Опыт внедрения системы управления техническим обслуживанием и ремонтами на базе «1С:ТОиР»
Техническое обслуживание и ремонты (ТОиР) оборудования любой компании, а особенно — производственной, являются важнейшим вспомогательным бизнес-процессом компании.
Особенности работы предприятий добывающей отрасли, связанные в том числе и с требованиями обеспечения непрерывности и безопасности производства, предъявляют повышенные требования к системе управления ТОиР, причем как в части нормативно-правового регулирования, так и в части ее автоматизации.
Мы расскажем о нашем опыте внедрения системы управления ТОиР в ООО «Иркутская нефтяная компания» (ИНК), которая является одним из крупнейших независимых производителей углеводородного сырья в России.
Компания занимается геологическим изучением, разведкой и добычей углеводородного сырья на месторождениях Восточной Сибири — в Иркутской области и Республике Саха (Якутия).
Формирование современной системы управления ТОиР предусматривает не только решение специфичных для ТОиР задач, но и широкую интеграцию системы с другими системами управления, внедренными в компании. В частности, при разработке и внедрении необходимо решить целый ряд интеграционных задач, в том числе:
- интеграция и взаимодействие компонентов ИС между собой;
- сбор, обработка и интерпретация больших массивов разнородных данных в реальном времени;
- визуализация информации и интегрированное моделирование;
- междисциплинарное взаимодействие специалистов и систем — интеллектуальных помощников для коллективного принятия решений.
Надежность оборудования — это свойство объекта производства сохранять значения эксплуатационных параметров, характеризующих способность выполнять требуемые функции в заданных режимах и условиях применения.
Наиболее эффективным является комбинированное применение различных стратегий обеспечения надежности:
- реактивное (реагирующее) профилактическое обслуживание (РПО);
- обслуживание по регламенту или плановопрофилактическое обслуживание (ППР);
- обслуживание по фактическому техническому состоянию (ОФС);
- проактивное или предотвращающее обслуживание (ПАО).
Именно комплексность позволяет учесть такие отраслевые особенности, как:
- капиталоемкость производства;
- высокие технологические риски и требования обеспечения безопасности;
- высокие затраты на ТОиР;
- высокая стоимость простоев при отказах оборудования.
Отрицательно влияющим фактором может являться отсутствие прозрачности в процессах деятельности ремонтных и обслуживающих подразделений.
Для обеспечения эффективности системы ТОиР в рамках цифровой трансформации используются различные инструменты трансформации:
- датчики и система АСУ ТП (датчики на оборудовании), обеспечивающие мониторинг показателей производственного оборудования в реальном времени, включая геодатчики и RFID-метки;
- использование мобильных устройств для сбора данных и оперативного взаимодействия работников служб ТОиР и информационных систем предприятия;
- ESB — единая сервисная шина данных для интеграции приложений;
- единая модель данных предприятия на базе MDMсистемы;
- визуализация и интеллектуальная интерпретация собранных данных;
- создание интерактивных 3D-моделей месторождения;
- внедрение элементов интеллектуальных систем-помощников для планирования, прогнозирования и принятия решений.
База любого анализа — это данные. Только при наличии достаточно большого объема достоверных данных (в том числе — исторических) о параметрах работы различного оборудования возможно использование предиктивных моделей для анализа состояния и прогноза эффективности работы.
Такие модели динамического анализа позволяют установить причинно-следственные связи и способны прогнозировать возникновение нештатных аварийных ситуаций. Это позволит специалистам правильно и эффективно планировать профилактическое обслуживание и ремонты оборудования — не допускать аварийных остановок и потерь добычи.
При установке датчиков на оборудование необработанные данные с контрольно-измерительных приборов поступают в специализированные системы АСУ ТП, после чего эта информация может быть передана в систему управления надежностью для дальнейшего интеллектуального анализа.
Датчики GPS и ГЛОНАСС могут быть использованы для:
- удаленного геомониторинга и контроля состояния производственного объекта;
- геолокации оборудования для его поиска персоналом на местности «в полях».
Например, один из заказчиков после установки системы GPS-мониторинга выяснил, что спецтехника и рейсовый транспорт частенько заезжали в производственный магазин, вместо того чтобы выполнять прямой маршрут от точки А в точку Б, что, конечно же, не отражалось в путевом листе. Крюк был существенный. Несколько раз фиксировали, что машина по путевому листу работала на месторождении, а по мониторингу ездила в магазин для доставки продуктов рабочим на производственную площадку.
