ремонтной службы: децентрализованные ремонтные службы административно подчинены начальникам соответствующих подразделений, а функционально — ОГМ, что приводит к неоднозначности при определении приоритетности решаемых задач; децентрализованные ремонтные службы взаимодействуют с коммерческими и прочими службами предприятия как самостоятельно, так и через ОГМ, что значительно усложняет структуру связей, реализуемые бизнес-процессы, а также приводит к отсутствию чёткого разделения задач и ответственности, к их дублированию; всё более широкое распространение получает практика привлечения подразделений ОГМ для ремонтного обслуживания предприятий корпоративной сети. Мы начали разбираться с бизнес-процессами — что же там на самом деле в ремонтной службе предприятия происходит. Оказалось, что то, что написано, не выполняется, а если выполняется, то имеется целый ряд замечаний по этому поводу. Все варилось в каком-то своем котле, процессы запускались то по телефонным звонкам, то по бумагам. Не было никакой ясности в процессах, и это была одна из задач, которую мы решали в процессе централизации.
Для оценки эффективности ремонтного обслуживания использовались пять параметров.
- Выполнение целей в области интегрированной системы менеджмента качества, экологии и охраны труда (факт/план).
- Устранение замечаний в области интегрированной системы менеджмента качества, экологии и охраны труда (устранено/выявлено).
- Бесперебойность работы основного и кранового оборудования (длительность аварий / длительность работы).
- Выполнение графиков ТОиР (факт/план).
- Выполнение планов производства производственными подразделениями ОГМ (факт/план).
Обратите внимание, что только третий параметр, по сути, характеризует эффективность работы оборудования. И ничего не говорится про финансы. Основная цель системы технического обслуживания и ремонта — это обеспечение заданного уровня безаварийной работы оборудования с минимальными затратами.
Осознание руководством ситуации, которая сложилась на предприятии, потребовало, скажем так, принятия кардинальных и срочных мер для выхода из кризиса ремонтной службы. Для этого был выбран путь изменения способа организации ремонтной службы. Не могу сказать, что в данной ситуации это был единственно правильный путь, потому что — это сугубо мое мнение — эту систему надо менять комплексно.
Задачи централизации и средства их решения
Задачи
- Снижение уровня отказов и простоев механического оборудования.
- Сокращение численности ремонтной службы предприятия.
- Увеличение объёмов и видов ремонтных работ, выполняемых собственными силами.
Средства решения
- Изменение структуры ремонтной службы предприятия.
- Совершенствование бизнес-процессов ремонтного обслуживания производства.
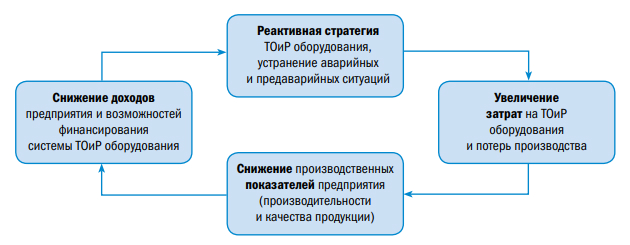
При сокращении численности ремонтной службы происходило не только сокращение людей, но и анализ работы подрядчиков, т.е. можно же отказаться от подрядчика, выполнявшего работы, которые не могли охватить своими силами, и выполнять их своими сотрудниками. Эту задачу можно было решить более оптимальным распределением загрузки.
Также мы справились с задачей снижения уровня отказа и простоев, хотя поначалу представители руководства ремонтной службы предприятия говорили о том, что давайте хотя бы обеспечим тот уровень аварийности, который у нас был.
Хронология централизации
- 22.11.2010 — начало работы над программой централизации, сбор и анализ информации о ремонтной службе предприятия, предложений участников ремонтного обслуживания производства, разработка проекта программы централизации;
- 16.12.2010 — начало обсуждения проекта программы централизации, корректировка, согласование и утверждение;
- 19.01.2011 — издание приказа о частичной централизации ремонтной службы предприятия в соответствии с утверждённой программой;
- январь—март 2011 — подготовка нормативно-технической базы для работы в условиях после централизации ремонтной службы предприятия;
- 1.04.2011 — выполнение централизации ремонтной службы завода, упразднение структуры ОГМ и создание на её базе МРК, перевод персонала из ремонтных служб цехов в подразделения МРК, введение в действие новой нормативно-технической базы;
- октябрь—декабрь 2011 — комплексный анализ результатов централизации.
Основные решения централизации:
- на базе ОГМ и его подразделений создать механоремонтный комплекс (МРК);
- выполнить частичную централизацию персонала ремонтных служб двух основных производственных цехов (доменного и мартеновского);
- для обеспечения выполнения работ по техническому обслуживанию оборудования полностью укомплектовать дежурные бригады централизуемых цехов;
- создать в централизуемых цехах оперативные бригады, работающие в дневную смену (V график), для решения текущих задач и выполнения подготовки к ТОиР;
- перевести в МРК 80 человек (рабочих и ИТР) из числа персонала централизуемых цехов, работающего по V графику;
- сократить в централизуемых цехах штатные единицы ремонтной службы, фактически не укомплектованные персоналом;
- внести изменения в стандарт предприятия, регламентирующий обеспечение качественной работы механического оборудования, для совершенствования бизнес-процессов ремонтного обслуживания производства, в том числе в части документооборота.