Корпоративная сервисная шина данных (Enterprise Service Bus) предназначена для построения распределенного информационного ландшафта предприятия. Программный продукт обеспечивает взаимодействие всех интегрируемых приложений в одном центре, объединяя существующие источники информации и предоставляя централизованный обмен данными между разными ИС.
Интеграция систем в один контур, реализация их взаимодействия и информационного обмена обеспечивают один из важнейших принципов цифрового месторождения — взаимодействие всех элементов комплекса в режиме онлайн.
Для унификации на уровне данных используются MDMсистемы — специализированное программное решение, которое помогает стандартизировать и поддерживать в качественном виде нормативно-справочную информацию (НСИ) во всех информационных системах (ИС) предприятия.
Для подготовки к цифровой трансформации в ИНК был выполнен большой объем работ.
- Внедрение системы НСИ и автоматизация процесса закупок, в том числе и закупок МТР для ТОиР, за счет чего была создана качественная основа ведения аналитики по базовой справочной информации.
- Формирование базы данных оборудования — как фундамент всей трансформации. От качества описания оборудования предприятия, полноты описания его характеристик и атрибутов зависит успешность дальнейших шагов.
- Автоматизация учета показателей эксплуатации для сбора, хранения и анализа сведений о техническом состоянии оборудования во время его эксплуатации (например, давление на входе/выходе, частота вращения, вибрация, уровень шума, температура и др.); всего используется порядка 150 контролируемых показателей.
- Автоматизация построения графиков ППР и регистрации дефектов, формирования заявок, выполнения и приемки ремонтных работ.
- Автоматизация планирования потребности в запасных частях, материалах и инструментах.
- Разработка отчетности для ежедневного анализа эффективности использования активов.
- Интеграция с подсистемами регламентированного учета, материально-технического обеспечения, бюджетирования.
При разработке и внедрении системы были решены некоторые специфичные задачи, о которых мы и расскажем далее.
Задача 1. Формирование единого процесса планирования, контроля исполнения и оценки эффективности ТОиР
Весь сквозной процесс управления ТОиР включает восемь процессов верхнего уровня (рис. 1).
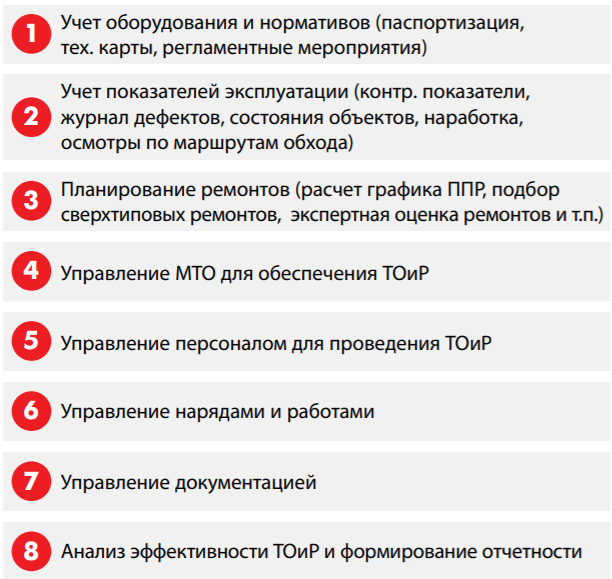
Все процессы верхнего уровня представляют собой части единого процесса управления, основанного на единой базе данных, общей концепции и нормативной базе управления.
Была сформирована (частично актуализирована, частично — создана вновь) нормативная и методологическая база ведения ТОиР.
В компании уже имелся значительный объем нормативных документов, регламентирующих ведение ТОиР. При разработке и внедрении системы ряд документов был актуализирован, а также были разработаны инструктивные документы по эксплуатации системы.
Задача 2. Интеграция с АСУ ТП
В процессе интеграции с АСУ ТП ORION+ были выполнены следующие работы:
- привязка низкоуровневых сигналов с датчиков к показателям эксплуатации оборудования;
- интерпретация и визуализация полученных данных в понятном для пользователя виде;
- мониторинг изменения показателей с помощью специализированного рабочего места;
- возможность оперативного реагирования на критические значения датчиков;
- информирование о различных событиях, связанных с работой оборудования.
Данные о работе оборудования накапливаются в АСУ ТП и по заданным временным параметрам (периодически) либо по достижении заданных параметров работы оборудования передаются в систему ТОиР. Примеры визуализации данных датчиков работы оборудования приведены на рис. 2.
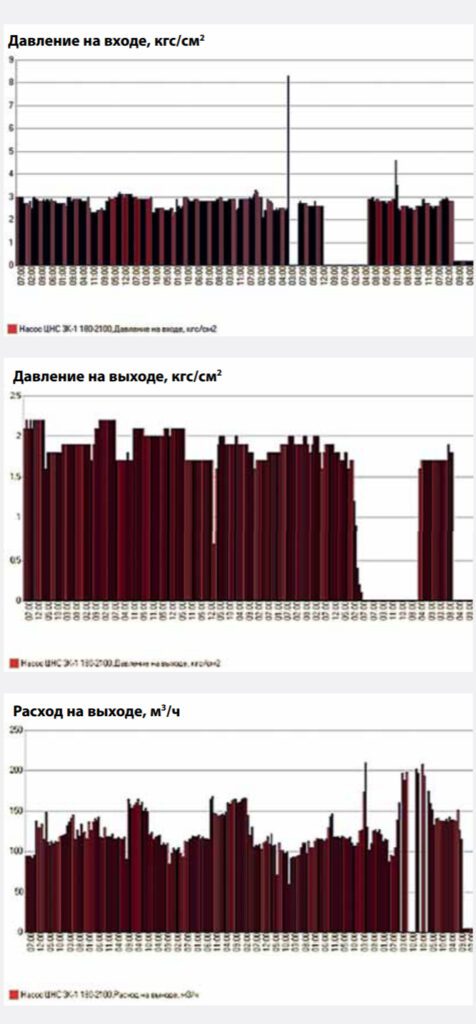
Задача 3. Формирование системы расследования отказов
Формирование системы расследования отказов и выявление корневых причин отказов включает:
- накопление статистических данных об отказах с целью совершенствования модели планирования;
- переход к проактивному планированию;
- создание интеллектуального помощника;
- формирование системы автоматического расчета уровня аварийного запаса;
- формирование заказа подрядчикам на устранение неисправности оборудования или ремонт оборудования при его выходе из строя;
- автоматическое формирование заявки на требуемые запчасти и материалы;
- публикацию оперативной сводки об отказах на корпоративном портале. Оперативная сводка является базой для совместной работы экспертов и совместного, децентрализованного принятия решений.
При отказах формируется Акт технического расследования отказа (рис. 3).
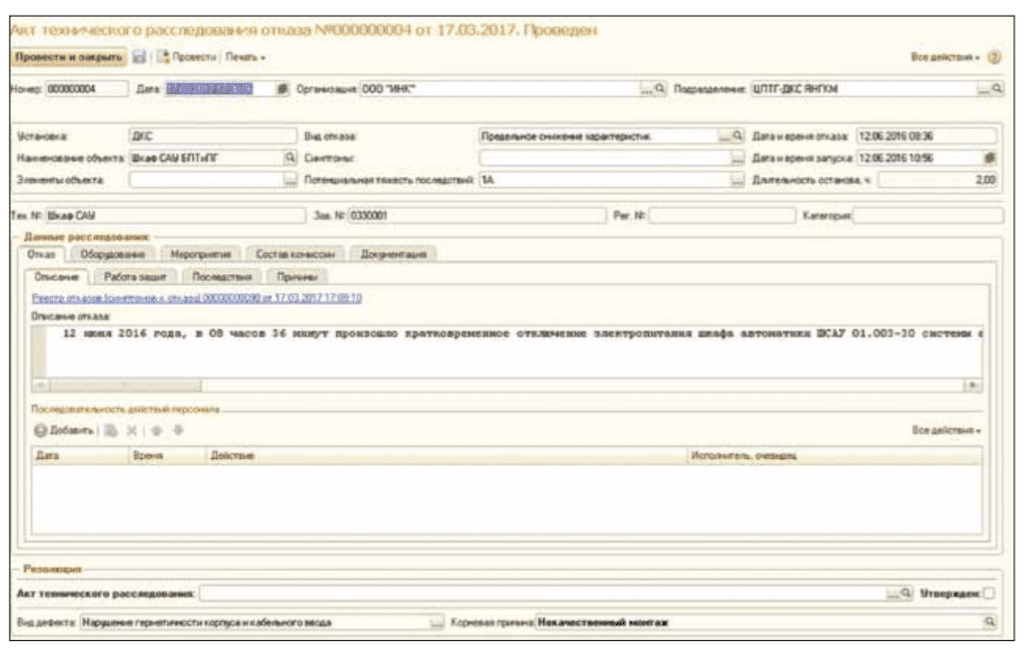
Разрабатываются классификаторы и проводится классификация и категоризация оборудования и систем — присвоение категорий критичности единицам оборудования и системам, обеспечивающим надежную и безопасную эксплуатацию технологических объектов (рис. 4). Данный этап важен для определения и совершенствования подходов к ТОиР оборудования в зависимости от тяжести последствий отказа тех или иных единиц оборудования или систем.