На весь проект нам дали полгода. Из них два месяца ушло только на разработку программы, утверждение, согласование и обсуждение. А кроме того, все средства могли носить исключительно организационный характер. Применение каких-то средств технической диагностики дополнительно и способы материальной мотивации персонала — в нашем распоряжении были только эти инструменты.
Надо отметить, что был выполнен очень большой объем работы по описанию бизнес-процессов ремонтной службы предприятия, был заново переработан и по сути создан новый стандарт предприятия по обеспечению качественных работ механического оборудования, были пересмотрены должностные инструкции, штатное расписание и только после этого в апреле 2011 года централизация была признана завершенной. Завершилась она упразднением структуры отдела главного механика и формированием на ее базе механоремонтного комплекса, в этот же момент произошел перевод персонала из ремонтных цехов в ремонтные комплексы. Плюс была введена новая нормативная база, на основании которой работала новая ремонтная служба. По итогам централизации был выполнен анализ, через полгода еще, потом еще через несколько месяцев.

Было очень большое опасение, что у нас вырастет аварийность, т.к. ремонтников забрали, они не смогут отказы устранять, и появятся отказы, которые носили скрытый характер. На самом деле по цифрам можно увидеть, что результата мы достигли: по количеству отказов сокращение порядка 25%, по потерям сокращения на 45%.
Что касается численности персонала, то мы ожидали потери персонала порядка 20—30%. На самом деле к 1 апреля мы потеряли половину персонала. Половина людей просто ушла. Дальше в течение 2011—2012 годов ушло еще процентов 15. Это связано с условиями труда. Если раньше человек сидел в своей машине, когда надо — пошел, когда не надо — сидит и занимается своими делами, то теперь, оказавшись в централизованной ремонтной службе, он вынужден был постоянно бегать с одной точки на другую. И те люди, которые были балластом ремонтной службы, отсеялись сами.
Еще один фактор, на который хочу обратить внимание. Когда мы в ЗМК из мартеновского цеха перевели полностью участок по ремонту металлоконструкций мартеновской печи, то есть более 20 работников, то из этих работников не потеряли почти никого, взяли мастера, всех его подчиненных, их переподчинили в отдел главного механика, и потерь штата практически не было. Среди тех людей, которых мы выдергивали по 1—2 с участков, потери были наибольшие, потому что у цехов была возможность определять, кого отдавать, соответственно, они отдавали тех, кого могли. Получился очистительный эффект централизации.
В связи с тем, что очень большая часть персонала до ремонтного комплекса так и не дошла, в середине 2011 года пришлось привлекать подрядчиков для технического обслуживания текущих ремонтов. Дальше волевым решением руководства запретили привлекать подрядные организации, хотя были попытки показать, что привлечение подрядчиков выгоднее экономически, чем работа собственными силами (и если смотреть по чистым цифрам, получилось, что выгоднее привлекать подрядчиков). Поэтому в конце 2011 года и в дальнейшем для технического обслуживания текущих ремонтов внешние подрядные организации уже не привлекались, только для выполнения капитальных ремонтов, где на короткий срок нужны большие человеческие ресурсы, либо для выполнения каких-то специфических работ, которые требуют соответствующей квалификации либо какого-то инструмента, техники, средств, которые в распоряжении механоремонтного комплекса отсутствуют.
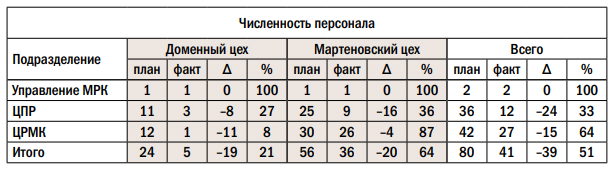
Теперь о выводах, к которым мы пришли в результате централизации. Сейчас идет второй этап централизации, поэтому очень важно понять и обобщить тот опыт, который мы получили на первом этапе. Какие ошибки допустили, что могли сделать лучше?
Выводы:
- целесообразно провести централизацию ремонтной службы предприятия, в особенности в условиях кризисных и посткризисных явлений, для повышения эффективности управления производственными активами;
- возможно обеспечить безаварийную работу оборудования в условиях централизации при достаточной комплектации штата централизованных ремонтных подразделений;
- вероятны значительные потери персонала при рассредоточенной централизации, что обуславливает целесообразность предварительного разделения персонала, работающего посменно в дежурном режиме, от персонала, работающего в дневную смену (V график), с дальнейшей централизацией последнего;
- допустимы альтернативы при выполнении работ по техническому обслуживанию и текущим ремонтам силами внешних подрядных организаций либо силами предприятия при достаточной комплектации штата централизованных ремонтных подразделений;
- целесообразно постепенно и непрерывно вести работы по совершенствованию системы ТОиР оборудования;
- необходим значительный объём работ по оптимизации бизнес-процессов, осуществляемых ремонтной службой предприятия, для повышения эффективности управления производственными активами;
- необходимо внедрение системы общепроизводственного обслуживания оборудования (ТРМ) в условиях централизации ремонтной службы предприятия и обучение технологического персонала принципам и методам технического обслуживания оборудования;
- целесообразно внесение изменений в систему оплаты труда централизованных ремонтных подразделений с установлением взаимосвязи с показателем безаварийной работы оборудования предприятия для повышения мотивации в качественном выполнении работ по ТОиР;
- целесообразно централизованное управление материально-техническим обеспечением ТОиР с целью оптимизации распределения выделяемого финансирования.
Журнал Prostoev.NET № 4(13) 2017
Автор: А. В. Сидоров, руководитель проекта «Школа ТОиР: кузница мастерства»