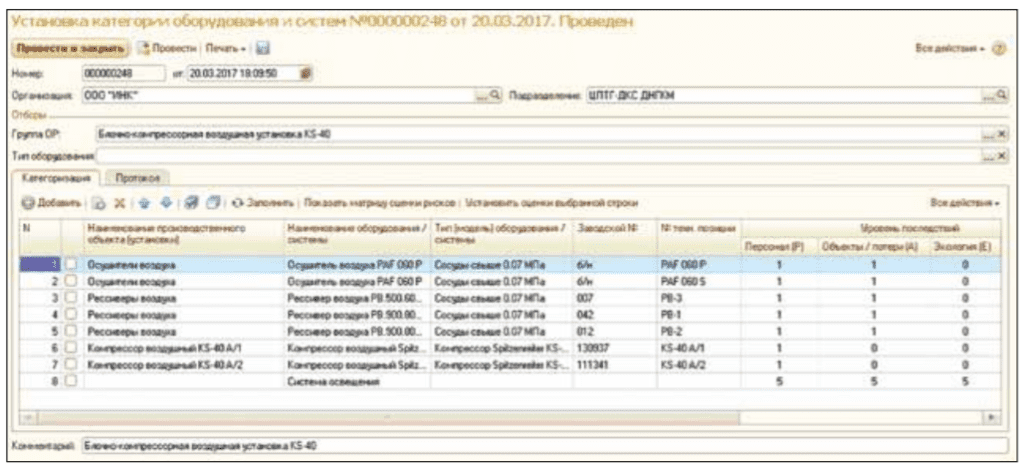
Задача 4. Анализ эффективности системы ТОиР
В системе формируется большое число отчетов, содержащих показатели эффективности ТОиР, в том числе:
- список оборудования с различной аналитикой;
- фактические затраты по объектам ремонта;
- эксплуатация: показатели, простои, дефекты оборудования, состояние оборудования и т.д.;
- показатели исполнения планов ремонтов, план-фактный анализ ППР, диаграммы ППР и т.д.;
- план-фактный анализ материально-технического обеспечения ТОиР;
- отчетность по показателям эффективности (KPI).
Система предоставляет широкие возможности построения аналитической отчетности по всем основным процессам ТОиР как в текстовом и табличном, так и в графическом виде (см., например, рис. 5).
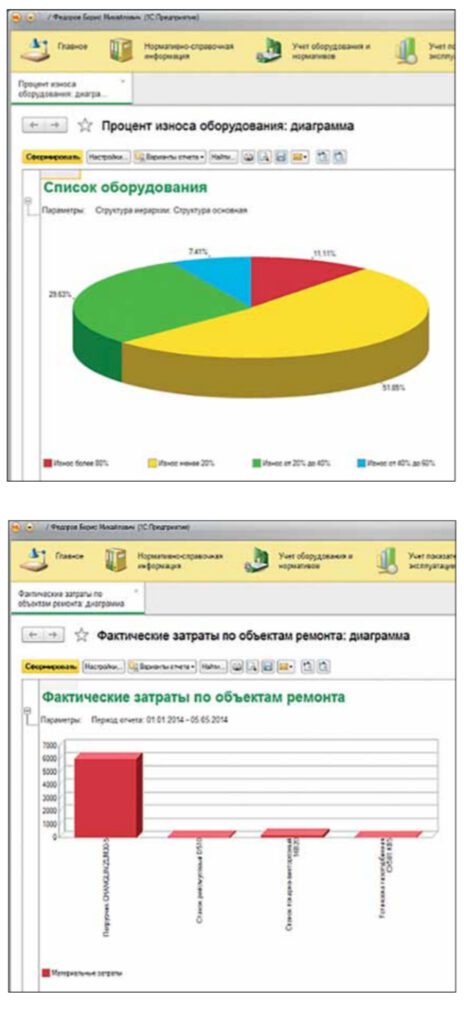
В системе формируется большое число отчетов по проведению ТОиР — как регламентированных (типовых), так и дополнительных (табл. 1).
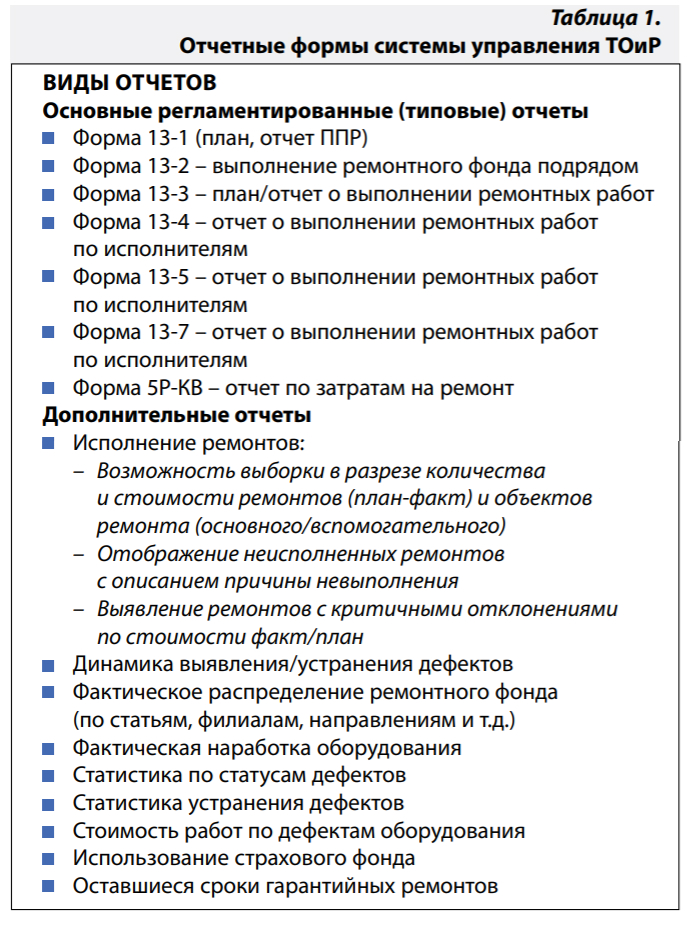
В дальнейшем предполагается развитие системы в следующих направлениях:
1. Внедрение мобильного клиента, обеспечивающего:
- регистрацию эксплуатационных показателей;
- формирование целевых отчетов для руководства и задач на выполнение ТОиР персоналу на местах;
- формирование уведомлений о событиях в системе, например, отказ оборудования или напоминание о предстоящем ремонте.
В рамках подготовки проработан порядок внедрения мобильного решения (см. рис. 6).
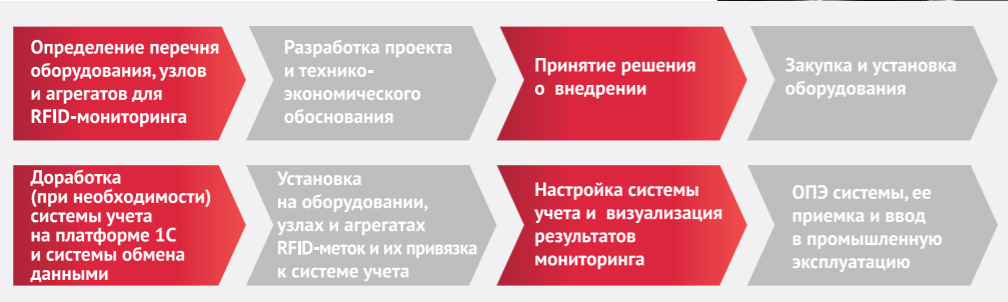
2. Моделирование различных стратегий ТОиР по типам оборудования и совершенствование существующих нормативов с целью оптимизации затрат на проведение плановых ремонтов.
3. Создание «Цифрового помощника» для помощи в принятии решений по следующей информации:
- рекомендации по реагированию и предотвращению возможных отказов;
- выявление взаимосвязей между условиями эксплуатации оборудования и неисправностями;
- построение вероятностных моделей и совершенствование ремонтной стратегии.
4. Формирование системы интеллектуального видеомониторинга с передачей оповещений о событиях в систему управления надежностью:
- оповещение о различных происшествиях (в том числе нетипичное поведение);
- оповещения о текущем состоянии оборудования и действиях персонала.
Таким образом, в статье мы рассмотрели важность задач по управлению надежностью оборудования в работе добывающих предприятий и роль системы ТОиР как необходимого элемента цифрового месторождения.
Журнал Prostoev.NET № 1(18) 2019
Подготовлено экспертами компании GRADUM